Medical engineers understand better than anyone the need for precise, reliable components that meet stringent specifications while also contributing to the overall safety and effectiveness of the medical instruments they design.
However, with the miniaturization and intricate designs of modern medical instruments, most traditional machining methods fail to provide the precision required for medical component manufacturing. Delivering superior precision, customization, and cost-effectiveness, photochemical etching (PCE) has emerged as the preferred manufacturing method for engineers across a broad range of precision medical components.
An industry leader in photochemical etching (PCE), E-Fab, is a trusted partner for engineers looking for medical componentsthat meet the highest standards of quality and performance. Boasting more than 40 years of experience, they deliver precision components manufactured to the highest standards, enhancing the efficacy and safety of medical instruments.
In this article, we explore photochemical etching’s many advantages over traditional machining methods and why it’s the ideal process for crafting high-quality medical instruments.
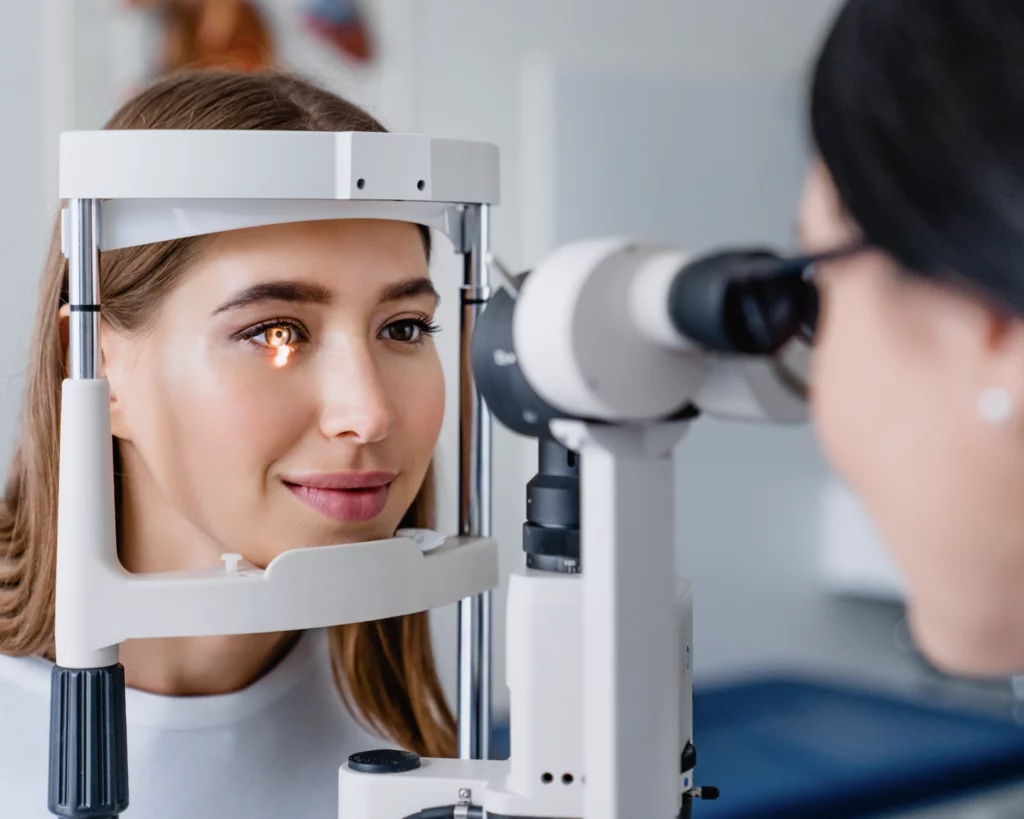
The Importance of Precision in Medical Instruments
From surgical tools to implantable devices, the modern medical instruments we now rely on require an extraordinary level of precision. With the health and safety of patients dependent on the functionality and reliability of these instruments, you need components with tight tolerances, intricate designs, and flawless finishes.
Let’s take instruments like scalpels, forceps, and stents as an example. These precision instruments need to be manufactured with extreme accuracy to perform their intended functions without causing harm to patients. In these applications, even the slightest deviation from design specifications can lead to serious consequences.
Unlike traditional machining methods, processes like photochemical etching provide the precision necessary to produce these critical components, ensuring that medical instruments meet the highest standards of quality and performance.
Advantages of Photochemical Etching for Medical Components
Photochemical etching is a subtractive manufacturing process that uses light-sensitive photoresist coatings and chemical etchants to produce highly precise metal components.
The process offers several key advantages for medical instrument manufacturing:
Unmatched Precision
PCE allows for the production of components with incredibly tight tolerances, often in the range of microns. This level of precision is essential for medical instruments, where exact measurements are crucial for ensuring the device’s functionality and safety.
