E-Fab is dedicated to providing our clients with best-in-class services and sharing our accumulated knowledge of manufacturing excellence throughout every project we are involved with.
When it comes to precision metal fabrication, selecting the right manufacturing process is crucial for achieving optimal results. We incorporate the latest metal processing technology combined with traditional metal cutting technologies to create solutions that continue to meet and exceed our customer’s expectations.
Two of the most widely used techniques to produce precise metal parts are Photochemical Etching (PCE) and Laser Cutting. Both offer distinct advantages and limitations depending on the application, material, and desired output.
We pride ourselves on cultivating a team of experts who have years of hands-on experience within the industry. At E-Fab, we are committed not only to utilizing these cutting-edge processes and staff expertise but also to educating our clients on how to leverage them to achieve superior results in their projects.
Throughout this series, we will delve deeper into the benefits of Photochemical Etching vs. Laser Cutting. By examining aspects such as material compatibility, precision tolerances, production speed, and cost-effectiveness, our aim is to provide engineers, designers, and manufacturing professionals with the insights they need to make informed decisions.
Understanding Photochemical Etching (PCE)
Photochemical Etching (PCE), also known as chemical milling or photochemical machining (PCM), is a highly precise, cost-effective subtractive manufacturing process used to produce intricate metal components with fine details and tight tolerances. Unlike traditional machining methods that rely on mechanical cutting or thermal processes, PCE utilizes a combination of photoresist technology and chemical etchants to selectively remove material, allowing for the creation of complex patterns without inducing mechanical stress, distortion, or burr formation.
The five key steps begin with metal preparation, where the selected metal sheet is thoroughly cleaned to ensure proper adhesion of the photoresist. Next, a light-sensitive photoresist is evenly applied to both sides of the sheet, acting as a protective layer. During UV exposure and image development, a photomask is placed over the coated sheet and exposed to ultraviolet light, hardening specific areas of the photoresist and leaving the unexposed portions to be chemically removed in the next step. The chemical etching stage follows, where controlled etchants dissolve the exposed metal, leaving behind the desired pattern. Finally, the stripping & cleaning step removes the remaining photoresist and ensures a clean, corrosion-free component with high precision.
Understanding Laser Cutting (CO2 and Fiber)
Laser cutting employs a highly focused laser beam, controlled by computer systems, to precisely cut or engrave a variety of materials, including metals like steel, aluminum, and titanium. The beam works by melting, burning, or vaporizing the workpiece along a predetermined path while assisting gases remove molten material and minimize oxidation. Available in both CO2 and fiber optic systems, this process delivers repeatable accuracy, although it is limited in high-volume production due to a singular cutting unit, which often requires additional post-process finishing due to slag build-up from cutting.
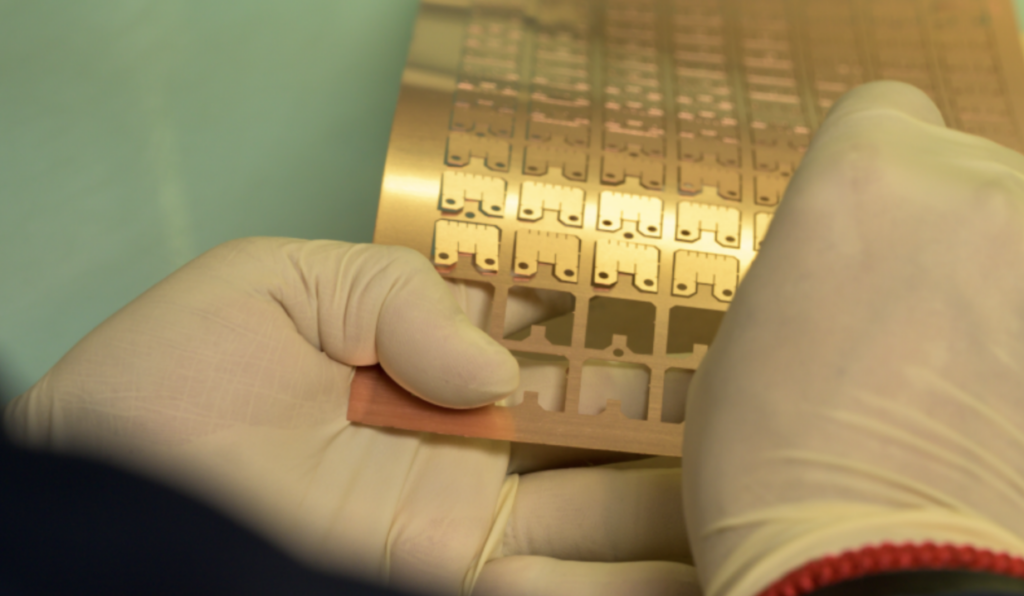
Benefits of the Photochemical Etching Process
Photochemical etching offers numerous advantages in precision metal fabrication, delivering high-resolution, intricate designs without the need for costly dies or mechanical tools. By utilizing a chemical etching process guided by precision photolithography, this technique enables the creation of highly detailed and complex geometries with exceptional accuracy and tight tolerances. Its non-contact nature eliminates mechanical stress and thermal distortion, ensuring stress-free and burr-free, dimensionally stable components even for ultra-thin or delicate materials.
Additionally, the method is highly versatile and capable of working with a broad range of metals and alloys, including stainless steel, copper, brass, and even exotic materials like titanium and tungsten. Photochemical etching is particularly advantageous for industries requiring fine-detail components, such as aerospace, medical devices, and electronics. It is also a highly cost-effective solution for low to medium-production runs, thanks to its minimal tooling costs, rapid prototyping capabilities, and excellent repeatability, making it ideal for both intricate designs and quick design modifications.
