There are numerous metal cutting technologies used to fabricate metal parts with high efficiency and extreme repeatability; selecting the right manufacturing process is crucial for achieving optimal results. Between the advanced techniques of Photochemical Etching (PCE) and traditional methods of Metal Stamping, there are specific areas that provide clear differences in the components produced. While both offer distinct advantages depending on the application, material, and desired output, PCE stands out as the superior choice for manufacturers requiring high precision, design flexibility, and burr-free components.
At E-Fab, we specialize in photochemical etching, a cutting-edge metal processing technology for thin materials that not only meets but exceeds the demands of industries that require tight tolerances, intricate geometries, and high-performance materials. Unlike traditional metal stamping, which relies on costly tooling and can introduce mechanical stress, distortion, and unwanted burrs, E-Fab’s etching process provides a non-contact, burr-free solution that ensures superior edge quality and structural integrity.
In this series, we will explore the fundamental differences between photochemical etching and metal stamping, evaluating their strengths and limitations, ideal applications, and the ultimate value gained by transitioning to a modern, precision-driven fabrication method. Through this exploration, it will become evident why E-Fab’s photochemical etching process is the clear choice for manufacturers looking to push the boundaries of conventional processing technologies.
Understanding Photochemical Etching (PCE)
Photochemical Etching is a subtractive manufacturing process that uses a combination of light-sensitive photoresist and chemical etchants to produce precise metal parts. The process involves applying a patterned photoresist layer to the metal, exposing it to UV light, developing the pattern, and then etching away the unwanted material.
One of the defining advantages of photochemical etching is its ability to accommodate complex and highly detailed designs without the limitations of traditional mechanical processes. Because there is no physical tool wear or die degradation, every part produced is identical, ensuring unparalleled repeatability. This makes PCE the clear choice over traditional metal-cutting technologies for industries such as aerospace, medical devices, electronics, and telecommunications, where consistency and extremely exacting tolerances are non-negotiable.
Additionally, E-Fab’s photochemical etching process offers unmatched flexibility in material selection and customization. Whether working with stainless steel, copper, titanium, or other specialty metals, our process enables rapid prototyping, and cost-effective production runs without the need for expensive retooling. The ability to make quick design modifications with minimal lead time gives engineers and product developers the agility needed to innovate and refine their designs efficiently.
Understanding Metal Stamping
One of the more traditional machining methods, metal stamping is a high-speed, high-volume production process used to shape sheet metal into uniform components by pressing or stamping it between a custom-designed die and punch. This technique employs mechanical or hydraulic presses to apply significant force, cutting, bending, or deforming the sheet metal into the desired shape.
The process is widely utilized in industries that require mass production of metal parts, as it offers cost-effective and efficient manufacturing after the initial high tooling costs are amortized into the production. While metal stamping is best suited for simple to moderately complex components, advancements in die technology can allow for the production of more intricate shapes with additional secondary operations.

Benefits of PCE vs. Stamping
Precision & Tolerance
Photochemical Etching (PCE):
Photochemical etching achieves exceptionally tight tolerances, often within ±0.001 inches (±25 microns), making it a highly precise manufacturing method. Because the process does not involve mechanical force, it eliminates stress, burrs, and material distortion, ensuring smooth, accurate components that are ideal for high-precision applications in industries such as aerospace, medical, and electronics.
Metal Stamping:
The precision of metal stamping is influenced by die wear and the mechanical force applied during the process, typically achieving tolerances of around ±0.005 inches. However, the high-pressure stamping action can introduce stress, warping, and burrs in the material, often necessitating additional secondary finishing processes like deburring or flattening to ensure a smooth and accurate final product.
Design Complexity & Flexibility
PCE:
Enables the creation of intricate and highly detailed designs with fine features, including sharp corners, micro-holes, and complex geometries that would be difficult to achieve with traditional manufacturing methods. Since the process does not require physical tooling adjustments, design modifications can be made quickly and cost-effectively, providing greater flexibility for prototyping and production. Additionally, parts can have different designs on either side of the part – front and back.
Metal Stamping:
Limited to simpler designs due to the mechanical constraints of the die, restricting the level of detail and intricacy that can be achieved. Producing complex shapes often requires expensive progressive dies and additional secondary operations, increasing both costs and production time while reducing design flexibility.
Cost & Tooling Investment
PCE:
Relatively low tooling costs by using digital photomasks instead of expensive metal dies, making it a more affordable option for precision manufacturing. It is cost-effective for both prototyping and high-volume production, allowing for efficient scaling without significant upfront investment. Additionally, the ease of creating and modifying photomasks enables faster turnaround times, providing greater flexibility for design changes and reducing overall lead times.
