In the world of precision metal manufacturing, Photochemical Etching (PCE) and CNC Machining are two widely used techniques. While both methods offer unique advantages, PCE stands out as the superior choice for manufacturers requiring thin metal parts that are intricate, have high-precision, are cost-effective, and stress-free . However, CNC Machining retains its relevance for applications involving thicker materials and complex 3D geometries.
At E-Fab, we specialize in photochemical etching (PCE) as a precise and cost-effective solution for intricate, burr-free metal components. While PCE excels in producing highly detailed parts with minimal material stress, some applications may still require machining for thicker materials or complex 3D geometries.
Throughout this series, we will delve deeper into the benefits of Photochemical Etching vs. CNC Machining. By examining aspects such as material compatibility, precision tolerances, production speed, and cost-effectiveness, our aim is to provide engineers, designers, and manufacturing professionals with the insights they need to make informed decisions.
Understanding Photochemical Etching (PCE)
Photochemical Etching (PCE), also known as chemical milling or photochemical machining (PCM), is a highly precise, cost-effective subtractive manufacturing process used to produce intricate metal components with fine details and tight tolerances. Unlike traditional machining methods that rely on mechanical cutting or thermal processes, PCE utilizes a combination of photoresist technology and chemical etchants to selectively remove material, allowing for the creation of complex patterns without inducing mechanical stress, distortion, or burr formation.
Consisting of five key steps, it begins with metal preparation, where the selected metal sheet is thoroughly cleaned to ensure proper adhesion of the photoresist. Next, a light-sensitive photoresist is evenly applied to both sides of the sheet, acting as a protective layer. During UV exposure & image development, a photomask is placed over the coated sheet and exposed to ultraviolet light, hardening specific areas of the photoresist, leaving unexposed areas to be chemically removed in the subsequent step. The chemical etching stage follows, where controlled etchants dissolve the exposed metal, leaving behind the desired pattern. Finally, the stripping & cleaning step removes the remaining photoresist and ensures a clean, corrosion-free component with high precision.
Understanding CNC Machining
CNC (Computer Numerical Control) Machining is a highly precise and efficient subtractive manufacturing process that utilizes computerized controls and rotating cutting tools to shape a solid workpiece into a desired form. The process begins with a digital 3D CAD (Computer-Aided Design) model, which is converted into machine-readable instructions using CAM (Computer-Aided Manufacturing) software. These instructions guide the CNC machine in executing precise movements and material removal operations.
CNC machining is widely used across industries, including aerospace, automotive, medical, and electronics, due to its ability to produce highly accurate and repeatable components. It is suitable for a variety of materials, such as metals (aluminum, steel, titanium), plastics, composites, and even wood.
The primary types of CNC machining operations include:
- Milling – A rotating cutting tool removes material from a stationary workpiece, creating intricate shapes, holes, and slots.
- Turning (Lathe Machining) – The workpiece rotates while a cutting tool shapes it, typically used for cylindrical parts.
