We’ve Mastered the Use of Tungsten for Precision Parts
Why Tungsten?
Tungsten is a refractory metal known for its exceptional properties, including the highest melting point of any metal (3422°C / 6191°F), superior strength, and high density. It offers increased corrosion resistance, making it highly durable in harsh environments, and withstands exposure to corrosive substances compared to many other metals.
These characteristics make it an ideal material candidate when used for intricately etched parts and components.
However, tungsten also has some characteristics that make it difficult to manufacture using legacy or traditional methods.
Photochemical Etching Process

Traditional Machining Methods and Why They Aren’t as Effective
Standard subtractive manufacturing processes for hard metals that require a high level of precision are typically designated to a milling machine or electrical discharge machine (EDM), both of which provide extremely high rates of accuracy and repeatability.
Each process still has downsides or somewhat negative effects, either on the material or the machine, at some point or another, but all of these methods collectively fall short when dealing with thinner metals that require highly intricate designs.
Tungsten has a handful of properties that make it more challenging than others, which ultimately limits its application and utilization in specific industries.
For example, material hardness leads to shorter tool life on a mill. The brittle nature of Tungsten means there is a higher chance of cracking during the machining process, even if using a slow-moving wire EDM.
EBM technology, as impressive as it is, still has limitations with design for manufacturability. Each of these processes is hindered by the ability to handle intricate, multi-axis parts, with the availability of both tooling and technology to support it.
All of these factors drive up the manufacturing costs associated with traditional methods because of the time required for multiple setups and the consumables required, which then restrict the use of the material in certain designs and applications.
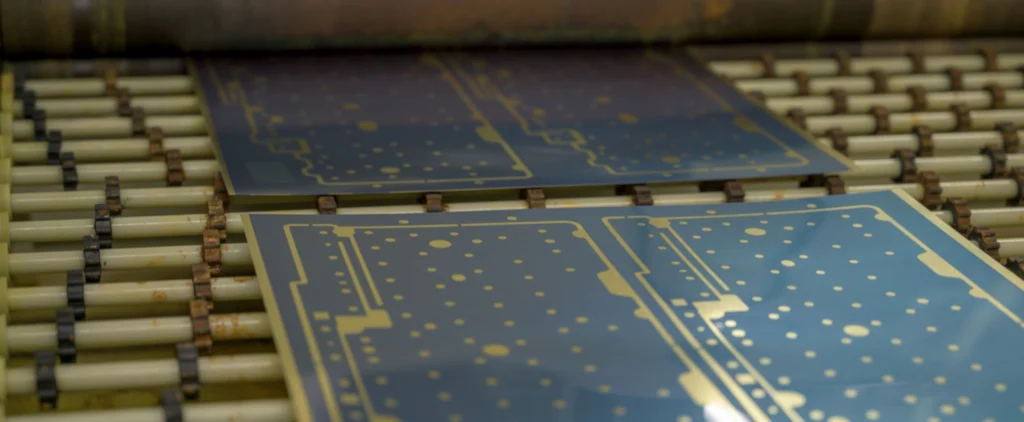
Understanding the Photochemical Etching Process for Tungsten
Photochemical etching (PCE) is a non-contact, precision fabrication process used to create intricate metal parts while mitigating metallurgical stress.
The process involves coating the material with a light-sensitive photoresist, exposing it to ultraviolet light to pattern a design, and developing the exposed areas to reveal the desired pattern.
More specifically, the process starts with immersing tungsten components into a chemical solution known as tungsten etchant, a mixture of mildly alkaline potassium ferricyanide and potassium hydroxide, which selectively dissolve the unprotected areas.
PCE offers several advantages over traditional machining methods, including the creation of intricate designs with precise features while also limiting material waste. This alternative form of subtractive manufacturing provides an extremely high degree of precision, repeatability, and accuracy, making it a preferred method for specific applications within the aerospace, medical, and semiconductor industries, whether for low-volume prototype options or mass production.
