In the world of manufacturing and engineering, precision and consistency are paramount. With costs, quality, accuracy and performance all key project considerations, choosing the right manufacturing process can make all the difference.
Delivering high precision and consistency, photochemical etching is quickly becoming the preferred process for industries that require accuracy and quality.
Offering a number of advantages over traditional metal fabrication techniques, photochemical etching is ideal for producing parts with high-precision tolerances and complex geometries for a range of industries, from aerospace and medical, to electronics and defense.
As the trusted leader in photochemical and metal etching, the E-Fab team has a long history of engineering excellence and a focus on providing the highest level of quality.
In this article, we break down the reasons why photo etching services deliver unmatched precision and consistency compared to traditional manufacturing techniques.
What is Photochemical Etching?
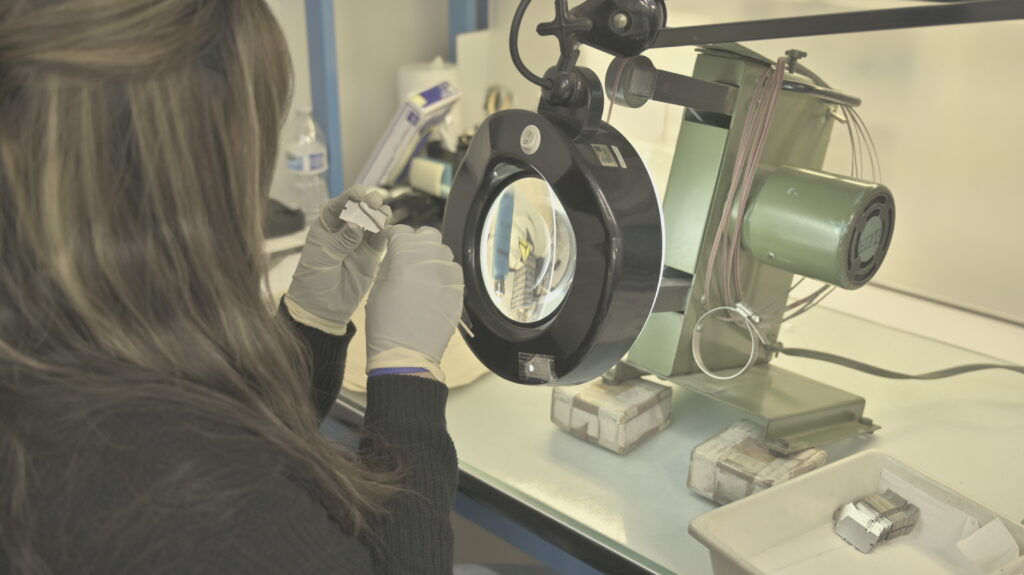
Photochemical etching, also known as photochemical machining, photo etching or chemical blanking, is a highly precise manufacturing process that enables the production of intricate metal components with exceptional accuracy.
The subtractive machining process uses chemical etchants to selectively remove metal from a thin sheet, creating intricate shapes, patterns, and features.
Unlike traditional methods, photochemical machining does not involve mechanical force or direct contact sheet metal, minimizing the risk of distortion, burrs, or stress-induced deformation.
First introduced in the 1960’s, the photo etching process was initially developed for fabricating intricate patterns on metal sheets to manufacture printed circuit boards. Over time, advancements in photochemical technology and materials led to its expansion into various industries, including aerospace, electronics, and medical.
Today, the photochemical etching process, has become a highly specialized and versatile manufacturing method, revolutionizing how intricate metal parts are produced. New sectors, including renewable energy, are leveraging the accuracy and efficiency of photochemical etching.
The Advantages of Photochemical Etching

Photochemical etching offers unparalleled precision, tight tolerances, and consistency in manufacturing intricate components and precision parts. With its cost-effective nature, material flexibility, and stress-free processing, photochemical etching has become preferred in industries that demand high-quality and complex parts.
Some of the key advantages delivered by the photo etching process include:
High Precision and Tight Tolerances
One of the key advantages of photochemical etching is its ability to achieve high precision and tight tolerances. The use of photolithography and chemical etching allows for the creation of intricate and complex geometries with extremely fine details. The accuracy of the photo tool ensures that the pattern is transferred onto the metal sheet with utmost precision, resulting in consistent and repeatable parts. This level of precision is difficult to achieve with other manufacturing methods, such as laser cutting or stamping.
Cost-Effective for Prototyping and Small Production Runs
Photochemical etching is a cost-effective solution for prototyping and small production runs. Unlike traditional machining processes that require expensive tooling and setup, photochemical etching does not incur significant upfront costs. The photo tool can be quickly produced at a fraction of the cost, making it an ideal choice for testing and validating designs before committing to large-scale production. Additionally, the digital nature of the photo tool allows for easy modifications and revisions, reducing the time and cost associated with design changes.
Material Flexibility
Another advantage of photochemical etching is its ability to work with various materials. The photochemical etching process can accommodate various metals, whether it’s titanium, stainless steel, copper, brass, or even exotic alloys. This flexibility in material selection allows for producing components with specific mechanical or chemical properties, meeting the unique requirements of different industries and applications. Furthermore, photochemical etching can process thin materials with ease, down to a fraction of a millimeter, without compromising on precision or quality.