Customization and Complexity
PCE enables the creation of intricate designs that would be difficult or impossible to achieve with traditional machining methods. Whether it’s producing fine-cutting edges for surgical instruments or creating complex geometries for implantable devices, the innovative process offers unparalleled design flexibility. This makes it an ideal choice for customized medical instruments that need to meet specific patient or procedural requirements.
No Burrs or Deformations
The chemical nature of the PCE process results in components with smooth, burr-free edges. This is particularly important for medical instruments, where surface finish can impact both performance and patient safety. Smooth, burr-free edges reduce the risk of tissue damage during surgery and ensure that implantable devices integrate seamlessly with the body.
Cost-Effective and High Scalability
Despite its high precision, photochemical etching (PCE) is a highly scalable and cost-effective manufacturing process, particularly for complex or customized components. The process eliminates the need for expensive tooling and allows for rapid prototyping and production, significantly reducing both lead times and overall manufacturing costs. Its scalability makes it ideal for both small batch and high-volume production, offering flexibility and efficiency at every stage. Unlike CNC machining or lasering, which produce one part at a time, etching of medical equipment through PCE can etch multiple parts simultaneously from a sheet of metal, greatly enhancing production efficiency.
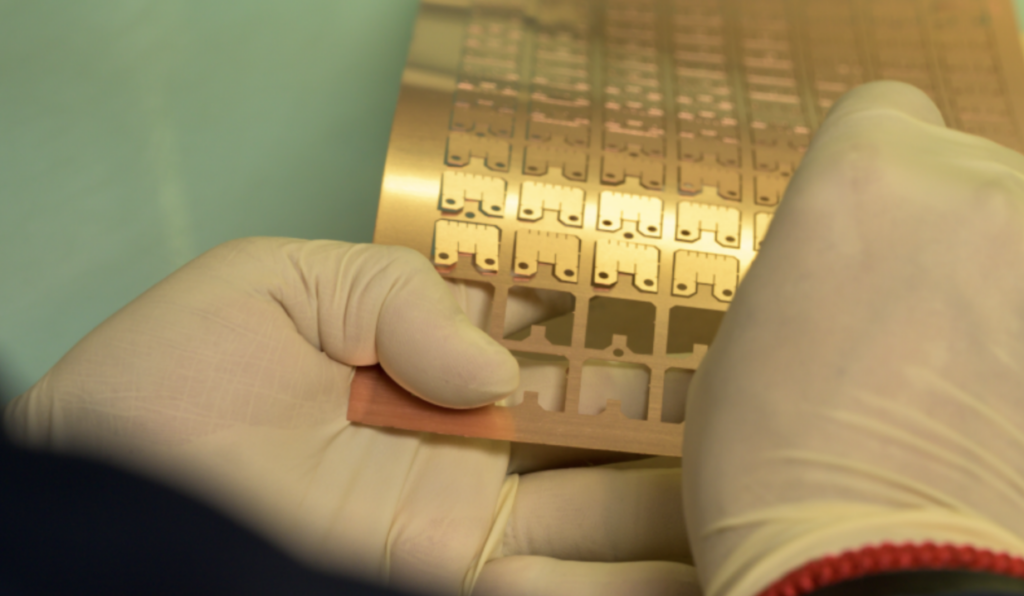
Material Compatibility
PCE works with a variety of materials commonly used in medical instruments, including stainless steel, titanium, tungsten, and nickel alloys. The process does not alter the metallurgical properties of the material, ensuring that the components retain their biocompatibility and mechanical strength.
Biocompatible Metals for Implantable Devices
Titanium is especially known for its biocompatibility, making it the ideal choice for implantable devices such as orthopedic implants, stents, and craniomaxillofacial applications. Its properties allow it to integrate seamlessly with the body, reducing the risk of rejection or adverse reactions.
Metals for External Medical Products
Stainless steel alloys are typically used for external medical products, such as surgical tools and equipment, due to their exceptional strength and resistance to corrosion. These properties make stainless steel ideal for instruments that require durability and reliability in sterile environments.