Precision and Accuracy
PCE allows for extremely fine details and intricate patterns without producing mechanical stress or burrs. This process also maintains tight tolerances with uniform material removal, while laser cutting may affect material integrity due to heat.
Also known as Heat Affected Zones (HAZ), the heat generated by the laser beam can alter material properties both visually and structurally, which typically requires additional post-processing for more high-precision parts. This is exponentially more apparent as the material thickness and density increase, which requires the cutting beam to move slower, resulting in more heat produced along the cut line, resulting in slag along the edges.
Material Compatibility
Both processes work with various metals; however, photochemical etching excels with thin metals and complex geometries. Laser cutting does manage to cut thicker materials, but that threshold is quickly met with thicknesses exceeding 1″ due to the loss of accuracy and the immense amount of thermal distortion.
The photochemical etching process does not exert force on the material, eliminating the risk of mechanical deformation. Because it does not alter the integrity of the material during the process, the end result maintains consistency throughout the production cycle. Depending on the density of features required when using laser cutting, the heat introduced to components throughout a single sheet or plate of material can result in unpredictable and inconsistent warping of the part. As the heat is uncontrollably dispersed throughout the part, once completely cut free, it loses the surrounding mechanical strength provided by the whole sheet and takes a form of its own.
Design Complexity
Photochemical etching is advantageous for intricate patterns and fine features, allowing for extremely fine details and intricate patterns. This process is extremely advantageous for complex designs in thinner materials, whereas laser cutting can result in uncontrolled material removal, due to the excess heat.
Laser cutting can be sufficient for standard shapes or hole patterns as long as there is a balance between the material, both type and thickness, and the design features.
Cost and Scalability
Photochemical etching is cost-effective for high-volume production with consistent quality, as well as being extremely versatile for prototyping and small batch production. Given its processing flexibility and relatively low tooling costs, it is easy to scale without the need to modify or alter the equipment and process.
Although the process of laser cutting offers large-scale automation, those systems come with an extremely high price tag, which results in higher service costs offered by the manufacturer. To offset these high equipment costs, production runs require high-volume and low-mix designs to remain cost-competitive within the market, which, more often than not leads to a lack of capacity for rapid prototyping.
Edge Quality and Material Stress
Photochemical etching offers exceptional edge quality and material integrity by producing burr-free, smooth, and precise components without mechanical wear or deformation. It eliminates the risk of mechanical stress, heat-affected zones, and tool-induced inconsistencies, ensuring uniform, high-precision results.
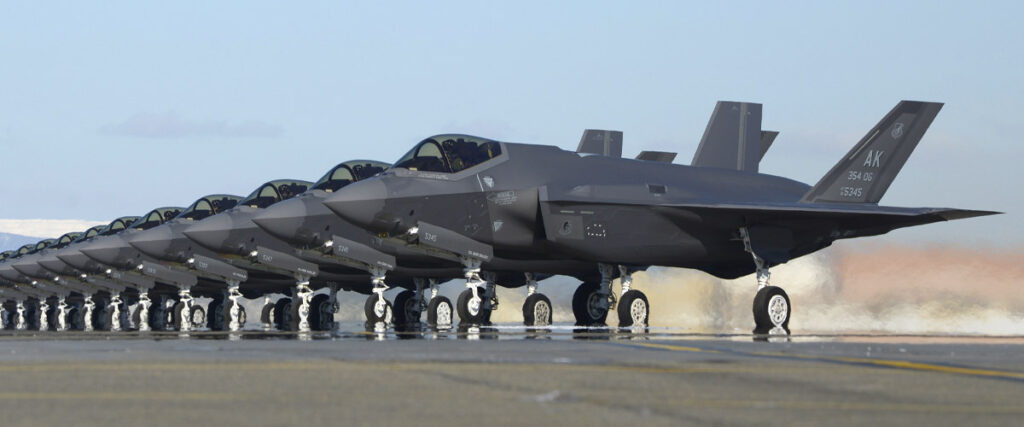
Ideal Industry Applications for PCE
Photochemical etching is ideally suited for industries that demand intricate, high-precision metal components with minimal thermal or mechanical stress. Its ability to create burr-free, dimensionally accurate parts from a variety of metals ensures both reliability and cost-effectiveness for both prototyping and large-scale production.
Aerospace
Lightweight, stress-free components with precise features. Suitable for thin precision parts, including fuel filters and heat exchanger plates
Medical Devices
Used for manufacturing precise surgical instruments and microfluidic components. Biocompatible parts with intricate designs and smooth finishes
Electronics and Power Sources
High-density, fine-feature components for circuitry and shielding. Ideal for intricate designs in electronic circuits in semiconductors, EMI/RFI shielding, fine mesh screens, and busbars
Automotive
Durable, high-precision parts for sensors and connectors, including fuel cells and injection nozzles. It can also be found in decorative, high-end automotive interiors
E-Fab’s Commitment to Quality
Photochemical etching (PCE) and laser cutting each offer distinct advantages suited to different manufacturing needs. PCE excels in producing high-precision, burr-free, and stress-free components, while laser cutting is valued for its speed and ability to process thicker materials.
E-Fab specializes in precision photochemical etching, offering highly accurate, burr-free, and cost-effective solutions for intricate metal components. With decades of experience, E-Fab delivers customized etching solutions that meet ultra-fine tolerances, often surpassing traditional fabrication methods in both quality and efficiency.
Contact us today with your latest project, we look forward to assisting you throughout the technical and manufacturing aspects of your design.