Burrs and Stress-Free Manufacturing
Photochemical etching is a non-contact manufacturing process, meaning no physical force is applied to the material. This eliminates the formation of burrs, common in conventional machining methods. Burrs can affect the functionality and aesthetics of a component, requiring additional deburring operations. With photochemical etching, the chemical nature of the process ensures a clean and burr-free result, reducing post-processing requirements. Additionally, the stress-free nature of photochemical etching minimizes material distortion, allowing for the production of flat, warp-free parts.
Consistency and Reproducibility
Consistency and reproducibility are crucial factors in manufacturing. Photochemical etching delivers consistent results, thanks to its digital and automated nature. The photo tool ensures that every part produced is identical to the original design, eliminating variations that may arise from manual processes. Once the photo tool is created, the etching process can be repeated with high accuracy, ensuring the same precision and consistency throughout the production run.
While there’s no doubt that photochemical chemical etching offers numerous advantages, alternate, often traditional, manufacturing processes should still be considered.
Laser cutting has been popular because it uses a focused laser beam to cut through metal. Although laser cutting provides fast and precise results, it can also generate heat, potentially leading to thermal distortion and a narrower range of materials suitable for processing.
Another option worth considering is waterjet cutting, which utilizes a high-pressure jet of water mixed with abrasive materials. While waterjet cutting is effective for a wide range of materials, it may result in tapering edges and limited precision compared to photochemical etching.
Additionally, traditional mechanical methods like stamping and punching can be employed, but they may lack the intricate detail and complexity achievable through photochemical etching.
When it comes to metal etching, each alternative has its limitations, making it crucial to assess the project’s specific requirements and select the most suitable etching process accordingly.
When to use Photochemical Etching
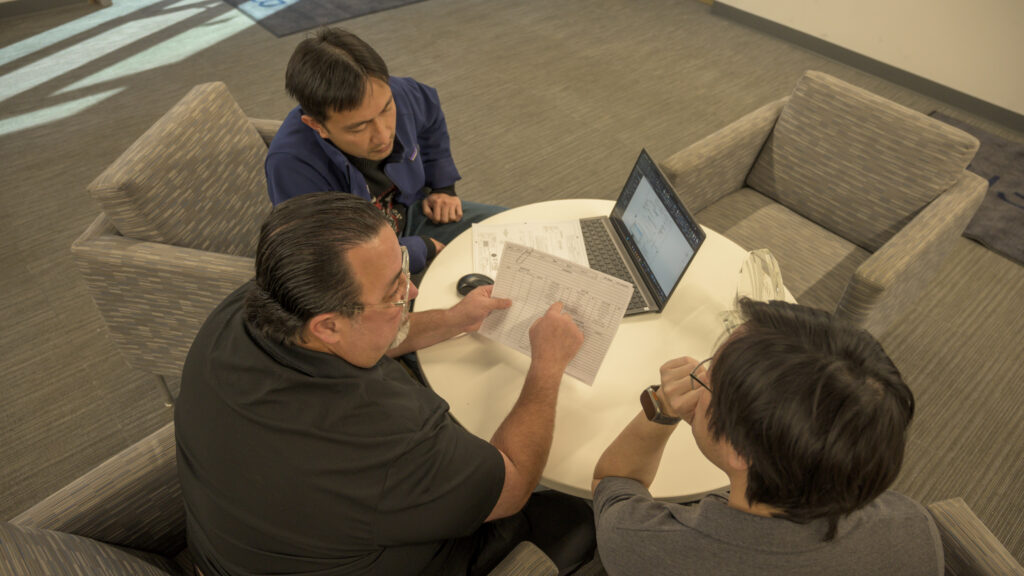
Affordable, fast and precise, photochemical etching is the ideal process for a number of situations. Boasting reduced set-up costs, rapid turnaround times and minimal errors, photochemical etching is preferred for applications across various industries.
The photochemical etching process is commonly used in applications that include:
Renewable Energy: Chemical etching is a highly effective and efficient process for creating various parts, including bipolar electrolyzer plates, cathodes, anodes, and shields.
Aerospace: Some of the aerospace parts that can be produced through this method of metal etching include intricate and lightweight metal components such as aircraft engine blades, turbine disks, fuel nozzles, heat exchangers, brackets, shims, electrical contacts, screens, filters, and connectors.
Medical: Photochemical etching allows for the creation of intricate and complex shapes with high precision and tight tolerances, ensuring the accuracy and reliability of medical devices that include implants, filters, meshes, stents, diagnostic test strips, electrodes, and more.
Semiconductor: Accuracy and reliability are essential when delivering parts such as shields, flexures, and contacts used in high-technology applications that power our communications, computers, and entertainment.
