Known as a remarkable refractory metal, molybdenum has quickly become a powerful and popular choice for precision manufacturing. But why is that?
The secret lies in its superior properties. Boasting a unique combination of high melting point, exceptional strength, excellent thermal and electrical conductivity, and corrosion resistance, molybdenum offers enhanced performance, durability, and reliability for components in critical applications across various industries. Its low coefficient of thermal expansion, high elastic modulus, and high melting point make it particularly suitable for high-temperature parts, such as carriers. Additionally, the material is often gold plated for bonding, enhancing its utility.
As a trusted leader in photochemical etching, E-Fab is a leader in manufacturing precision molybdenum parts. Our etched parts are integral to airplanes, rockets, satellites, and medical devices. Supplying a variety of components for aerospace and defense applications, we ensure our molybdenum stock is DFARS compliant.
In this article, we explore what makes this metal so special, the main benefits of using it in precision manufacturing, and its key applications across various industries.
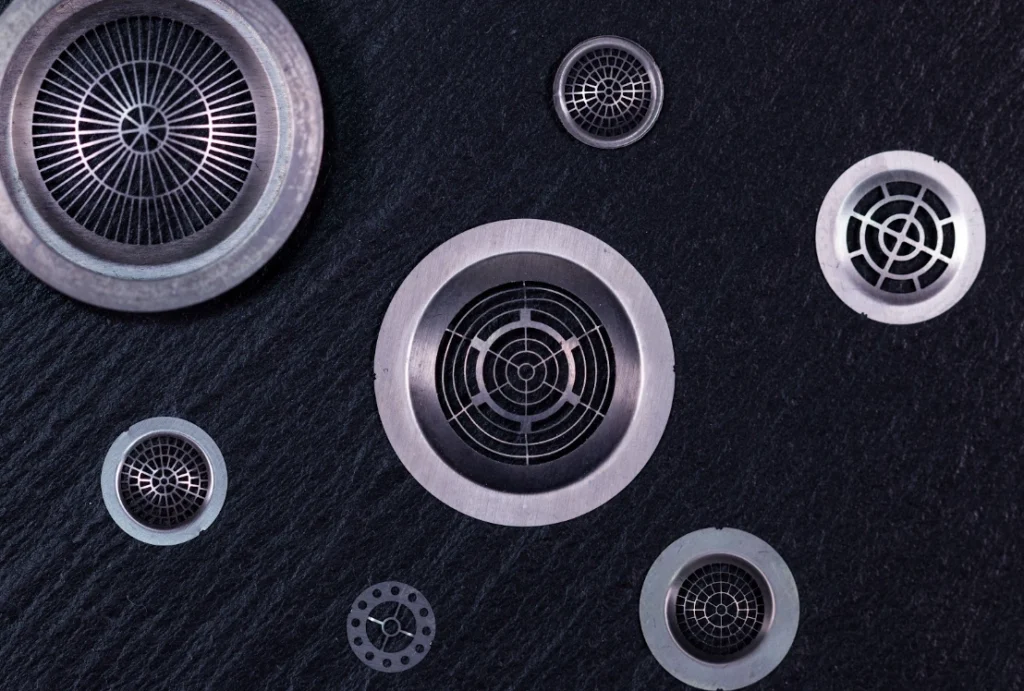
What is Molybdenum Metal?
Molybdenum—often referred to as Moly or Mo— is a refractory metal that comes in various alloys or mixtures, such as molybdenum-rhenium and molybdenum-copper.
Molybdenum is renowned for its impressive characteristics and properties, making it highly significant in various industrial applications. With a high melting point of 2,623°C (4,753°F) and exceptional thermal and electrical conductivity, molybdenum stands out for its ability to perform under extreme temperatures and conditions. It also possesses remarkable strength and hardness, coupled with excellent corrosion resistance.
Molybdenum’s exceptional properties make it an essential material in industries like aerospace, electronics, and energy, where extreme heat environments are common. Its applications include control or shadow grids, electrical contacts, and heat-resistant components.
