What to look for in a busbar manufacturer, the power of the photochemical etching process, and the reasons E-Fab has led the way in precision busbar manufacturing.
Responsible for powering critical systems across a wide range of industries, the humble busbar is an unsung hero of modern engineering.
From aerospace to automotive, renewable energy to telecommunications, these unassuming metal bars facilitate the seamless flow of electricity in power distribution systems. But when the failure of these systems puts safety, security, and lives at risk, you need to know they are powered by busbars built to the highest standards.
Offering cutting-edge solutions that combine the functionality of a stiffener with the power and ground distribution capabilities of a busbar, E-Fab is redefining the standards of busbar manufacturing. Renowned for consistently delivering reliable, high-quality busbars for a wide range of critical applications, E-Fab has become the trusted manufacturer for leading industries worldwide.
In this article, we explain what to look for in a busbar manufacturer, the power of the photochemical etching process, and the reasons E-Fab has led the way in precision busbar manufacturing.
What is a busbar?
A busbar, also known as a bus bar, is a metallic strip or bar, typically manufactured in copper or brass, that conducts electricity within a distribution board, circuit board, battery bank, power supply unit, or other electrical apparatus. They are designed to conduct substantial currents of electricity, more than can be provided by standard circuit board traces.
Busbars are typically made of copper, brass, or aluminum and can be insulated or non-insulated.
To learn more about the importance of busbars, read our article on why busbars & stiffeners are essential in circuit boards.
Key applications of busbars
Busbars are driving innovation across various sectors as essential components for power distribution and electrical connectivity.
Let’s explore the pivotal role that busbars play in powering our modern world.
Aerospace: Reliability and performance are paramount in the aerospace industry. Busbars provide essential electrical connectivity for avionics systems, flight control systems, and onboard electronics. Their lightweight yet durable construction ensures efficient power distribution while withstanding the rigors of flight, contributing to aircraft safety and efficiency.
Automotive: Busbars are vital in powering electric and hybrid vehicles, providing a centralized electrical distribution network for batteries, motors, and onboard electronics. By optimizing space and reducing weight, busbars help improve vehicle efficiency and range, accelerating the transition toward sustainable transportation solutions.
Renewable Energy: Busbars efficiently convert and distribute power from solar panels, wind turbines, and other renewable sources. By enabling the seamless transmission of electricity within solar inverters, wind turbine generators, and energy storage systems, busbars play a key role in maximizing energy output and grid stability.
Telecommunications: In an industry where uninterrupted connectivity is essential, busbars serve as the backbone of data centers, telecom towers, and network infrastructure. By providing reliable electrical connections for servers, switches, and networking equipment, busbars ensure seamless data transmission and communication services for businesses and consumers alike.
Industrial Machinery: A busbar facilitates efficient power distribution to motors, actuators, and control systems in various industrial applications, such as manufacturing, automation, and robotics. Its robust design and high current-carrying capacity make it ideal for powering heavy machinery and equipment, optimizing productivity and uptime in industrial operations.
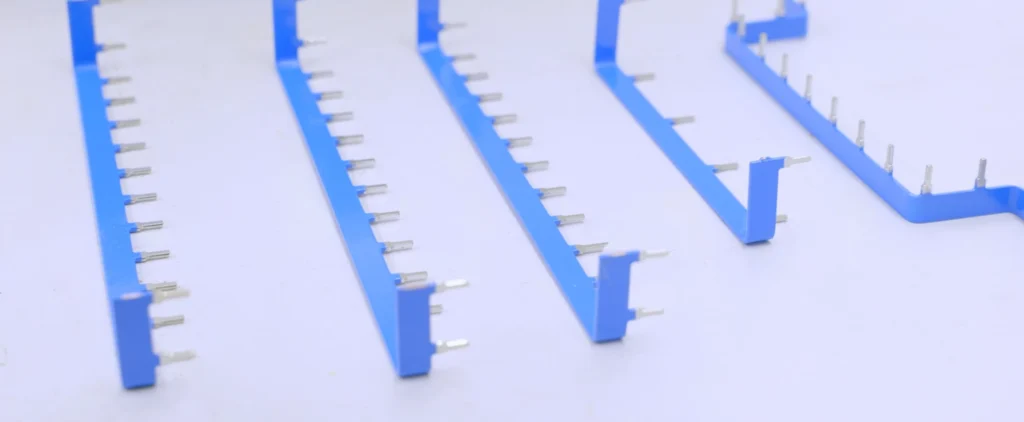
What to consider when choosing a busbar manufacturer
To ensure optimal performance and reliability, you need to consider several key factors when selecting a busbar manufacturer.