From This
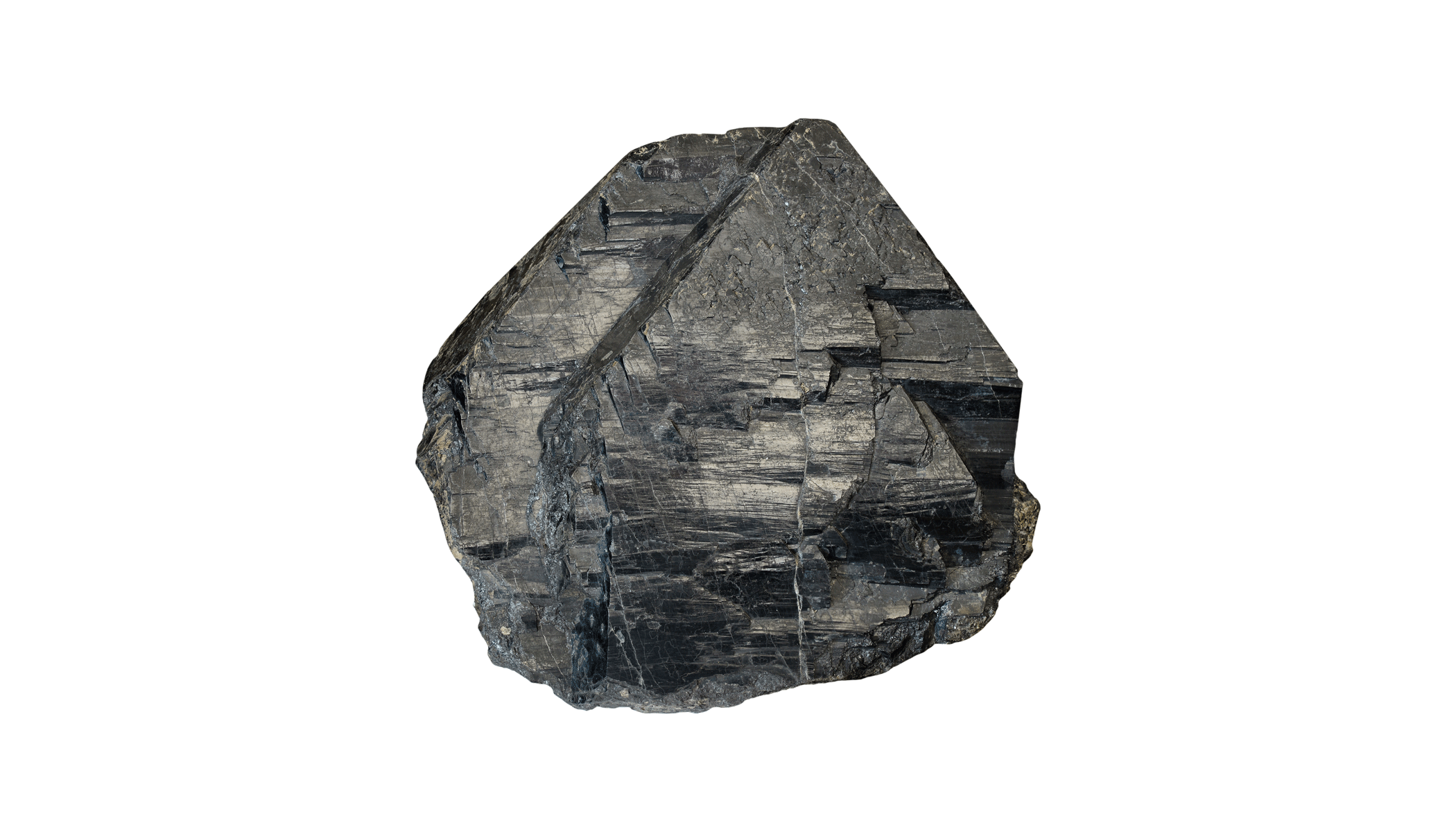
to This
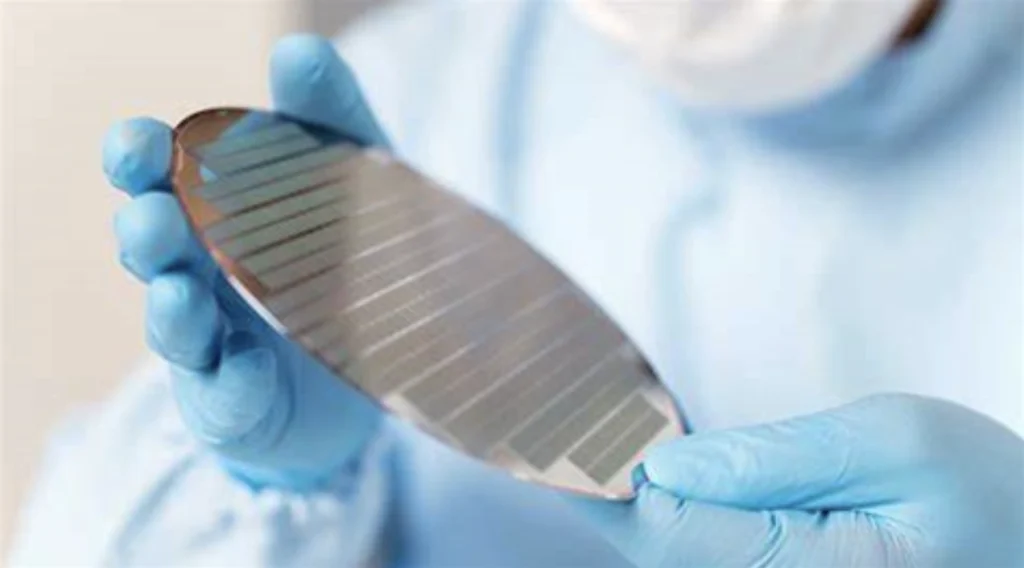
Challenges for Tungsten-Specific Applications
The biggest challenge with PCE for tungsten is the material integrity itself. Since tungsten is a brittle material, any manufacturing process can result in substantial warping or cracking, especially when it is etched from both sides. The non-contact process eliminates this stress and distortion, critical when producing extremely intricate, small parts integrated into components used in the medical and semiconductor industries. This becomes more important as parts and components continue to get smaller while still demanding the same, if not more, performance and reliability.