Materials that can be Processed by Photochemical Etching
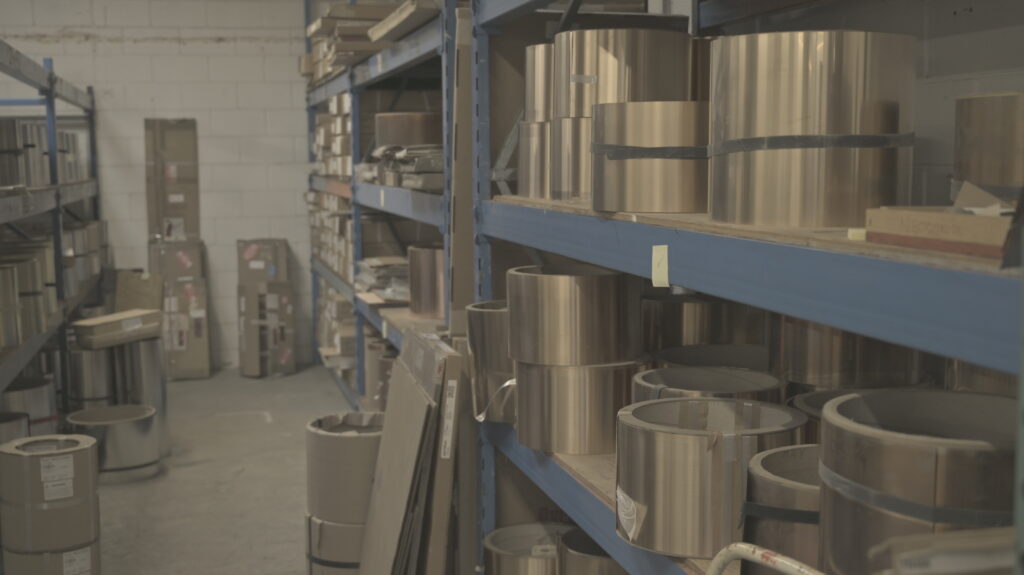
Renowned for its versatility as a manufacturing process, photochemical etching can be applied to various materials.
Some of the more popular materials that can be processed include stainless steel, copper, brass, aluminum, nickel, titanium, and more.
The versatility also extends to the thickness of materials you can process, with the ability to work with thin foils as well as thicker sheets. It can produce intricate designs and fine features with exceptional precision, even for materials as thin as a few microns. The precision level may vary for thicker materials, but the metal etching process can still deliver accurate and consistent results up to several millimeters in thickness.
Why Photochemical Etching is the Better Option for OEMs and Engineers
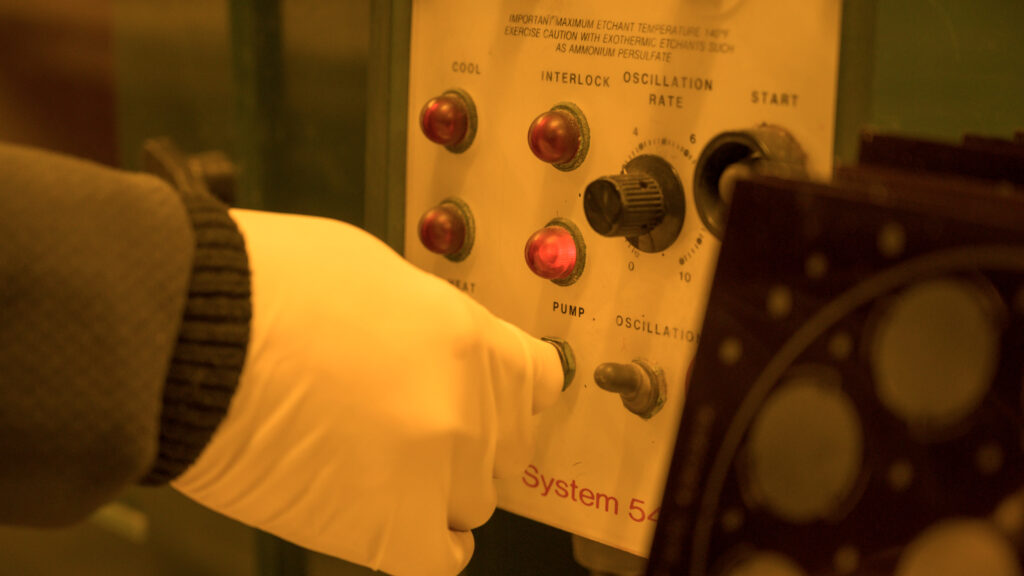
Photochemical etching has quickly become preferred due to its exceptional efficiency, high precision, and rapid turnaround time.
One of the main reasons why photochemical etching comes out on top is its cost-effectiveness compared to other metal fabrication methods.
A lot of that comes down to tooling. Digital tooling provides a streamlined process that allows for design modifications throughout the manufacturing stage, significantly reducing the overall project time and saving valuable time and money.
The Leader in Photochemical Etching Services
Renowned for delivering highly precise metal parts to various industries, E-Fab has come a long way in a short time.
At E-Fab, our engineers, manufacturers, and quality assurance specialists turn ideas into precision parts through collaboration, full engineering services, and expert machining processes.
A one-stop shop for businesses looking for precision, performance and all-round excellent service, talk to the team at E-Fab today to discuss your production needs.