Rapid prototyping is revolutionizing metal manufacturing by accelerating product development and reducing costs. Leveraging advanced technologies and continuous R&D, this approach offers benefits like design validation, time savings, and customized solutions across various industries.
The precision metal manufacturing industry continues to develop, with new, innovative processes like metal prototyping taking center stage.
Enhanced by cutting-edge technologies like CNC machining, laser cutting, and direct metal laser sintering, sheet metal prototypes have reshaped the way manufacturers and engineers bring their concepts to life.
From cost-efficiency and rapid development to the ability to test and refine designs with unparalleled precision, these cutting-edge components deliver a wide range of advantages to manufacturers, engineers and the end-user.
With a culture built on client collaboration, E-Fab leads the way in rapid prototyping techniques and technologies, working hand-in-hand with customers in highly innovative, technically demanding, and critical industries. Metal prototyping pioneers, we have consistently delivered cutting-edge sheet metal solutions for a diverse range of applications. With specialist metal prototyping tools and equipment, together with our specialist in-house engineering team, we’re continuing to drive innovation, efficiency, and quality in precision manufacturing for a variety of metal materials.
In this article, we explore common rapid prototyping processes, the advantages of precision prototype metal parts, and the key role precision metal prototyping is playing in shaping the future of manufacturing.
What is precision metal prototyping?
Precision metal prototyping uses advanced technologies and methodologies, such as CNC machining, laser cutting, and metal casting to rapidly transform design concepts into tangible prototypes.
These metal prototypes allow engineers and manufacturers to assess the feasibility, form, and functionality of their sheet metal components. Rapid prototyping minimizes errors, speeds up development, and allows precise iteration, reducing the time-to-market and facilitating better product quality – perfect for a range of industries, especially those with short product life cycles and intense competition.
Common rapid prototyping processes
In order to efficiently create metal prototypes for a variety of applications, a number of different rapid prototyping processes are used. These processes offer a range of advantages in terms of speed, precision, and cost-effectiveness.
Some of the common rapid prototyping processes used include:
CNC Machining:
Computer Numerical Control (CNC) machining is a versatile and highly precise method for creating metal prototypes. In this process, material is removed from a metal workpiece using computer-controlled machinery to create the desired component. The accuracy of CNC machining makes it suitable for a wide range of metals.
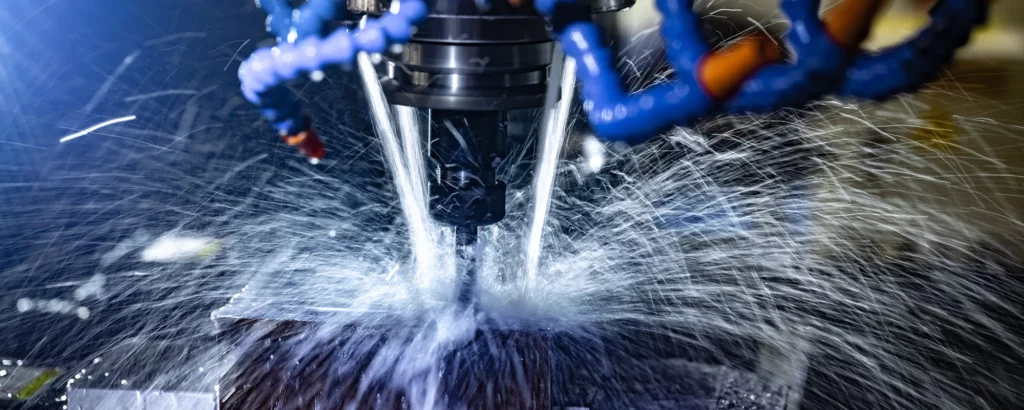
3D Printing:
Additive manufacturing, commonly referred to as 3D printing, has gained popularity for its ability to create intricate metal prototypes layer by layer. This method is particularly useful for complex geometries and quick iterations.
