Tungsten is a refractory metal known for its exceptional properties, including the highest melting point of any metal (3422°C / 6191°F), superior strength, and high density. These characteristics also include thermal resistance and radiation protection due to its unique material properties, which are crucial for medical applications.
Professionals in the medical industry use several systems and tools for life-saving procedures and tests that incorporate tungsten-based components, which are vital to ensuring accurate and dependable information is provided to the medical teams in real-time.
Most people are familiar with an X-ray machine that takes images of a broken bone or a CT scan when a head injury is suspected. These are two places where tungsten parts and components are found. Tungsten is also used in robotic medical technology and brain surgical instruments when the line between success and failure is extremely thin.
Due to the difficulty of these procedures and the importance of precise devices and instruments, medical manufacturers and engineers must consider several challenges during the design and planning processes that rule out traditional methods of manufacturability.
Tungsten’s Role in Medical Devices
Tungsten components are used in X-ray machines, CT scanners, and radiation therapy equipment. These components protect the equipment, operators, and patients from the radiation produced during the procedure.
Tungsten can also be found in surgical instruments, implantable devices, and testing equipment that require exact tolerances and biocompatibility. Tungsten is used in miniature cables and tools, such as syringe protection equipment and arthroscopic surgical wands for controlled ablations.
Tungsten also withstands high temperatures and wear, making it ideal for prolonged use in demanding conditions. The material’s durability makes it a prime candidate for use in various therapy and treatment delivery machines.

Manufacturing Challenges for Tungsten in Medical Devices
The high melting point and density of tungsten are some of the benefits of using the metal in medical devices. At the same time, it is extremely hard and brittle, making traditional manufacturing methods like CNC milling or wire EDM more difficult and costly. While both methods can hold the tight tolerances required for the industry, each has limitations and is only as accurate as the tools and software in the machines.
For all its benefits, tungsten is often a more expensive option that is not readily available, so manufacturers must consider the material waste associated with subtractive manufacturing processes. In the spirit of advancing medical technology and getting life-saving tools into the hands of more medical professionals, it is crucial to keep the raw material costs of every component as low as possible.
Tungsten in medical components requires a different level of accuracy, often referred to as extreme precision, where traditional manufacturing refers to tolerance in the sense of thousandths, extreme precision looks at tolerance on a micron level. E-Fab understands the importance of this level of precision, as well as tungsten’s biocompatibility and the necessity of continually adhering to regulatory standards within the medical field.
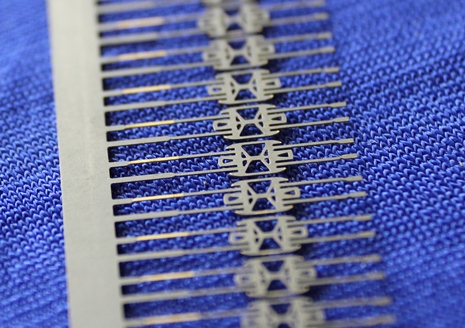
How Does E-Fab’s Photochemical Etching Solve These Challenges
Photochemical etching (PCE) is a subtractive form of manufacturing that enables extreme precision with little to no variance between components.
E-Fab’s advanced PCE techniques achieve tight tolerances and create intricate, complex two-dimensional shapes required for medical device components used in medical equipment and implants designed for specific anatomical structures.
Photochemical etching is a “stress-free” manufacturing process that creates parts and components without the cracking or deforming of the material from mechanical or thermal stress. Additionally, etched parts can be formed to create three-dimensional parts for other applications.
Fabricating parts with PCE, where the material’s integrity is kept intact, is crucial in medical applications as material micro-stresses can start small but ultimately compromise the part’s integrity.
PCE also allows for minimal material waste and streamlines prototypes and large-scale manufacturing production. The reduction in waste and efficiency in production both contribute to efforts to keep these devices affordable and make them more readily available to patients.
Patient safety is the top priority at every step of the process, from fabrication to implementation. Producing parts and components using PCE from medical-grade tungsten ensures that functionality does not compromise safety, thereby removing a barrier to approval for use.
Benefits to Patient Outcomes
Every medical professional is dedicated to providing the best care possible for their patients. Yet, some patients are apprehensive about accepting treatments that are deemed experimental or risky.
When medical devices, machines, and treatments are proven reliable, there is a pattern of repeatable success and patients are more apt to accept a treatment plan.
As engineers and manufacturers of medical devices perfect the tools used by medical professionals, confidence rises, and patients’ health outcomes improve. E-Fab partners with engineers and manufacturers to develop and deliver parts and components to minimize risk and maximize benefits.
For example, E-Fab photochemically etches enhanced shields that protect patients and clinicians from the harmful radiation emitted during cancer treatments. As we all continue to create more effective medical devices and safer equipment, patient quality of life increases.

E-Fab’s Expertise in the Medical Industry
Boasting more than 40 years of experience, the team at E-Fab specializes in delivering precision metal components tailored to the unique needs of our medical clients.
Blending experience, expertise, and experimentation, our team of engineers, manufacturers, and quality assurance specialists produce a wide variety of precision metal products that are durable, reliable, and accurate. As an ISO 9001-certified facility, among other quality certifications, we ensure all our components adhere to stringent quality control and compliance standards for medical devices.
Our proven ability to provide customized, high-precision components tailored to the industry’s unique requirements sets us apart. Our precise metal components designed specifically for medical applications include, but are not limited to:
- Medical sensor elements
- Customized medical device parts
- High-precision screens and filters for sterile medical environments
- Intricate shielding components for medical equipment
- Metal components for surgical devices
- Precision components for medical sensors
- Miniaturized parts for medical device technology
- Medical instrumentation components

Ready to Improve Patient Outcomes for Years to Come
The synergy between tungsten’s remarkable properties and precision manufacturing PCE techniques used by E-Fab makes these medical devices capable of achieving unparalleled performance and reliability.
At E-Fab, we are leaders in photochemical etching, prototyping, and producing intricate parts critical for medical applications. We’re the trusted team for an industry that demands meticulous attention to detail throughout the manufacturing process.
Working with innovation and collaboration at our core, we ensure the highest precision, reliability, and safety standards for every medical component we deliver.