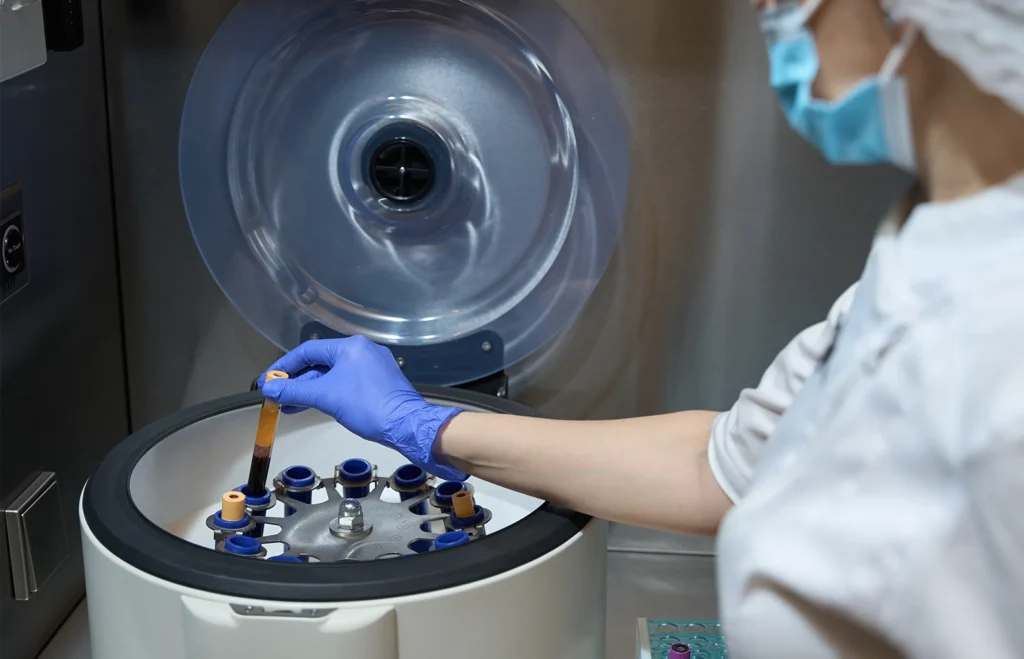
E-Fab’s Expertise in Precision Medical Machining
E-FAB has become a trusted partner for medical clients by providing specialized services and precision metal components that are essential for various medical applications.
Blending innovation and collaboration, we’re transforming the future of medical technology by providing customized, high-precision components that can be relied on for even the most extreme applications.
Backed by over 40 years of experience, our skilled engineers and operators are able to create custom medical device components with the greatest accuracy possible.
Our team of seasoned engineers works closely with clients from the initial design phase through to production, helping optimize designs for manufacturability and ensuring that medical components are not only precise but also practical for large-scale production.
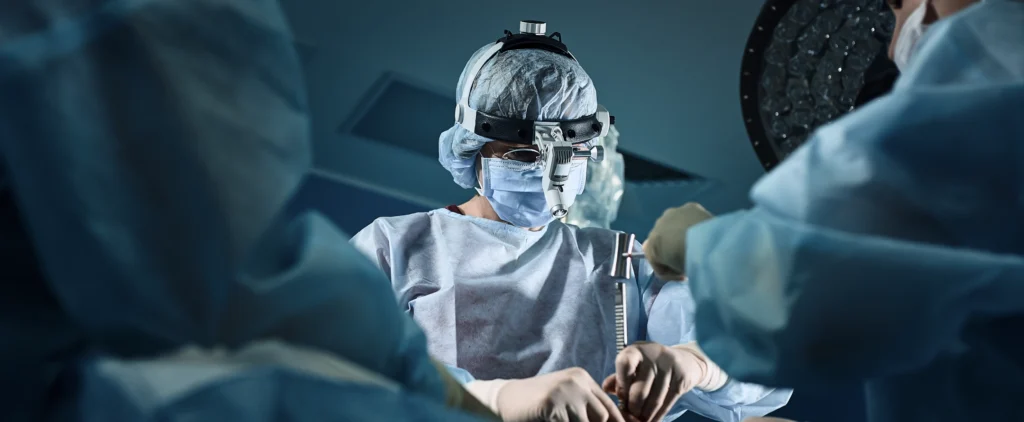
Custom Medical & Surgical Components
E-Fab sets the standard for high-quality medical care by consistently producing precise components that enhance the efficacy and safety of medical instruments. Our industry-leading capabilities include medical device etching, photochemical machining, high-frequency laminate processing, plating, finishing, and bonding.
With a proven ability to provide customized, high-precision medical parts for competitive prices, we’re helping to advance the medical field and improve patients’ quality of care and quality of life.
Our precise metal components designed specifically for medical applications include, but are not limited to:
- Medical sensor elements
- Customized medical device parts
- High-precision screens and filters for sterile medical environments
- Intricate components for medical equipment
- Precision components for medical sensors
- Miniaturized parts for medical device technology
- Medical instrumentation components
- Medical shims
- Anode and cathode grids
- Hearing aid components
- Stents and orthopedic bone implants
- Filters and sieves for laboratory or pharmaceutical equipment
In an industry where failure is not an option, we ensure the highest quality standards throughout our manufacturing processes. We’re ISO 9001:2015, ITAR, CMRT, and PCMI certified, ensuring all our components adhere to stringent quality control and compliance standards for medical devices.
