In this article, we explore the role precision plays in engineering and how it’s shaping the landscape of modern manufacturing.
In the innovation and performance-driven world of engineering, the ability to achieve exacting levels of accuracy in manufacturing processes is not just a goal; it’s a fundamental requirement.
Every step, from design to production, demands meticulous attention to detail to craft components with incredible accuracy, reliability, and repeatability. Precision is the linchpin that holds it all together, ensuring that every cut, etch, or forming operation results in components that meet stringent tolerances. This level of accuracy is especially crucial in industries like aerospace, electronics, and medical devices, where the performance and reliability of components hinge on their precise dimensions.
At E-FAB, precision isn’t just a buzzword; it’s a commitment that permeates every facet of our operations. Leaders in successful precision machining, our photo etching expertise has seen us consistently deliver precise parts in the highest tolerances for applications that demand accuracy. From the initial processes design phase to the final product, we meticulously engineer our processes to achieve the highest levels of accuracy and quality.
In this article, we explore the crucial role precision plays in engineering and how it’s shaping the landscape of modern manufacturing. With a focus on popular techniques like photochemical etching, we break down the advantages of precision manufacturing processes when producing precision parts designed and delivered to exact specifications.
The Essence of Precision in Engineering
Precision is the foundation for innovation, reliability, and excellence in engineering. When we look at the role precision plays in metal manufacturing, its importance lies in its ability to ensure exacting accuracy and consistency throughout the entire production process.
The impact of precision is both profound and far-reaching for many industries, affecting everything from product quality and performance to compliance and customer satisfaction. Without precision, you risk your components’ performance, reliability, accuracy, and, most importantly, safety.
As technology continues to advance, so do the levels of precision available to manufacturers. Through the use of computer-aided manufacturing, components can be manufactured with precision and exhibit uniformity and reliability, ensuring that each piece meets the intended specifications. Precision engineering can also improve performance by enhancing both the efficiency and durability of products. This precision is especially critical in safety-critical industries such as aerospace and medical devices, where the reliability of components can directly impact end-users safety. Let’s dive a little deeper.
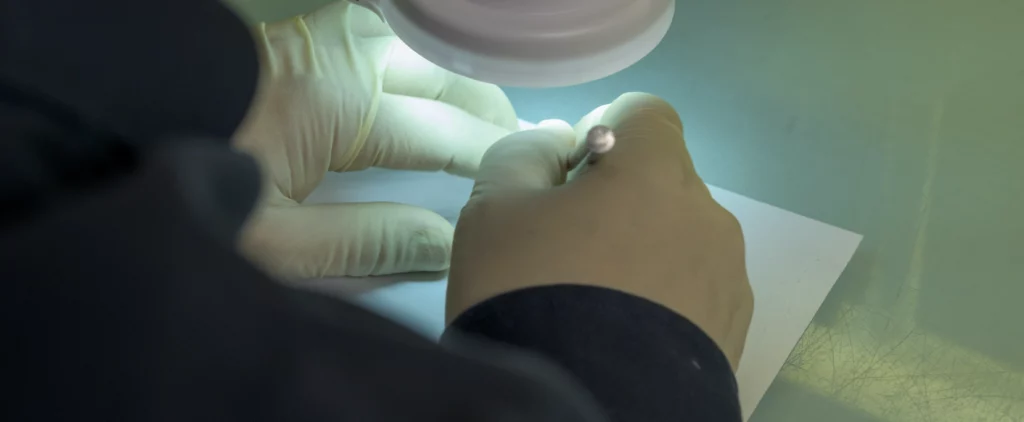
Why Precision is Paramount in Engineering
Precision in engineering is not just a technical specification but a commitment to excellence, fostering product quality, high performance, and, above all, safety. Relied on for every stage of the manufacturing process, precision can impact:
Product Performance: Precision ensures that engineered products function as intended, meeting performance specifications consistently. Precision plays a crucial role in ensuring safety and reliability in industries such as aerospace and automotive, where even minor deviations from design tolerances can cause catastrophic failures.