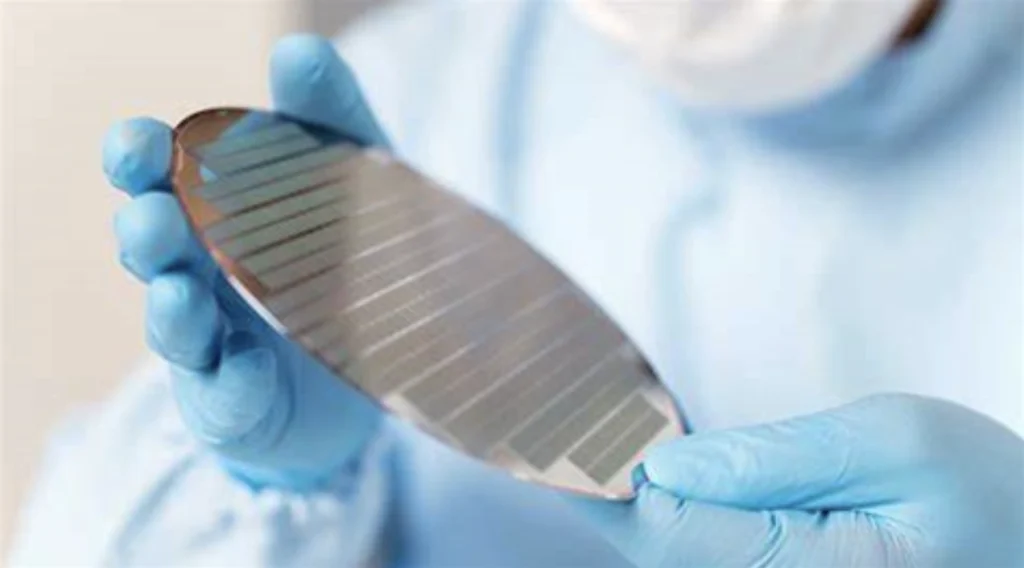
Benefits of Photochemical Etching vs. CNC Machining
Photochemical etching is a highly precise metal fabrication process that produces intricate, high-resolution designs without the need for expensive dies or mechanical tools. Using a chemical etching process guided by precision photolithography enables the creation of complex geometries with exceptional accuracy. Its non-contact nature prevents mechanical stress and thermal distortion, ensuring burr-free, dimensionally stable components, even for ultra-thin or delicate materials.
This versatile technique works with a wide range of metals and alloys, including stainless steel, copper, brass, titanium, and beryllium copper. It particularly benefits industries requiring fine-detail components, such as aerospace, medical devices, and electronics. With minimal tooling costs, rapid prototyping capabilities, and excellent repeatability, photochemical etching is a cost-effective solution for low to high-production runs, allowing for intricate designs and quick modifications.
CNC machining offers exceptional precision, versatility, and strength, making it ideal for manufacturing complex 3D components from a wide range of materials, including metals, plastics, and composites. It provides high accuracy and repeatability, enabling the production of tight-tolerance parts for industries like aerospace, automotive, and medical.
Unlike photochemical etching, CNC machining is suitable for thick materials and structural components. Additionally, it supports various machining operations—such as milling, turning, and drilling — allowing for complex geometries and functional features. While setup and tooling costs can be high, CNC machining remains an option.
Material Compatibility, Integrity & Stress Considerations
PCE: As a non-contact, chemical-based process, PCE does not exert mechanical force or introduce heat into the material. This results in components that are free from burrs, residual stresses, and heat-affected zones, preserving the original material properties. This makes photochemical etching ideal for processing thin metal without stressing or cracking the material.
CNC Machining: Since CNC machining involves direct contact with cutting tools, it can generate tooling marks, burrs, and residual stress within the material. Additionally, friction and heat generation may alter the metallurgical properties of heat-sensitive materials, requiring further finishing processes to remove imperfections. CNC machining is also not ideal for processing thin metal sheets, as it is not as efficient as PCE and is not ideal for working with brittle material like Tungsten, especially for small, thin parts.
Cost Efficiency & Scalability
PCE: This method is highly cost-effective for both prototyping and mass production, particularly for thin metal parts and sheet metal applications. The process has minimal tooling costs, making it well-suited for high-volume manufacturing without significant cost increases. Additionally, PCE etches all part features and parts in a sheet all at once – if 200 parts fit on a sheet of metal, all 200 parts on that sheet can be etched in a pass.
CNC Machining: While CNC machining is versatile, it becomes costly for high-volume production due to longer cycle times, frequent tool wear, and the need for skilled operators. Tooling expenses and material wastage also contribute to higher costs, making it less economical for large-batch manufacturing compared to PCE. Compared to PCE, CNC machining typically machines one part and one feature at a time, making the process less efficient for medium to large volume production.