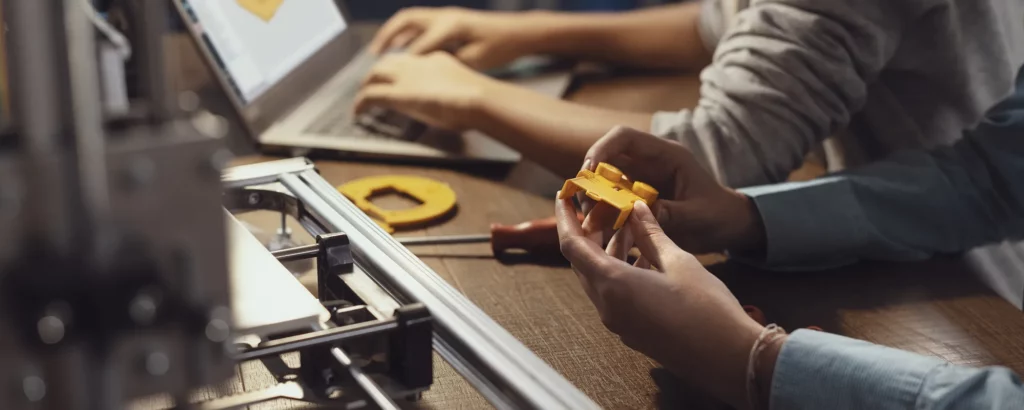
Sheet Metal Prototyping:
Sheet metal prototyping involves cutting, bending, and assembling sheet metal to create prototypes of components with a two-dimensional or three-dimensional shape. This process is commonly used for components like enclosures, brackets, and other sheet metal parts.
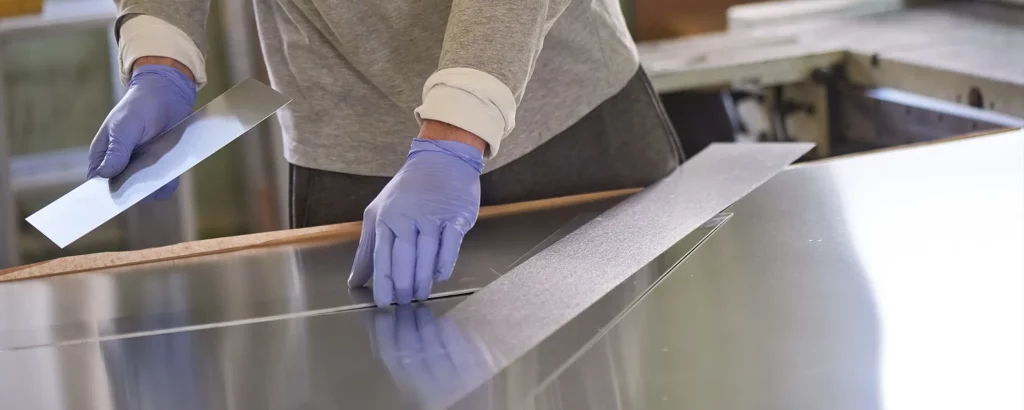
Laser Cutting:
Laser cutting is a precise method for creating intricate shapes in sheet metal. High-powered lasers are used to cut through the metal, allowing for the creation of detailed metal prototypes with clean edges and minimal heat-affected zones.
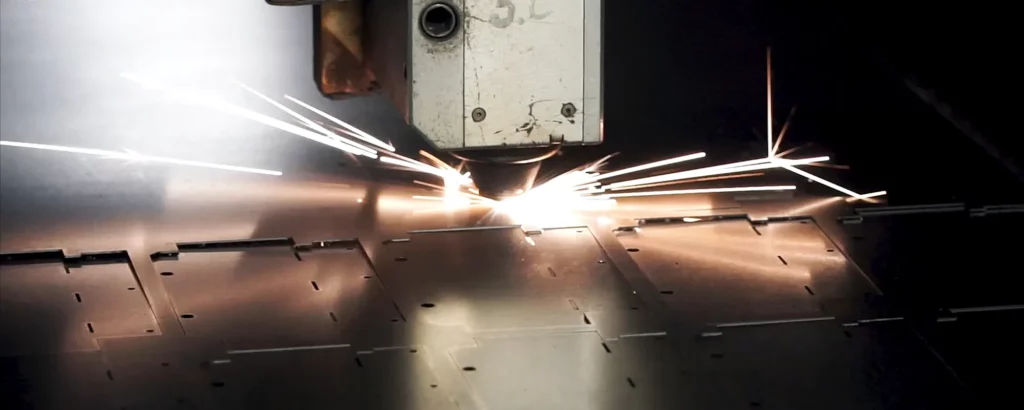
Photochemical Etching:
Photochemical etching, also known as chemical milling, is a subtractive manufacturing process that utilizes chemicals to selectively remove material from a metal sheet. It’s particularly suitable for creating precision components with fine details.