Quality Assurance: Precision is a cornerstone of quality assurance. It reduces defects, minimizes rework, and enhances the overall product quality. Engineers strive for precision to avoid costly recalls and repairs, which can have far-reaching financial and reputational consequences.
Cost Efficiency: Precision engineering often reduces material wastage and lower production costs. When components are manufactured with high accuracy, there’s less need for post-production adjustments or material scrap, resulting in cost savings.
Functionality: Many engineering applications rely on the seamless interaction of multiple components. Precision ensures that parts fit together precisely, facilitating the assembly process and ensuring proper functionality.
Durability and Longevity: Precise engineering contributes to the durability and longevity of products. Components manufactured with precision are less prone to wear and tear, corrosion, and premature failure, ultimately extending the lifespan of the final product.
Innovation and Advancements: Precision engineering often paves the way for innovation. It enables the development of smaller, lighter, and more efficient products, spurring technological advancements in various sectors.
Regulatory Compliance: In regulated industries like healthcare and aerospace, adherence to stringent precision standards is mandatory to meet regulatory requirements. Precision engineering ensures that products comply with safety and performance regulations.
Customer Satisfaction: Precision engineering translates to consistency and reliability in products. Satisfied customers trust brands that consistently deliver high-precision solutions, fostering brand loyalty and repeat business.
Competitive Advantage: Companies that prioritize precision can gain a competitive edge. They can offer products with superior performance, reliability, and quality, making them preferred choices in the market.
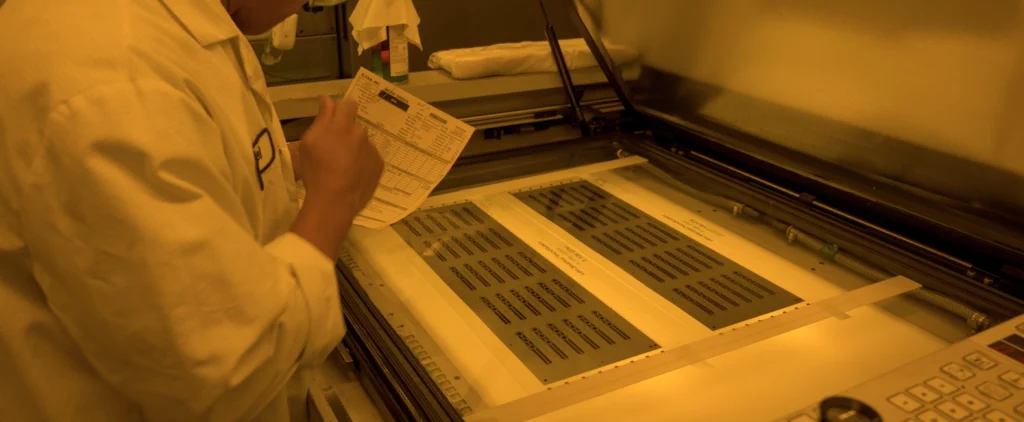
Engineered Precision Machining: Achieving Precision in Manufacturing
To achieve precision in metal manufacturing, a seamless blend of cutting-edge technologies, advanced machinery, and rigorous quality control measures are required. The process begins with precise design and planning, utilizing computer-aided design (CAD) and simulation tools to ensure accuracy.
High-precision machining techniques, such as photochemical etching, CNC machining, and laser cutting, play a pivotal role in shaping components with exacting tolerances. Photochemical etching has become the most popular process in precision metal manufacturing, offering unparalleled advantages in crafting intricate components with meticulous accuracy.
This technique involves using photosensitive materials and detailed photomasks to selectively remove material from a metal sheet, creating finely defined patterns. Boasting a wide range of advantages, photochemical etching allows for the production of intricate and complex designs with minimal tool wear, ensuring repeatability and consistency. The precision CNC machining process is highly scalable, seamlessly accommodating both prototyping and large-scale production.
