Engineers call for titanium because of the material’s strength and versatility. In this article, we look at why engineers view titanium as a valuable metal, discuss the versatility of etched titanium, its unique advantages, and where you can find titanium etched parts across many industries.
With its exceptional strength-to-weight ratio, corrosion resistance, and biocompatibility, titanium has long been a popular material choice for industries ranging from aerospace to medical and beyond.
However, it’s not just the material’s inherent properties that make it so valuable but the techniques applied to manufacture precision titanium parts. Adding titanium etching to the manufacturing equation unlocks a whole new world of possibilities for applications across various sectors.
As a renowned leader in the precision photochemical etching industry, the team at E-Fab specializes in fabricating titanium components for critical applications across several high-tech industries. Focusing on renewable energy, medical, aerospace, and defense sectors, we leverage advanced manufacturing capabilities to deliver top-quality titanium parts tailored to the most demanding requirements.
In this article, we look at what makes titanium such a valuable metal, the versatility etched titanium offers, its unique advantages, and how it’s shaping the future of precision metal manufacturing.
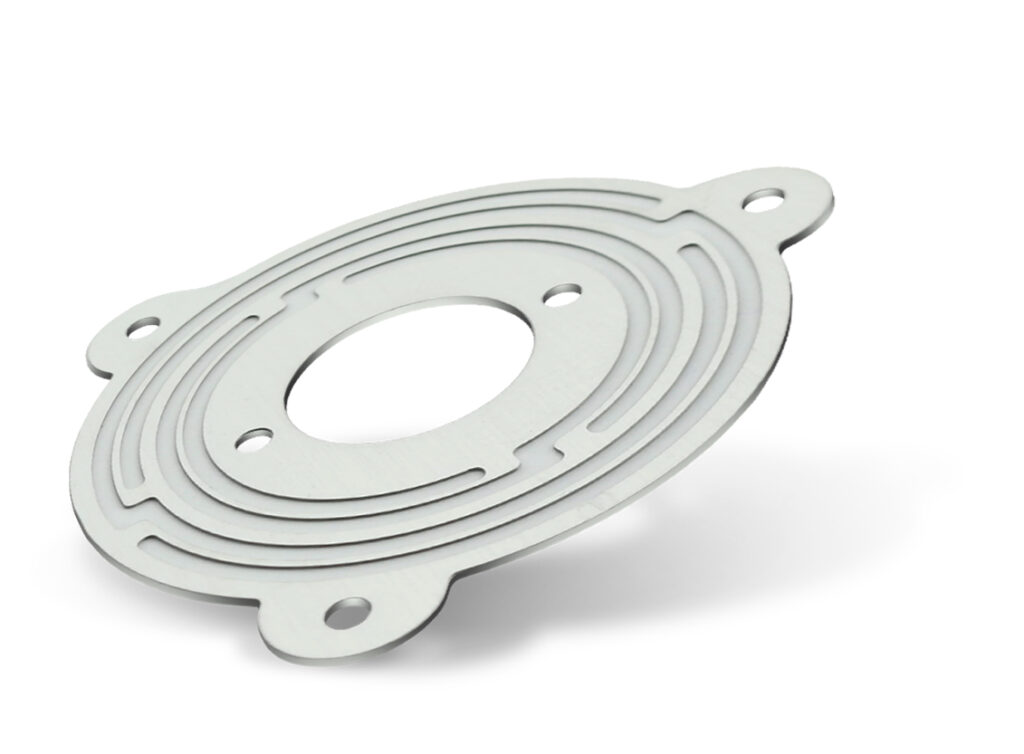
The Wonder Metal: Understand Titanium
Often called a wonder metal due to its lightweight, unmatched strength, and corrosion-resistant properties, titanium is driving innovation and advancement in precision metal manufacturing.
Its remarkable strength allows for the production of lightweight yet robust components, making it an indispensable material in aerospace, automotive, and medical applications. The metal’s impressive strength-to-weight ratio enhances fuel efficiency and maneuverability, while its strength supports higher payload capacity in transportation settings.
Titanium’s exceptional corrosion resistance ensures longevity in harsh conditions, making it ideal for applications exposed to corrosive elements or extreme temperatures. Its biocompatibility also makes it suitable for medical implants and devices, where compatibility with the human body can be the difference between life and death.
Titanium’s uniform surface and excellent machinability make it a great material for etching intricate patterns and features with incredible precision.