Benefits of Molybdenum in Precision Manufacturing
With a unique blend of superior characteristics, molybdenum has become the proven choice for producing durable, high-performance components that can withstand extreme temperatures and harsh environments.
High Melting Point and Thermal Stability
One of the most significant benefits of molybdenum is its high melting point of 2,623°C (4,753°F). This property makes it ideal for applications that require materials to maintain their strength and stability at extreme temperatures.
Molybdenum components can withstand intense heat without deforming or losing their structural integrity. This is particularly valuable in industries such as aerospace, where parts must perform reliably under severe thermal conditions.
Corrosion Resistance
Molybdenum exhibits outstanding corrosion resistance, particularly against non-oxidizing acids. This property ensures that molybdenum components maintain their integrity and functionality in corrosive environments. In industries like chemical processing and oil and gas, where exposure to corrosive substances is common, molybdenum’s resistance to corrosion significantly extends the lifespan of equipment and reduces maintenance costs.
Excellent Thermal and Electrical Conductivity
Molybdenum’s excellent thermal and electrical conductivity is another reason for its widespread use in precision manufacturing. It can efficiently transfer heat and electrical energy, which is essential for components in electronic devices and high-temperature furnaces. Its ability to dissipate heat quickly helps prevent overheating and enhances the performance and longevity of electronic and aerospace components and systems.
Exceptional Strength and Hardness
Molybdenum’s impressive strength and hardness enhance the mechanical properties of alloys, making them more robust and wear-resistant. This strength is crucial for creating durable tools and components that can endure high-stress environments. For example, molybdenum is often used in the production of carriers, ribs, and tooling equipment that must maintain precision and resist wear over prolonged use.
Additional benefits: unique combination of physical properties and good mechanical properties at ambient temperatures, ease of plating, and compatibility with existing brazing and soldering techniques, make it the material of choice in the construction of solid-state electronics.
The Key Applications of Molybdenum in Precision Manufacturing
One of molybdenum’s most unique and attractive properties is its ability to withstand high temperatures without losing strength and structural integrity.
This property is used to manufacture parts and components for devices operating in extreme heat conditions across a number of leading industries, including:
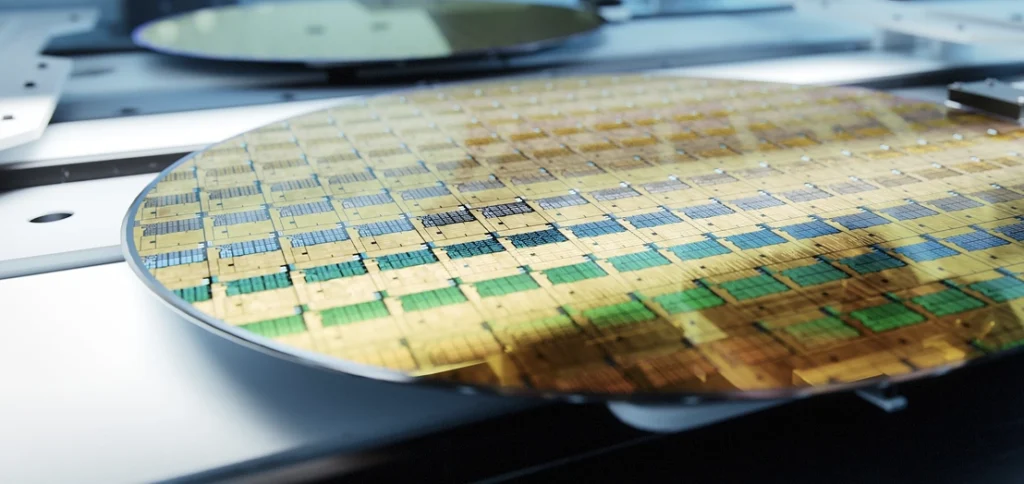
Semiconductors
Molybdenum is becoming a preferred material in semiconductor manufacturing due to its thin film resistivity. Thin film deposition is essential for device scaling of metal contacts, vias, and lines. Unlike other metals, molybdenum’s resistivity does not increase significantly when deposited as thin films, making it an ideal choice for advanced devices. Its mean-free path is better suited to the dimensions of features to be filled, outperforming tungsten, cobalt, copper, and other metals.