Learn more about the precise rapid prototyping processes used by E-Fab to validate and test designs before committing to large-scale production.

The advantages of precise metal prototypes
Metal prototype fabrication is a crucial step in the manufacturing process, enabling engineers and manufacturers to quickly and comprehensively evaluate the feasibility and design of intricate sheet metal components.
With a sheet metal prototype, the overall development process is heavily expedited, significantly reducing lead times. It also ensures that the final sheet metal prototypes are finely optimized for exceptional performance by detecting early design flaws and rectifications. The precise process also serves as a precursor to precise metal casting techniques, which produce components with remarkable accuracy and structural integrity.
1. Cost Efficiency in Product Development
One of the primary advantages of precision sheet metal parts is their potential to significantly reduce costs in product development. Traditional manufacturing methods involve expensive tooling and molds that can become a financial burden, particularly in the early design stages. Precision prototyping, on the other hand, bypasses these costly setups, allowing engineers and manufacturers to rapidly create a metal prototype without the heavy initial investment.
2. Accelerated Product Development Cycles
In a world where time-to-market can make or break a product’s success, precision prototype metal parts become a crucial asset. Rapid prototyping technologies, such as CNC machining, allow for the fast creation of metal prototypes, reducing lead times from months to weeks or even days. This accelerated development cycle enables businesses to remain agile and responsive to ever-changing market demands.
3. Precision and Quality Assurance
The precision in precision prototype metal parts isn’t just a name; it’s a defining characteristic. These prototypes are crafted with a level of accuracy that traditional manufacturing methods often struggle to achieve. With CNC machining, for example, tolerances can reach minuscule levels, ensuring that each component precisely matches design specifications. This level of precision translates to enhanced quality assurance, reducing defects and enhancing overall product reliability.
At E-Fab, we partner with customers to test concepts, materials, and processes with fast prototyping. That process allows parts to undergo testing, analyzing, and proofing before heading into mass production.
4. Design Optimization and Iteration
One of the most compelling advantages of precision prototype metal parts is the freedom they offer for design optimization and iteration. Engineers and designers can rapidly create and test component variations, assessing factors like size, shape, and material. This iterative process facilitates the identification and elimination of design flaws early in the development cycle, ultimately leading to a superior end product.
5. Compatibility with a Wide Range of Materials
Precision prototype metal parts are not limited to a single type of material. They can be crafted from a wide variety of metals, each selected for its specific properties. From lightweight aluminum to robust stainless steel, these prototypes offer the flexibility to choose the material that best suits the intended application.
6. Reduced Material Waste
Traditional manufacturing methods often result in significant material waste during the setup and adjustment phases. Precision prototype metal parts, with their minimal setup requirements and high precision, significantly reduce material waste. This not only benefits the environment but also contributes to cost savings.
7. Complex Geometries and Intricate Details
The capabilities of precision prototype metal parts extend beyond the production of simple shapes. Engineers and designers can create complex geometries and intricate details that would be challenging or impossible to achieve with traditional manufacturing. This allows for innovative designs that can open new possibilities in various industries.
8. Customization and Tailored Solutions
Precision prototype metal parts are all about customization. Rapid prototyping enables manufacturers to create customized or personalized products. With the ability to rapidly produce individualized prototypes, manufacturers can respond to specific customer requirements and preferences. This capability is particularly valuable in industries like medical devices, automotive, and consumer electronics, where tailored products are in demand.
9. Bridge to Full-Scale Production
Precision prototype metal parts serve as a crucial bridge between the design and full-scale production phases. Once a prototype is thoroughly tested and refined, it can be seamlessly transitioned into mass production, saving time and minimizing disruptions in the production cycle.