Start by evaluating the manufacturer’s expertise in material selection, ensuring they offer a range of high-quality materials such as copper, aluminum, and their alloys to meet the specific requirements of the application.
When it comes to busbars, precision is paramount, so look for a manufacturer with advanced machining capabilities and stringent quality control processes to guarantee tight tolerances and consistent performance. Customization options are essential to tailor busbars to unique specifications, so opt for a manufacturer that offers flexibility in design, size, and configuration.
It’s also vital to consider lead times and production capacity to ensure your orders can be delivered on time, especially for time-sensitive projects. While cost-effectiveness is crucial, prioritize value over price by selecting a manufacturer that offers competitive pricing without compromising on quality or service.
With more than four decades of manufacturing experience and four L-3 Supplier of the Year Awards, E-Fab is a proven partner for any busbar project. With years of experience in photochemical etching and precision engineering, we ensure the highest quality and reliability in every busbar we produce.
Our state-of-the-art manufacturing processes and stringent quality control measures guarantee superior performance, durability, and consistency, meeting the demanding requirements of various industries.
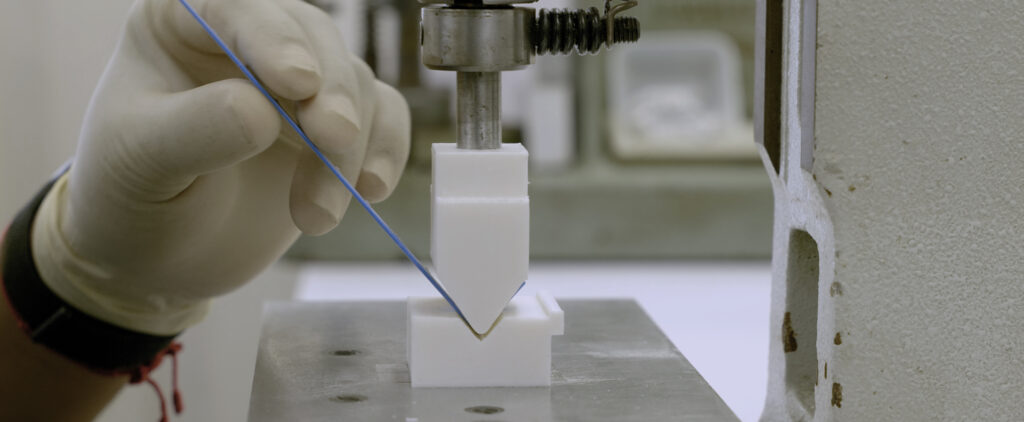
Building better busbars: The E-Fab difference
At E-Fab, we’ve been producing busbars since our earliest days, producing these precision parts for the telecommunications, defense, medical, and electronics industries.
There are numerous advantages to working with the E-Fab team, and it all starts with our focus on collaboration and exceptional customer support. From initial concept development to final delivery, our team works closely with clients to understand their needs, provide technical expertise, and deliver customized solutions that exceed expectations. We ensure a seamless experience for every client with responsive communication and dedicated support.