Aerospace
Molybdenum’s high thermal conductivity is crucial for microwave electronics, aiding in efficient heat dissipation for high-performance components. It’s also relied on for the manufacturing of high-temperature, high-stress components such as turbine blades and rocket nozzles.
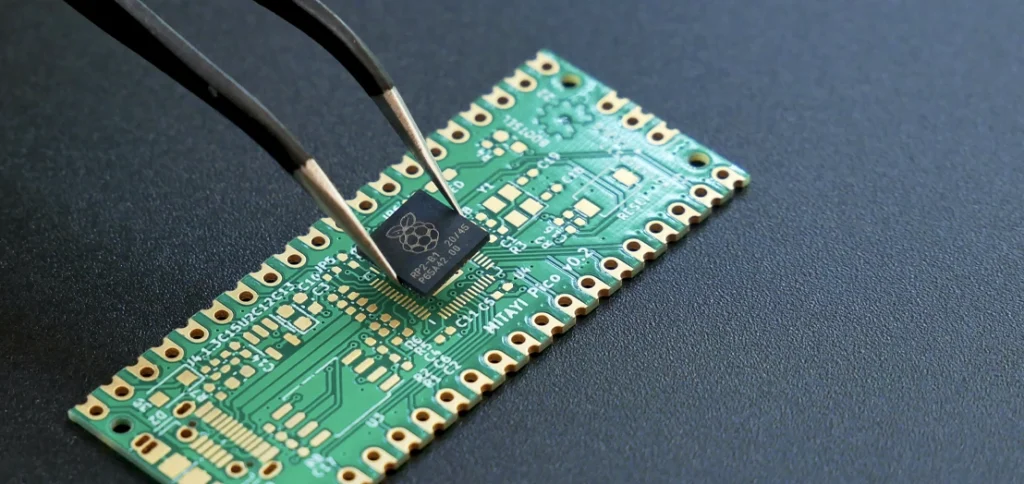
Electronics
Molybdenum is essential for semiconductor fabrication tools, where its exceptional properties guarantee high performance and longevity in the production of cutting-edge semiconductor devices. Its thermal and electrical conductivity also make it ideal for use in semiconductors, circuit boards, and other electronic components and microwave devices. EX: frequency filters, lithography
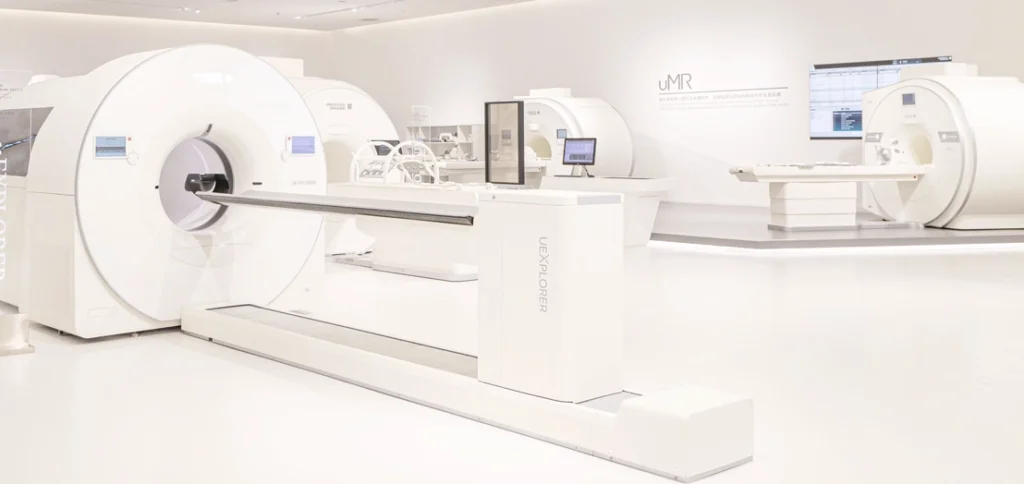
Medical
In the medical industry, molybdenum’s precision and durability make it ideal for manufacturing intricate 3D grids for advanced diagnostic and therapeutic devices. It’s also a valuable metal used in medical imaging equipment and devices that require precision and durability.