Metal Stamping:
Stamping requires substantial investment into tooling, often reaching tens of thousands of dollars for custom dies. However, it is best suited for high-volume production, where the per-unit cost decreases over time, offsetting the initial expense. Design changes can be challenging, as modifying or replacing dies is both costly and time-consuming, limiting flexibility in product development.
Material Compatibility
PCE:
Compatible with a wide range of metals, including stainless steel, titanium, copper, and exotic alloys, making it a versatile choice for various applications. Because the process does not involve mechanical force or extreme heat, it preserves the original properties of the material without causing hardening or softening, ensuring consistent performance and structural integrity.
Metal Stamping:
Limited by material hardness, as some brittle or delicate metals may crack under the high pressure of the stamping process. To overcome these challenges, additional treatments such as annealing or coating are often required to modify the material’s properties, adding complexity and cost to the process.
Lead Time & Production Speed
PCE:
Offers a quick setup and production process, allowing for prototyping in just a few days. It is ideal for low-to-medium-volume production, providing the flexibility to accommodate design changes efficiently while also offering scalable capacity for high-volume runs when needed.
Metal Stamping:
Involves long lead times due to the extensive process of die design, manufacturing, and testing, which can delay initial production. However, once the dies are set up, the process becomes extremely fast and efficient, making it ideal for high-volume production runs with consistent output.
Post-Processing Optimization
PCE:
Production layouts and processes can be optimized to increase overall manufacturing efficiency. For example, parts can be etched in panel form with half etched tabs. The parts can then be plated in sheets, reducing the need for additional wiring or racking of each individual part prior to plating. This decreases lead time and cost.
Environmental Impact & Waste Reduction
PCE:
Minimizes material waste by selectively removing only the necessary sections of metal, ensuring efficient use of materials. The process is conducted in environmentally controlled conditions, utilizing recyclable etchants that reduce chemical waste and promote sustainability.
Metal Stamping:
Produces significant scrap metal from cutting and trimming, leading to material waste and increased production costs. Additionally, the dies used in the process wear over time, requiring frequent replacement and consuming additional materials, further impacting efficiency and sustainability.
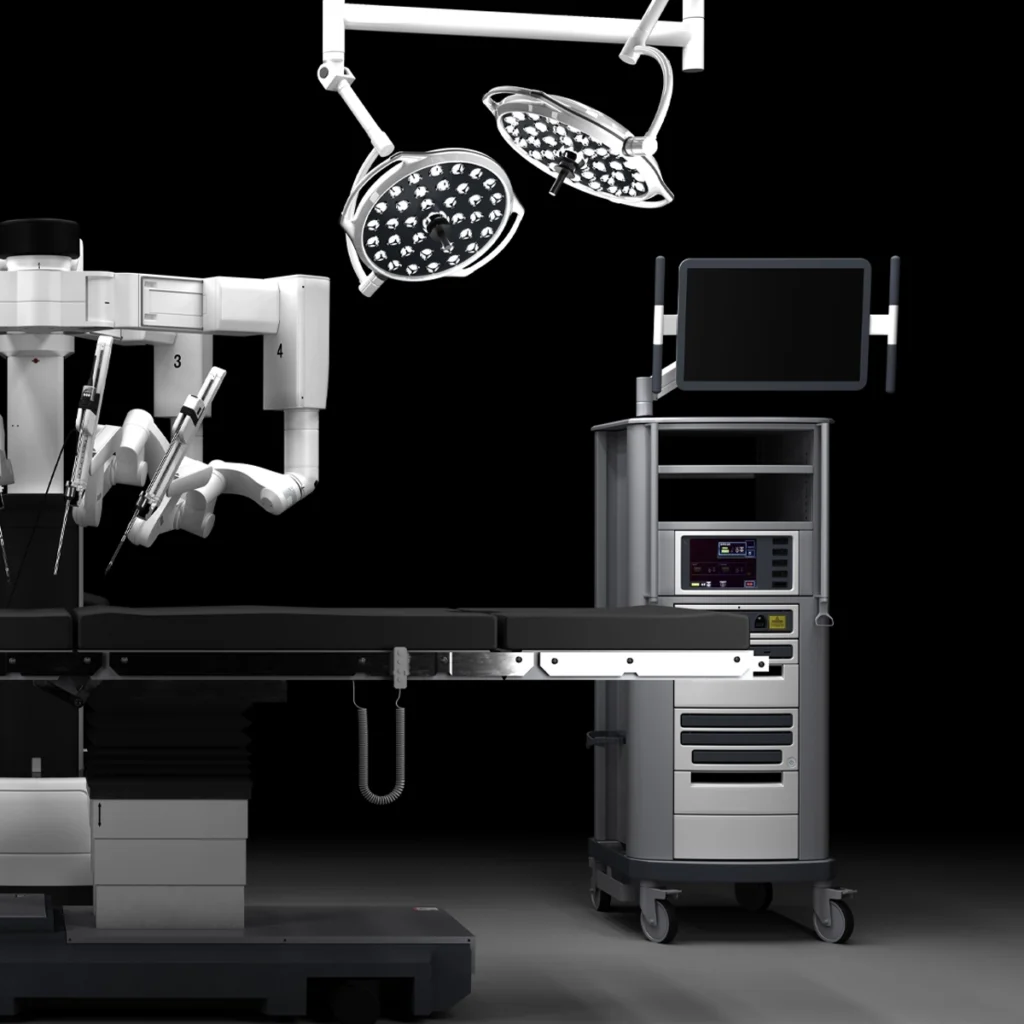
Ideal Applications for PCE vs. Metal Stamping
The PCE process is especially valuable for rapid prototyping, low-to-medium production volumes, and applications that produce intricate metal parts, with burr-free geometries that cannot be easily achieved through mechanical manufacturing methods. Because PCE does not involve high-pressure stamping or cutting forces, it preserves the material’s original properties, ensuring there is no mechanical stress, warping, or heat-affected zones that could compromise performance.