Lead Time & Design Flexibility
PCE: This process enables rapid prototyping and quick design modifications with minimal cost implications. Because it relies on digital photolithography techniques rather than physical tooling, design iterations can be made easily without the need for extensive reprogramming or tool changes.
CNC Machining: CNC machining involves longer setup and programming times, which makes iterative design changes more expensive and time-consuming. Adjustments to the design may require new tooling, reprogramming, and additional machine calibration, limiting flexibility during the prototyping phase.
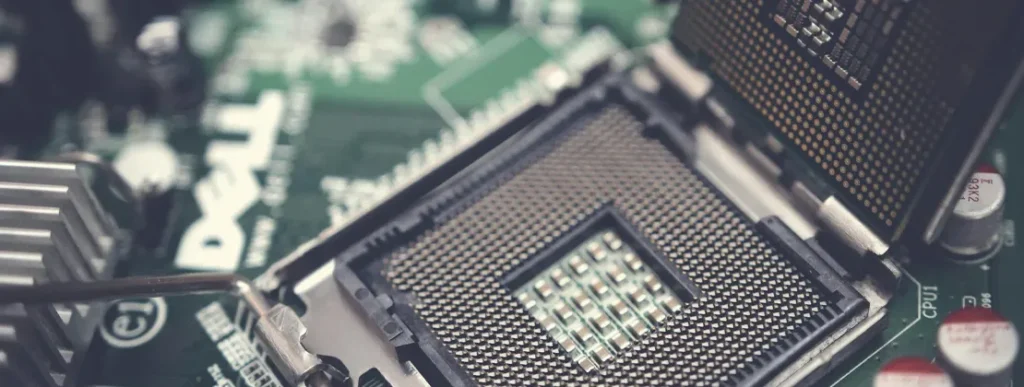
Ideal Industry Applications for PCE vs. CNC Machining
Photochemical etching and CNC machining are both widely used manufacturing processes for producing precision metal components, but they differ significantly in their capabilities, applications, and advantages.
Photochemical etching is ideally suited for industries that demand intricate, high-precision metal components with minimal thermal or mechanical stress. Unlike CNC machining, which involves cutting or milling material with physical tools, photochemical etching uses a controlled chemical process to dissolve unwanted material, preserving the structural integrity of the metal. This results in burr-free, dimensionally accurate parts without the risk of introducing mechanical stress or heat-affected zones.
Aerospace
PCE: Lightweight, stress-free components for satellites and aircraft such as RF/EMIshielding, shims, busbars and precision filters.
CNC Machining: Structural components requiring high mechanical strength.
Medical Devices
PCE: Biocompatible, burr-free parts for implants and surgical tools, such as titanium mesh, tungsten electrodes, or stainless steel surgical tips/blades.
CNC Machining: Custom orthopedic devices requiring bulk material removal.
Electronics
PCE: EMI/RFI shielding, flexible circuits, and fine-detail components like fine mesh screens.
CNC Machining: Connectors and enclosures requiring deep cuts.
E-Fab’s Commitment to the Best Approach
Both Photochemical Etching (PCE) and CNC machining offer unique advantages that cater to different manufacturing needs. While PCE excels in high-precision, burr-free, and stress-free applications, CNC machining is the preferred choice for producing thick, three-dimensional, and load-bearing components with precision. Choosing the right process depends on factors such as design complexity, material thickness, production volume, and cost considerations. By understanding the strengths and limitations of each technique, and the potential of combining those processes, engineers can make well-informed decisions to optimize their production processes and achieve superior results.
While CNC machining and photochemical etching each serve distinct purposes, PCE remains the preferred choice for applications requiring fine-detail precision, burr-free edges, and stress-free fabrication. When additional machining is needed for thick materials or structural components, manufacturers often integrate CNC machining into their workflows.
At E-Fab, we focus exclusively on photochemical etching to deliver highly precise and cost-effective metal components, helping customers achieve the best possible results for their designs.
Contact us today with your latest project, we look forward to assisting you throughout the technical and manufacturing aspects of your design.