So what makes E-Fab’s busbars special? It’s a question we often get asked, and it comes down to three key factors:
Dielectric Coating with High Current Capacity:
Unlike traditional busbars, our busbars feature a dielectric coating that enhances stiffness while enabling them to carry ground and power distribution of up to 128 amps. This innovative design eliminates the need for heavy traces, ensuring optimal performance and efficiency in electrical power distribution systems.
Customizable Features for Tailored Solutions:
We understand that every application has unique requirements. That’s why we offer customizable busbar features, including pins, spacing, height, length, surface holes or slots, top and end tabs, and more. Whether you need specific pinning configurations or additional mounting options, we can tailor our busbars to your exact specifications.
Multi-Layer Busbars for Enhanced Functionality:
We specialize in manufacturing multi-layer busbars, providing versatile solutions for complex power distribution applications. Our two-layer busbars feature staggered pin configurations with alternating power and ground pins, maximizing space efficiency while delivering superior performance. With our multi-layer busbars, you get the benefits of advanced stiffener features combined with extra power and ground buses in a space-saving design.
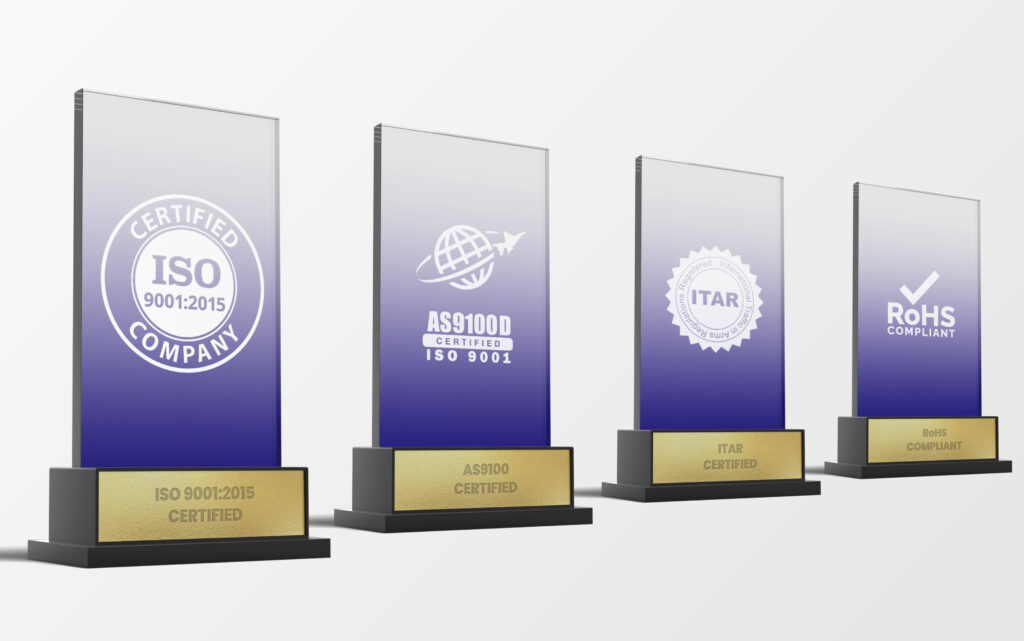
A bright future for busbars
Busbars already play a crucial role in powering critical systems and driving innovation across a wide range of industries. But as technology evolves and the demand for efficient, sustainable solutions grows, their importance will only rise.
By embracing the versatility, reliability, and efficiency of busbar technology, industries can unlock new possibilities and pave the way toward a brighter, more connected future.
Do you need a proven partner for your busbar manufacturing? The team at E-Fab is here to help.
Our knowledgeable team assists clients with every step of the project, from consultation to design to manufacturing to delivery, and provides high-quality product solutions that precisely satisfy your requirements.
Our precision photochemical etching process and industry-leading equipment in our ISO 9001:2015 certified facility ensure that every component we fabricate is of the highest quality. Plus, we are well-versed in working with a range of materials, including copper, brass, and aluminum.