Boasting an impressive array of unique properties, it’s easy to see why this metal has firmly positioned itself as the preferred choice for etching applications across various critical industries.
Working with some of the world’s most important industries, E-Fab manufacturers are experts at etching and forming titanium to precise standards and specifications. With decades of experience and expertise in a suite of processes, we’ve developed a reputation for delivering innovative, accurate, and reliable titanium-etched parts.
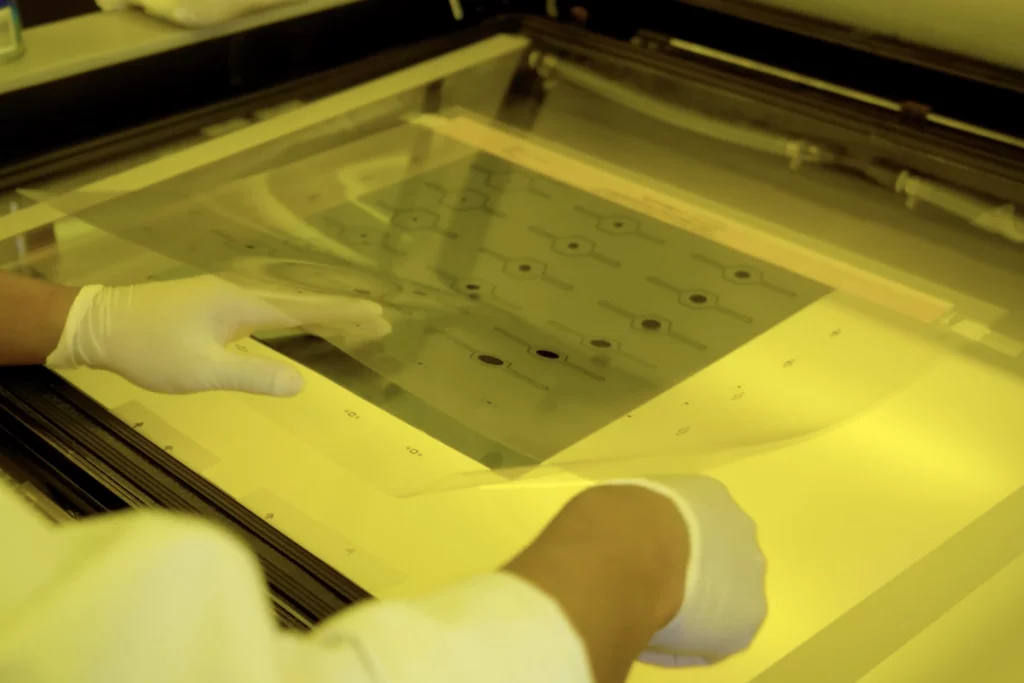
Versatility Across Industries
Etched titanium has a unique combination of strength, lightweight, corrosion resistance, and biocompatibility, making it the preferred material for various industrial applications. These include:
Aerospace:
Titanium etching is crucial in aerospace, where weight reduction is critical. Titanium components with etched surfaces offer significant weight savings and enhanced aerodynamics. From turbine blades to structural components, etching allows for the creation of complex geometries that improve fuel efficiency and overall performance.
Etching also offers precise control, ensuring the safety and performance of these components and contributing to the efficiency and reliability of aerospace technology.