This makes it an ideal choice for industry sectors requiring extreme precision and fine detailing, such as aerospace, medical, electronics, and telecommunications, where micro-features, sharp edges, and complex patterns are essential. Additionally, because PCE uses photomasks instead of expensive metal dies, design modifications can be made quickly and cost-effectively, allowing manufacturers to iterate efficiently and reduce time-to-market for new products.
Although conventional stamping processes can excel in large-scale production runs, they lack the design flexibility that PCE offers. Creating complex geometries often requires an expensive investment in complex tooling, from multi-stage tooling to secondary finishing operations required to remove burrs and correct material distortion. Additionally, any design modifications require expensive die adjustments or complete retooling, making it less adaptable for fast-changing industries or small-batch production needs.
Aerospace
PCE: High-precision components are needed, such as fuel injector nozzles, shielding, TWT grids, , and fine filters.
Stamping: Large, high-volume parts like brackets, shielding, and structural reinforcements.
Medical Devices
PCE: Extreme precision is required for microsurgical blades, implantable devices, stents, and microfluidic components.
Stamping: Mass production of medical housings, brackets, or standardized equipment parts.
Electronics
PCE: High-precision, thin metal parts like EMI/RFI shielding, lead frames, connectors, busbars, heat sinks, and circuit board components.
Stamping: Standardized metal enclosures, heat sinks, and chassis components are mass-produced.
Automotive
PCE: Precision components like fuel injectors, battery grids, heat exchangers, and sensor elements
Stamping: Large-scale parts such as body panels, brackets, frames, and exhaust systems.
Let E-Fab Show How PCE is Shaping the Future with Precision
Both photochemical etching (PCE) and metal stamping offer distinct advantages tailored to produce precision metal components. PCE excels in high-precision, burr-free production with unmatched design flexibility, making it ideal for intricate components that require tight tolerances and stress-free manufacturing. In contrast, metal stamping is best suited for high-volume production of simple to moderately complex parts, where lower per-unit costs justify the high initial tooling investment. Selecting the right process depends on factors such as design complexity, material properties, production volume, and cost considerations. By understanding the strengths and limitations of each technique, engineers and manufacturers can make informed decisions to optimize efficiency and product quality.
For manufacturers prioritizing precision, flexibility, and cost-effective production, E-Fab’s photochemical etching process is the superior choice over metal stamping. With no costly tooling, rapid design adaptability, and the ability to produce highly intricate parts with extreme repeatability, PCE is the go-to solution for industries that demand excellence.
While metal stamping remains a viable option for mass production, photochemical etching is the clear winner for applications requiring high precision, burr-free edges, and material integrity without the limitations of mechanical stress and die constraints.
Contact us today with your latest project, we look forward to showing you the inherent advantages of PCE in comparison to the relatively limited technology of stamping.