Energy
The metal’s ability to withstand high temperatures makes it ideal for ceramic heaters, ensuring consistent performance and durability. It’s also used to produce components for nuclear reactors and back contacts for thin-film solar cells.
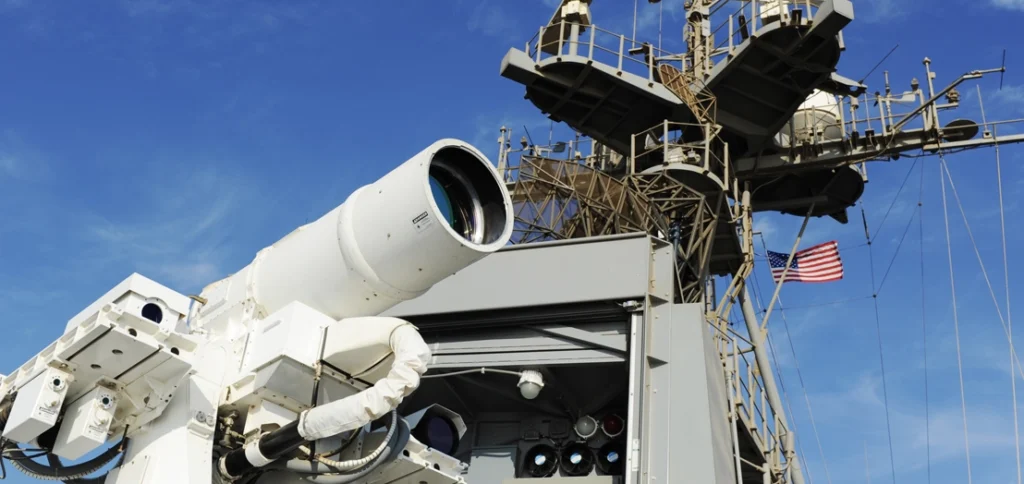
Defense
Molybdenum is used in electronic beam guns, where its high melting point and strength ensure reliability under extreme conditions. Additionally, molybdenum is utilized for shims, carriers, and antennas, all of which benefit from its superior properties in high-stress and high-temperature environments.
Why Choose E-Fab for Molybdenum Etching?
When you need precise, reliable molybdenum components, you need to know you’re partnering with a manufacturer with experience and expertise in working with this powerful transition metal.
As a leading provider of photochemical etching manufacturing services, E-Fab is an expert at etching and forming molybdenum to precise standards and specifications.
Our superior etching process enables us to deliver parts with complex or intricate geometries and tight tolerances with no heat-affected zones or burrs for customers in the telecommunications, defense, medical, and electronics industries.
Customization is key. We are focused on pushing your design to the next level by leveraging the latest cutting-edge technology and engineering principles. Our engineering philosophy and expertise revolve around innovation, so we aim to blend ingenuity and precision so that every project we deliver meets exacting standards and tight tolerances.
We take pride in our commitment to excellence and ensuring the highest quality standards throughout our manufacturing processes. To achieve this, we hold compliance certifications (ISO 9001:2015, ITAR, CMRT, and PCMI), highlighting our dedication to best practices and delivering top-notch products to our customers.
Shaping the Future of Molybdenum Manufacturing
The unique combination of molybdenum’s high melting point, exceptional strength, excellent thermal and electrical conductivity, and corrosion resistance continue to make it one of the most valuable materials for precision manufacturing.
With its ability to enhance the performance and durability of components across various industries, molybdenum is set to play a key role in manufacturing well into the future.
If you’re looking for a proven manufacturing partner to deliver high-quality molybdenum components you can rely on in even the harshest environments, the team at E-Fab can help.
Boasting a 40-plus-year reputation for accurate, reliable, and durable parts, our precision molybdenum components are powering leading-edge technology companies, defense contractors, and medical equipment manufacturers and innovators.
Our team of engineers, manufacturers, and quality assurance professionals is committed to quality, ensuring we every product is ready for use.