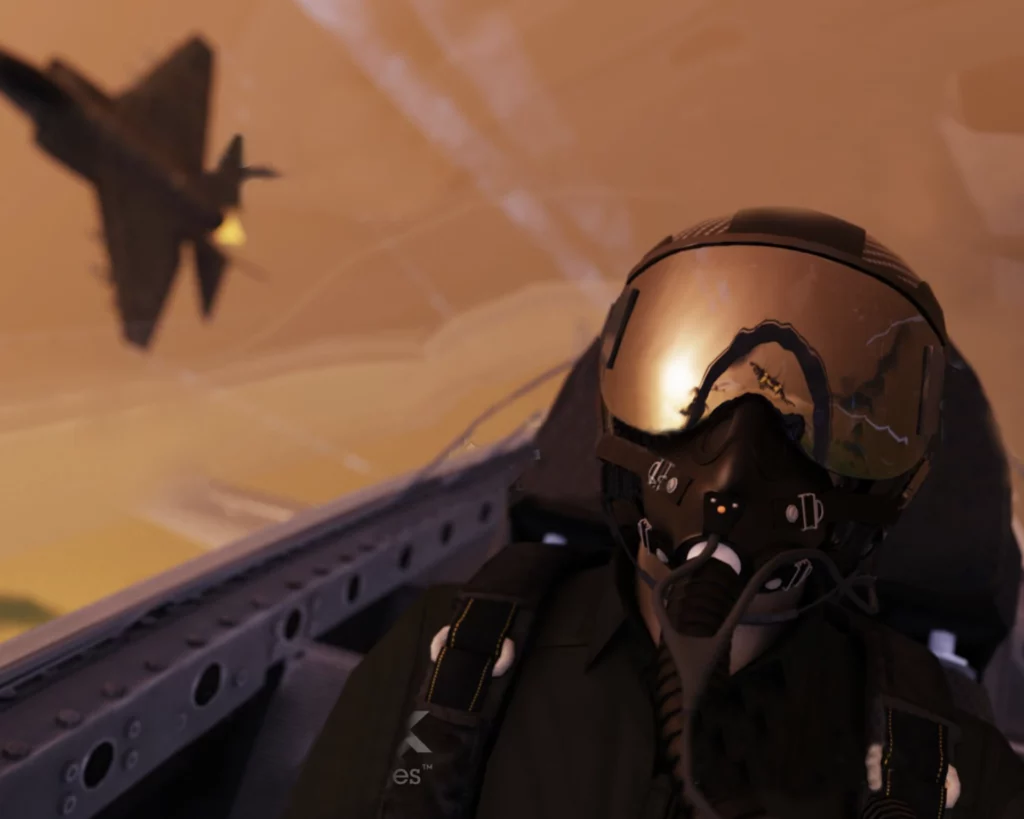
Renewable Energy:
Titanium’s unique properties, such as its exceptional strength-to-weight ratio, corrosion resistance, and durability, make it ideal for producing intricate components critical to renewable energy production.
Using photochemically etched titanium components enhances the efficiency and longevity of various renewable energy technologies, including bipolar or unipolar plates for fuel cells and electrolyzers, frames, and structural components.
Specializing in energy-grade alloys, E-Fab has become a leader in manufacturing exceptionally accurate and precise components built to perform in critical energy sector applications.
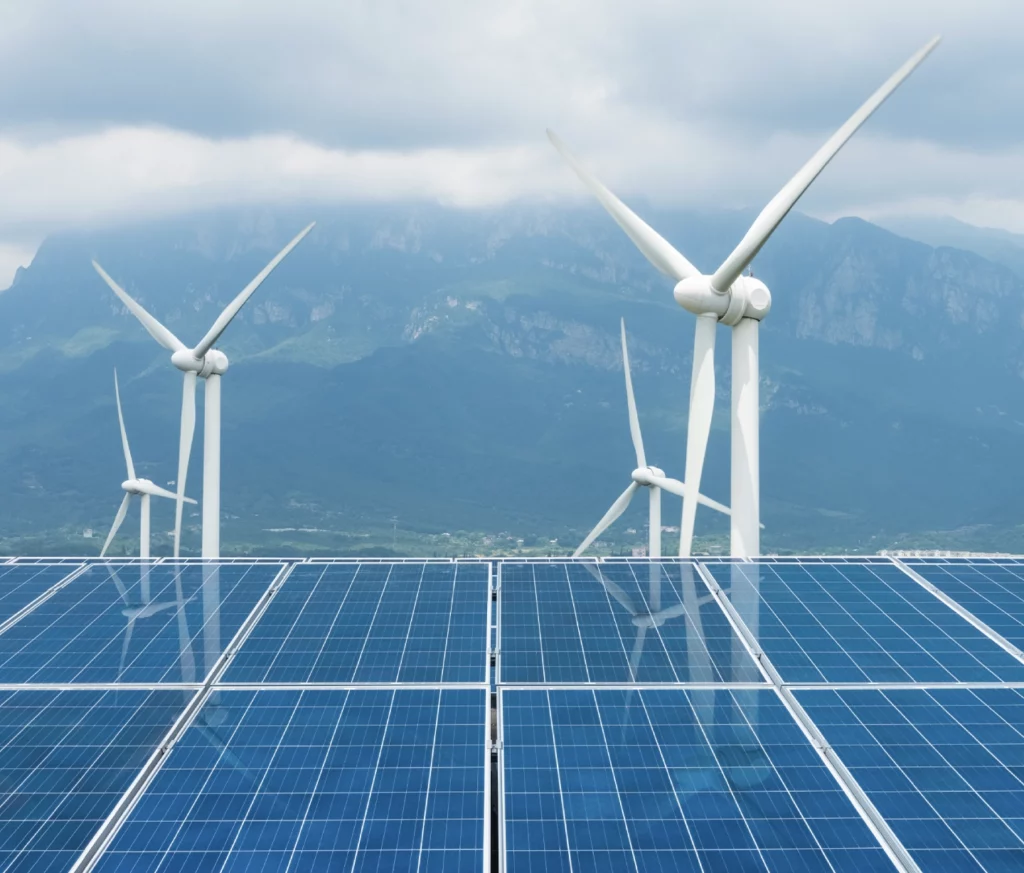
Medical Devices & Implants:
Titanium’s biocompatibility and corrosion resistance make it an ideal material for medical implants, instruments, and devices where precision and durability are non-negotiable.