Proven Experience in the Medical Industry – E-Fab’s Medical Machining Services
As a reliable and dedicated medical component supplier, E-Fab delivers superior precision components for a variety of critical medical applications.
For radiologists to provide a quality diagnostic service, they rely on precisely manufactured, reliable equipment. Required to perform a number of critical tasks from CT and MRI scans to X-rays and more, they need to know their components are mobile, accurate, reliable, and most importantly, safe.
Here at E-Fab our trusted team of medical device engineers provides only the highest quality parts such as collimators for CT scans, MRI table components, and anodes for X-ray systems. Our team of Quality Assurance professionals analyzes every part we send out to ensure each meets technical specifications and precise requirements.
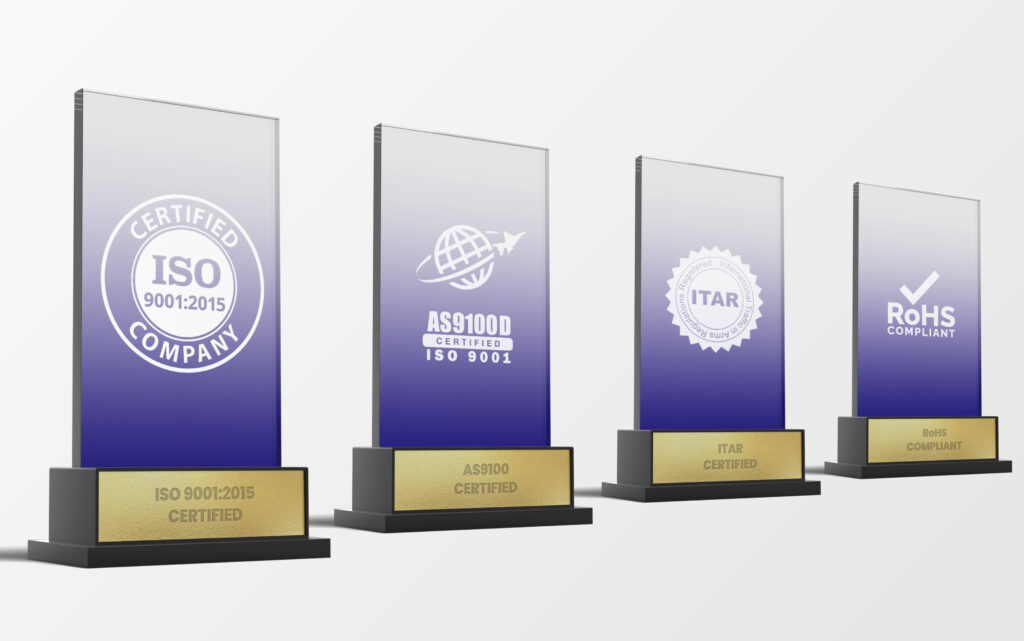
Why Partner with E-Fab for Medical Instrumentation
E-Fab has a long history of success in delivering precision components for the medical industry. Our commitment to innovation and quality has made us a trusted partner for engineers searching for precision-machined medical instruments.
What sets E-Fab apart:
Biocompatibility: Our photochemical etching processes can be tailored to work with biocompatible materials, such as titanium, stainless steel, and other medical-grade alloys, ensuring the components are safe for use within the human body.
Complex Geometries: Using our advanced photochemical etching techniques, we can create intricate and complex two-dimensional shapes, key for components in medical equipment and implants.
Rapid Prototyping: Our rapid prototyping capabilities are essential for developing and testing new medical devices and components before they enter mass production.
Cost-Effective Production: We help medical manufacturers achieve cost efficiencies through the cost-effective medium to high-volume production of precision components.
The Future of Precision Medical Machining
For engineers in the medical device industry, understanding the advantages of PCE can lead to better-designed instruments that meet the highest standards of quality and safety.
As the demand for advanced medical devices continues to grow, PCE will remain a critical manufacturing tool due to its ability to create precise medical device components for cutting-edge medical instruments that don’t just meet but exceed the quality and safety standards required to ensure patients receive the best possible health outcomes.
Leaders in the precision machining of medical components for a range of critical medical applications, E-Fab offers superior expertise, cutting-edge technology, and a commitment to delivering the highest quality products.
By partnering with E-Fab, you ensure that your medical components are manufactured to the highest standards, enhancing the efficacy and safety of your medical instruments.