We’ve developed a specific manufacturing process to mitigate these issues using CNC laser cutting and machining in conjunction with PCE to create complex parts. We provide custom solutions for our customers while ensuring the material integrity and longevity coincide with performance consistency throughout the application’s life cycle. This process maintains tight tolerances while also being a cost-effective option in comparison to traditional machining methods.
E-Fab Continually Provides Solutions for Tungsten PCE
Photochemically etched tungsten is a versatile and indispensable material relied on by some of the world’s leading industries. Tungsten’s unique properties, combined with the etching process’s precision and intricacy, have quickly become a preferred material in various high-performance applications, especially in the aerospace industry, where the environmental effects on the material are literally out of this world.
At E-Fab, we leverage our extensive knowledge of the etching process and our deep understanding of the molecular behavior of tungsten to ensure that we are producing the highest quality parts at every level. This is supported by our proven ability to hold tolerances below 70 µm on large arrays (up to 300 x 600 mm). Through our process, we achieve unprecedented stability for the most demanding applications.
We also provide a full range of services that bring additional value to your tungsten application, including forming and plating that produce enhanced properties specific to your project, making E-Fab a preferred partner within many supply chains.
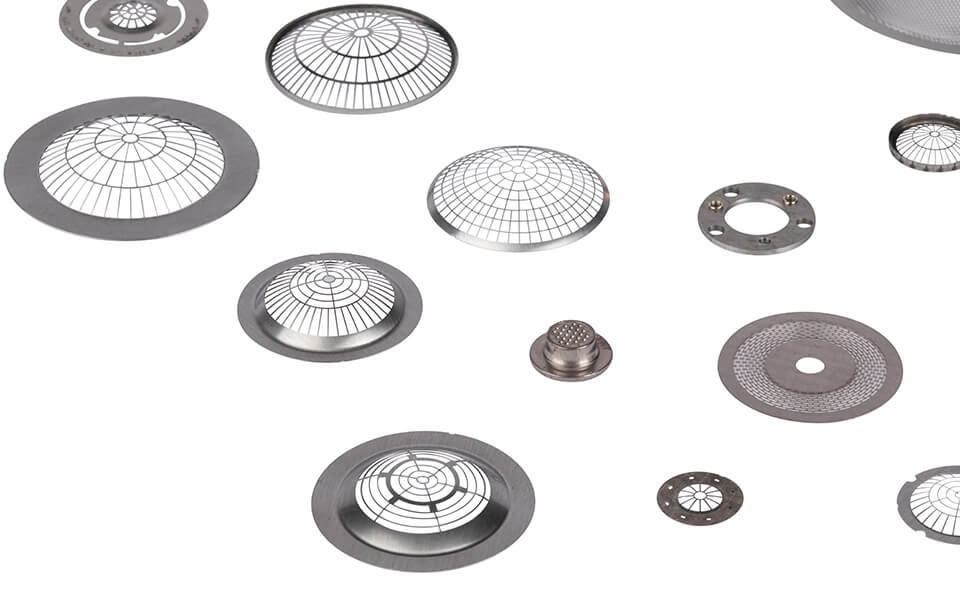
Tungsten Applications Across Multiple Industries
As technology continues to advance, industries are shifting from what was a legacy understanding of an application to an entirely new approach to problems that, beforehand, were simply isolated to a bucket labeled, “This is the best we can do,” where now the new question is, “How can we do it better.”
Medical
Equally as demanding, the medical industry continues to produce new technology that leads to scientific discoveries and ultimately improves the quality of life for everyone. Radiation shielding and surgical tools benefit from the technology provided by PCE for tungsten applications, as they can endure the corrosive environments presented.
Electronics
Whether it be heat sinks, electrodes, or thermal management systems, in space, on Earth, and in between, tungsten provides a versatile option for specific applications that endure harsh and corrosive conditions.
Ready to Get Started?
When creating a partnership, like the parts we produce, E-Fab looks to create longevity. We understand the importance of consistency and reliability within the supply chain at every level, which is why we maintain a strict quality assurance program that covers each aspect of the manufacturing process.
From concept to completion, E-Fab provides integrated consulting, engineering, and manufacturing support with an extensive history of being trusted for our reliability, accuracy, and innovation for tungsten solutions. We look forward to the opportunity to show you and your team what we can do for you. No matter the challenge, we are ready for it.