Customized surface textures can promote better osseointegration, improving patient outcomes. This unique bond enhances stability and longevity, turning titanium etching into a life-changing technology.
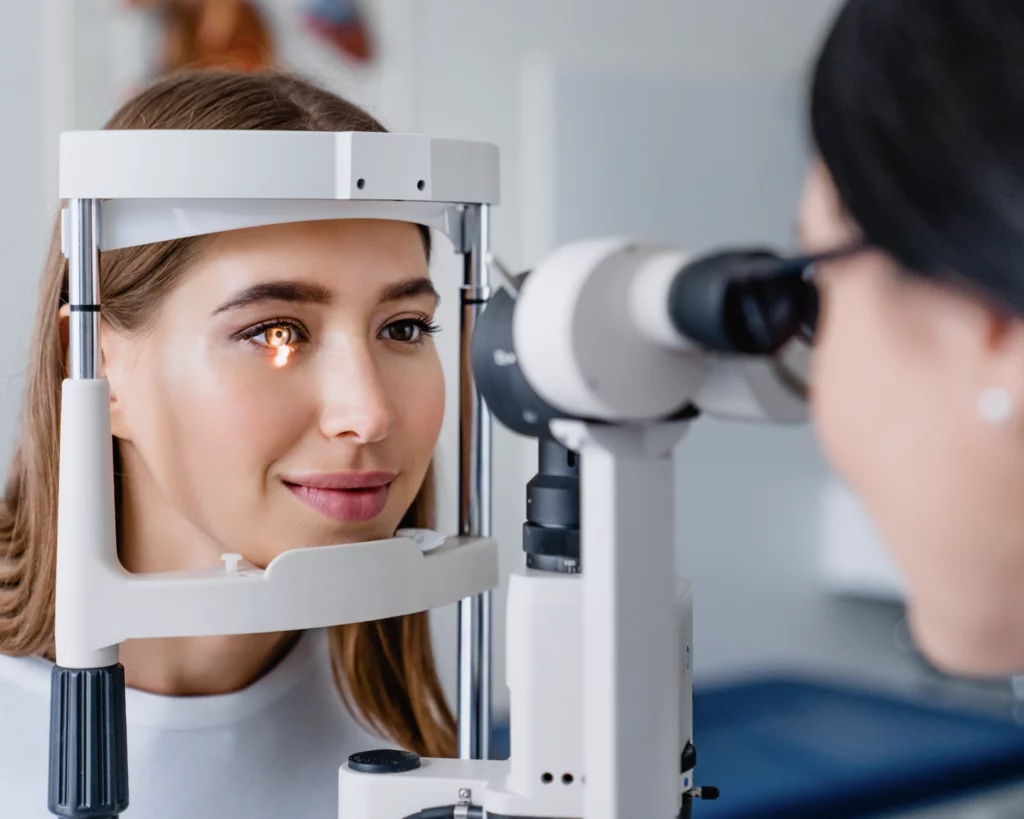
Electronics:
The titanium etching process is essential to producing hardware, circuit boards, and microelectronic components in electronics manufacturing because it creates intricate patterns and features necessary for the functionality of modern electronic devices.
While the metal’s lightweight properties and corrosion resistance make it a smart choice for hardware, its lack of electrical conductivity means engineers do not spec it for electrical components.