10. Market Agility and Competitive Advantage
In today’s dynamic business environment, agility is key to staying competitive. Precision prototype metal parts empower businesses to react swiftly to market changes, adapt to customer feedback, and launch new products with confidence. The ability to iterate and refine designs quickly provides a significant edge in highly competitive markets.
E-Fab's Expertise in Rapid Prototyping
As pioneers in the field of rapid prototyping, E-Fab’s culture is based on innovation and problem-solving. At the core of our approach is a commitment to experimentation, iteration, and a culture of learning from failures. Within our organization, rapid prototyping is not merely a process but an integral part of our development journey.
We place a strong emphasis on ongoing improvement, constantly investing in training and resources to educate our team members on the latest rapid prototyping techniques and technologies. This empowers our workforce to hone their skills and embrace this dynamic field. We also provide our employees with access to cutting-edge tools and equipment, including computer-aided design (CAD) software, laser cutters, and other state-of-the-art prototyping technologies. This collaborative approach fosters the creation of cross-functional teams and encourages innovation across the board.
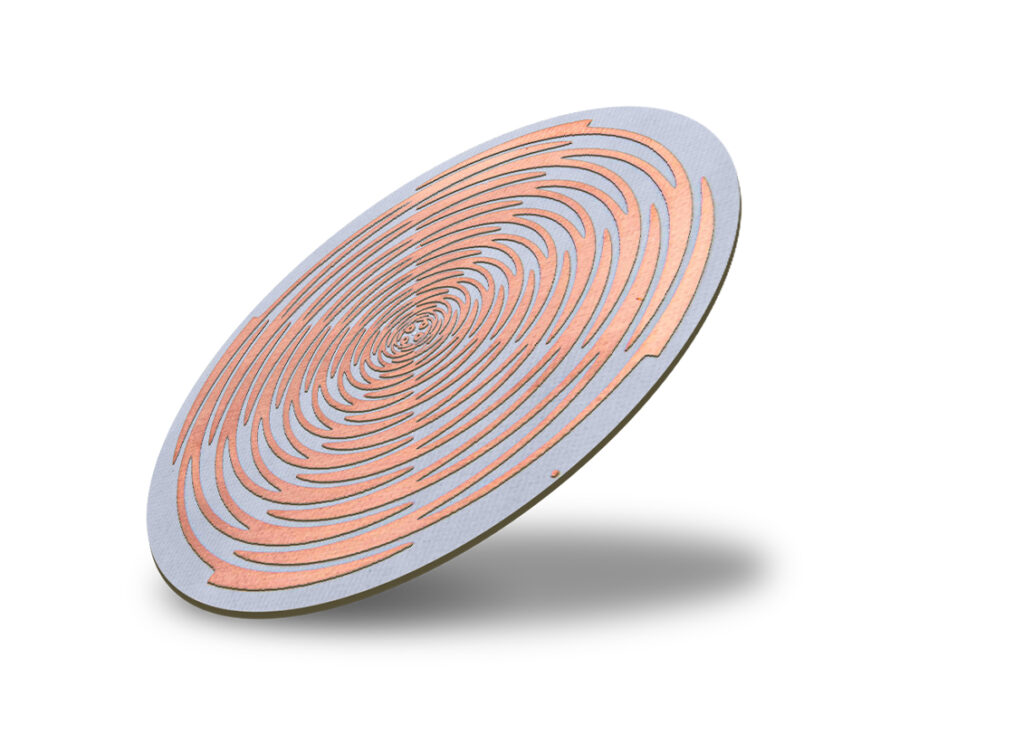
How Metal Prototyping in Shaping The Future of Precision Manufacturing
Precision prototype metal parts are driving the evolution of precision metal manufacturing. With their ability to cut costs, reduce lead times, and improve design and quality assurance, they have opened doors to innovative solutions and competitive advantages for a wide range of industries.
As technology continues to evolve, precision prototyping methods will only become more advanced and accessible, further expanding their role in shaping the future of precision metal manufacturing.
When it comes to metal prototyping, no one does it better or faster than the trusted team at E-Fab.
Working across a range of leading industries, we partner with customers to test concepts, materials, and processes with fast prototyping. That process allows parts to undergo testing, analysis, and proofing before mass production.
If you’ve got a prototyping problem, let’s solve it!