Tight process controls, including temperature regulation, tool calibration, and material selection, further contribute to achieving precision. Continuous monitoring and feedback loops during production help identify and rectify deviations promptly. Quality assurance practices, such as thorough inspections and testing, serve as the final checkpoints to guarantee that each component meets the desired specifications.
Precision Engineering in the Real World
Various industries rely on precision engineering for accuracy, reliability, and intricate design. From the microscopic to the macroscopic, precision engineering is critical to crafting products that meet exacting standards across a broad spectrum of industries.
In aerospace, precision is paramount for crafting components like turbine blades and intricate sensor systems. The electronics sector relies heavily on precision engineering for manufacturing microchips and intricate circuitry. For medical devices, such as surgical instruments and implants, precision is paramount for seamless integration within the human body. The automotive industry relies on precision for efficient, reliable components for everything from engines to safety systems.
Even in everyday items like smartphones, precision engineering ensures the seamless functionality of delicate components.
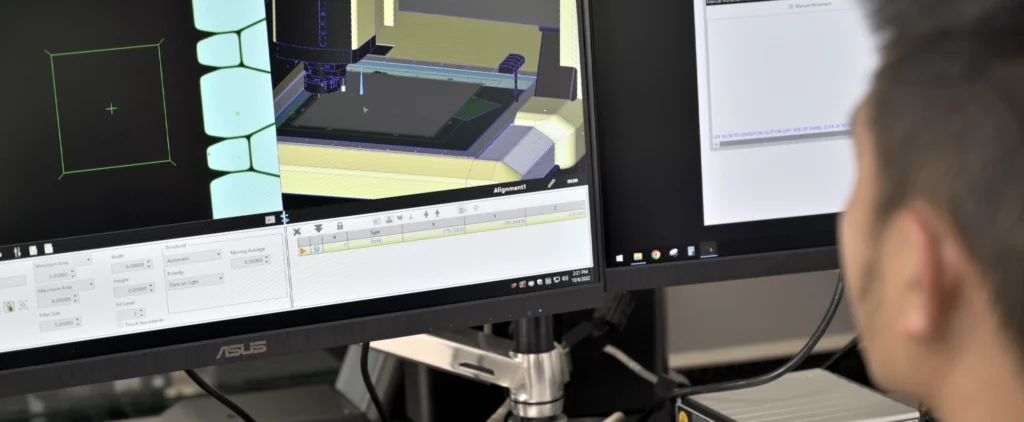
The Role of Advanced Technology in Precision Manufacturing
Technology is reshaping how precise parts are designed and delivered, making it faster and cheaper while improving accuracy, consistency, and performance.
Technology advancements, including the integration of computer-aided design (CAD), simulation tools, and cutting-edge machining techniques such as CNC lathes, have revolutionized precision metal manufacturing across various industries. This technological evolution has significantly enhanced the precision achievable in manufacturing processes. With their automated precision, CNC lathes enable the creation of intricate designs with tight tolerances, ensuring unparalleled accuracy.
Simultaneously, technologies like photo etching have emerged as sophisticated methods, allowing for the production of intricately detailed components with minimal tool wear. The intersection of these technological advancements has increased manufacturing efficiency and expanded the horizons of what is possible in precision engineering, setting new standards for accuracy and complexity in the modern era.
E-Fab is where ingenuity meets precision, leveraging the latest cutting-edge technology to consistently deliver parts with complex or intricate geometries and tight tolerances for customers in the telecommunications, defense, medical, and electronics industries.
Experts in Precision Machining
In the modern manufacturing world, where intricacy and accuracy define the quality of products, the power of precision engineering cannot be overstated. For a wide range of leading industries, where accuracy and reliability are everything, precision engineering meets stringent standards and sets new benchmarks.
Here at E-Fab, we’re pushing the boundaries of what is possible. Our engineers, manufacturers, and quality assurance specialists turn ideas into precision parts through collaboration, engineering, and expert machining processes. Specialists in photochemical etching, we consistently deliver accurate parts with tight tolerances in various materials for the telecommunications, defense, medical, and electronics industries.