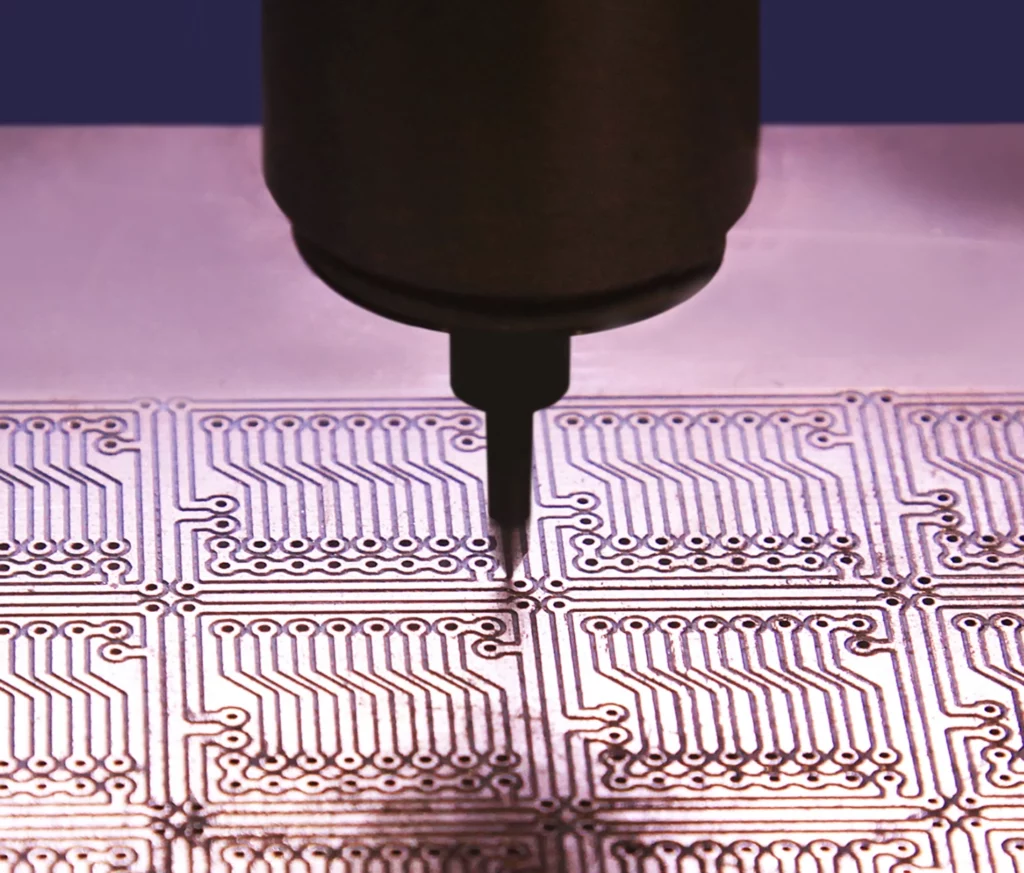
Automotive:
In the automotive industry, titanium etching is the trusted process for applications such as fuel cells, exhaust systems, and lightweight structural components.
Etched titanium parts make vehicles more reliable and environmentally friendly. They also improve fuel efficiency, reduce emissions, and improve durability.
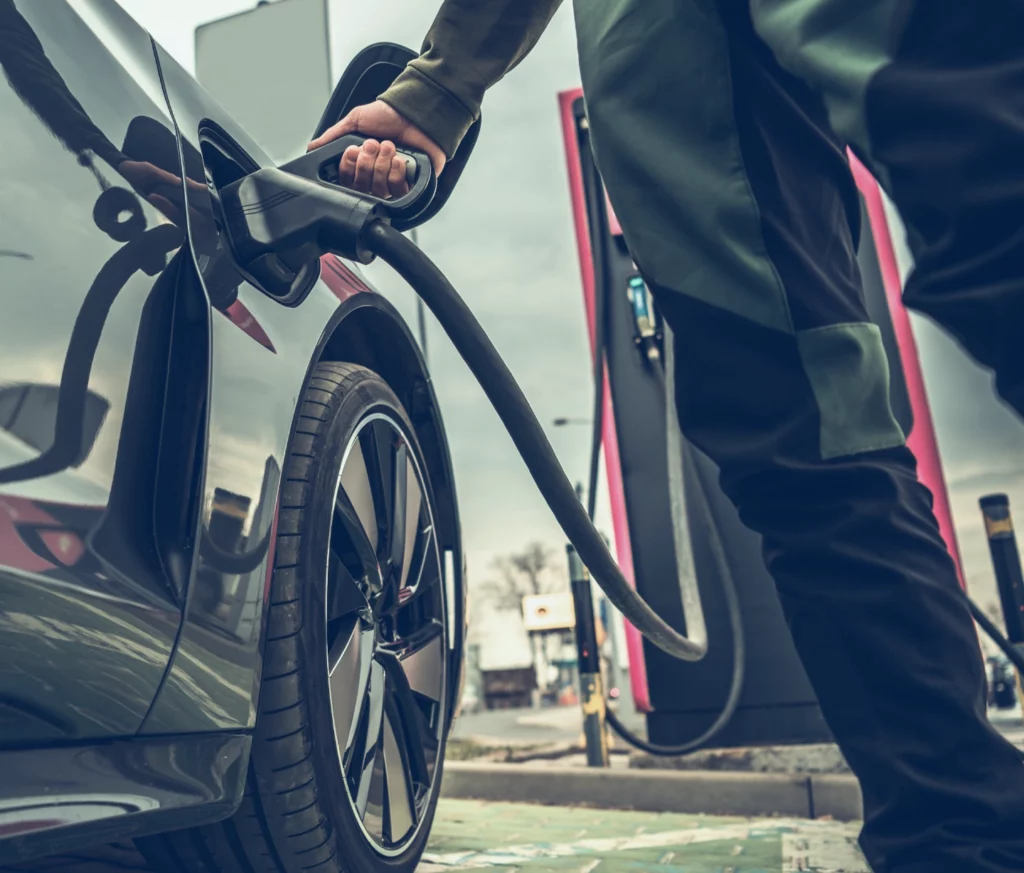
Chemical Processing
The corrosion resistance of titanium-etched components makes them an excellent choice for chemical processing. The etching process crafts tanks, pipes, and valves that can withstand the most corrosive environments, ensuring the longevity and safety of critical components.
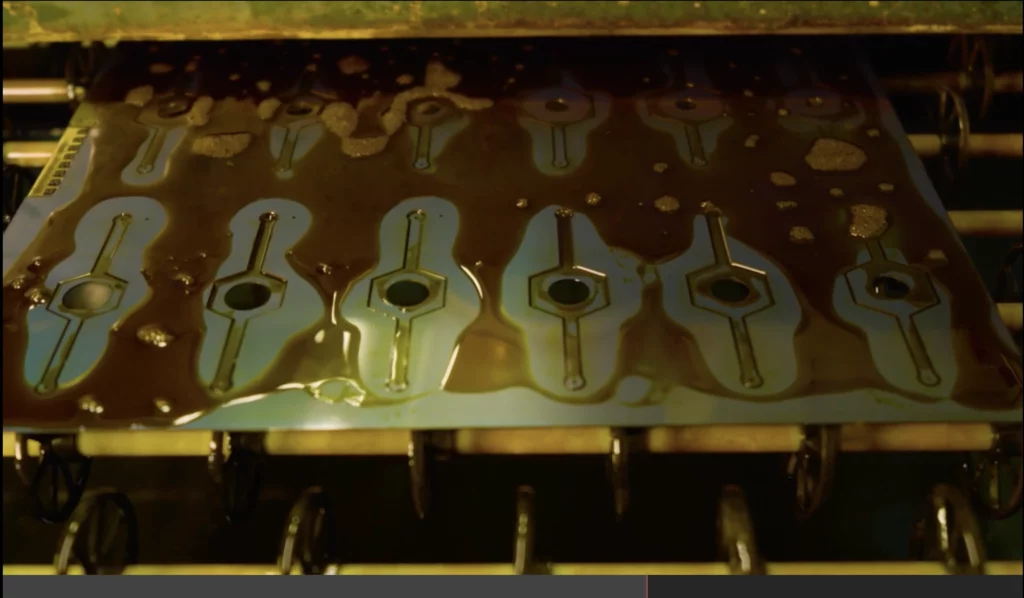
Industry | Applications/Titanium Components |
Technology | EMI shielding cases, heat sinks, connectors, brackets |
Aerospace | Airframe components, compressor blades, fuel system components, satellite structures, spacecraft components |
Communications | Antenna frames and components, mobile device micro-components, fiber optic systems |
Defense | Ballistic armor inserts, critical aircraft structural elements, sensors for naval ships |
Medical | Orthopedic implants (e.g., joint replacements, bone screws), dental implants, surgical instruments, stents, heart valves |
E-Fab is a leading provider of photochemical etching manufacturing services, delivering parts with complex or intricate geometries and tight tolerances for customers across various industries.
We operate two dedicated manufacturing lines solely for etching titanium and titanium alloys. These lines are optimized for processing various titanium grades, including Alpha, Beta, and Alpha-Beta alloys, ensuring superior quality and consistency in every component produced.
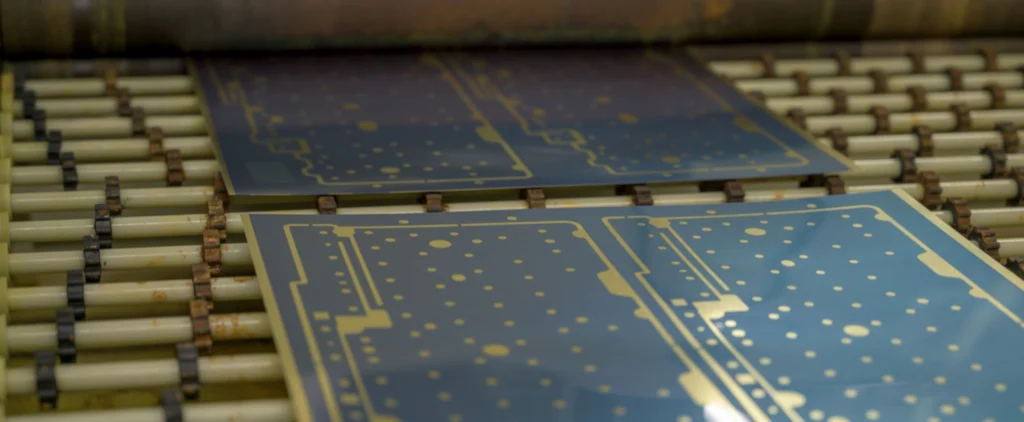
Key Benefits of Titanium Etching for Modern Manufacturing
Titanium’s exceptional flexibility has revolutionized precision metal manufacturing, enabling the creation of intricate, durable components.
This innovative photochemical etching process offers a range of benefits to both manufacturers and end users, making it the ideal choice for applications where precision, performance, and durability are non-negotiable.
The main advantages of titanium etching include:
- Precision: Titanium etching allows for the creation of intricate designs and patterns with micron-level accuracy, ensuring consistent quality and performance.
- Enhanced Bonding: Etching doesn’t just stop at surface modification; it creates a textured surface perfect for improving the adhesion of coatings, adhesives, or other materials. This advantage is invaluable in sectors like medical devices and aerospace, where bonding strength is critical.
- Customization: Titanium etching’s flexibility enables customization to meet specific application requirements, whether optimizing mechanical properties or enhancing aesthetics.
- Cost-effectiveness: Despite its advanced capabilities, titanium etching can offer cost savings compared to traditional machining methods, thanks to reduced material waste and production time.
- Corrosion Resistance: Titanium is renowned for its corrosion resistance. After the PCE process, coatings are available to enhance the metal’s ability to withstand even the harshest environments, such as marine or chemical processing applications.
With a proven track record of excellence and a comprehensive suite of certifications, E-Fab stands as a trusted partner for clients seeking reliable and compliant solutions for their titanium etching needs.
Our commitment to precision, quality, and compliance ensures that every component we produce meets the stringent requirements of our valued customers, making E-Fab the preferred choice for high-tech industries worldwide.
Titanium Etching is Driving Innovation Across Industries
As technology evolves and advances rapidly, titanium etching technology is poised to unlock new possibilities and capabilities for several key industries. If harnessed correctly, it has the potential to drive innovation, improve product performance, and create new opportunities for growth in aerospace, medical, electronics, automotive, and beyond.
Laser-based etching techniques enable even finer details and faster processing times than traditional chemical etching. As a result of this trend, titanium etching will not only become more precise and efficient but also open the door to new applications in fields such as microelectronics and nanotechnology.
Integrating artificial intelligence and machine learning algorithms into etching processes allows for real-time optimization and quality control, leading to higher yields and lower production costs. Additionally, eco-friendly etching solutions, such as water-based or solvent-free processes, align with sustainability goals while reducing environmental impact.
E-Fab continually invests in research and development to stay at the forefront of technological advancements in titanium etching. Our experienced engineering team can explore innovative process improvements and optimizations to enhance the efficiency, precision, and cost-effectiveness of titanium etching.
By leveraging cutting-edge technologies and best practices, we can help clients stay ahead of the curve and achieve competitive advantages in their respective markets.
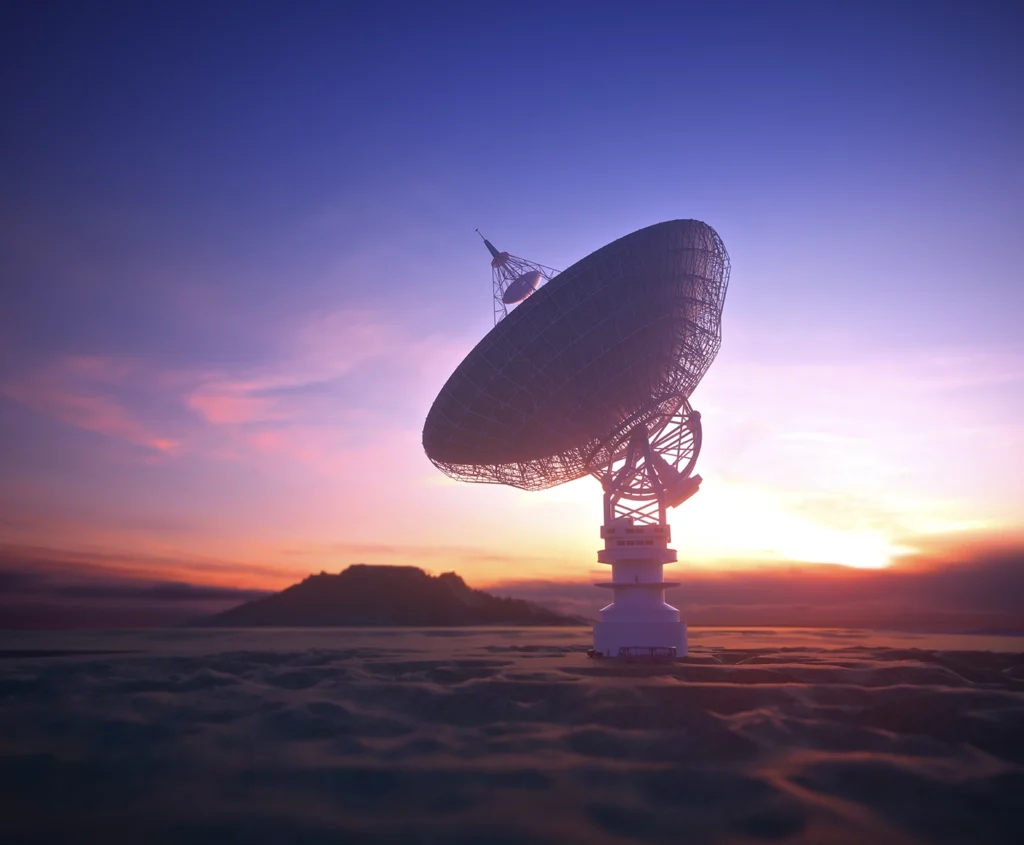
Your Trusted Partner for Titanium Etching
Titanium etching is the pinnacle of precision metal manufacturing, offering a level of versatility, durability, and customization that other etched metals simply can’t match.
From aerospace to medical devices, electronics, automotive, and beyond, the applications of titanium etching continue to expand, driving innovation and pushing the boundaries of what’s possible in modern engineering and design.
E-Fab is a renowned leader in the precision photochemical etching industry. We specialize in fabricating titanium components for critical applications across a wide range of high-tech industries.
What sets E-Fab apart is our commitment to quality and compliance. With ISO 9001-2015, AS9100D, and ITAR certifications, we adhere to the highest industry standards for quality management, aerospace, and defense requirements.
Collaboration is at our core. We partner with clients, suppliers, and industry stakeholders to develop customized, proactive solutions to their biggest challenges. By fostering open communication and collaboration, E-Fab can work closely with you to deliver titanium-etched parts to precise standards and specifications.