In this article, we examine the main differences, benefits, and drawbacks of chemical etching vs. laser cutting so you can make an informed decision about your manufacturing needs.
For any precision metal manufacturing project, choosing the right cutting method is crucial to achieving its specific requirements. With multiple methods available, the choice often comes down to two prominent techniques: chemical etching and laser cutting.
Both methods boast advantages and disadvantages, but which one reigns supreme as the method of choice for achieving better project outcomes?
In this article, we look at each method’s main differences, benefits, and drawbacks so you can make an informed decision regarding your manufacturing needs.
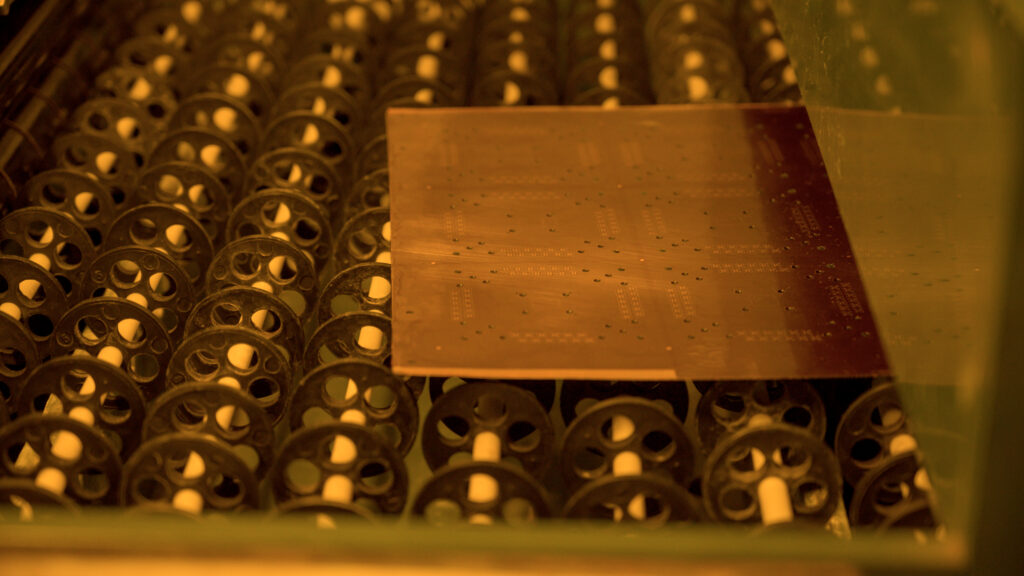
Chemical Etching: Precision Perfected
Chemical etching, also known as photochemical machining (PCM), photochemical etching (PCE), or photochemical milling (PCM), is an exact manufacturing process that utilizes chemical reactions to selectively remove material from metal sheets.
The chemical etching process begins with applying a maskant (photoresist) onto the metal surface, which is then exposed to UV light through a patterned mask. The exposed areas become soluble, allowing the chemical etchant to dissolve the metal, leaving behind the desired shapes or features.
The chemical etching method produces intricate and complex designs with tight tolerances, making it ideal for applications where precision is paramount.
Versatility is one of the key benefits of chemical etching. First, a variety of metals, including stainless steel, copper, aluminum, and titanium, are etchable without inducing thermal stress or distortion. Second, the process is a cost-effective solution for high-volume production because it eliminates the need for expensive tooling and setup costs associated with traditional machining methods.
While chemical etching is a versatile and precise method for manufacturing precision metal components, it does have its limitations.
One significant limitation is undercutting, where the etchant can eat away at the edges of the metal, causing a slight concave shape in the finished part. Undercutting can affect dimensional accuracy, particularly in parts with tight tolerances. Material thickness can be another constraint, as thicker metals require longer etching times and may result in less uniform etching or even incomplete removal of material. The chemical composition and surface properties of certain metals may also limit the range of materials that can be etched effectively using this method.
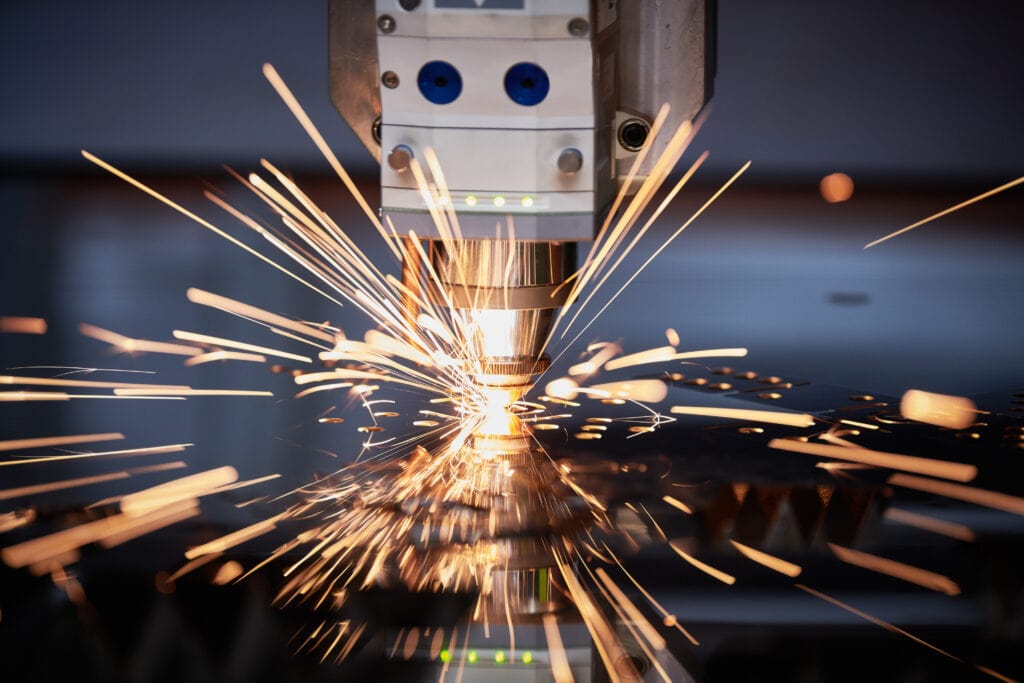
Laser Cutting: Speed and Versatility
Laser cutting relies on a high-powered laser beam to melt, burn, or vaporize material along a predefined path. A computer-controlled system guides the laser beam through a programmed path to achieve the desired cuts. The intense heat generated by the laser vaporizes or melts the metal, creating clean and accurate edges with minimal heat-affected zones.
This method excels in cutting through thick metal sheets quickly and efficiently, making it ideal for applications that prioritize speed and versatility. Laser cutting is commonly used in automotive, aerospace, and electronics industries, where fast turnaround times are crucial.
While laser cutting offers advantages in terms of speed and versatility, it falls short when it comes to achieving the same level of precision and intricacy as chemical etching. The heat generated during the laser cutting process can result in thermal distortion and edge burrs, leading to the need for additional post-processing steps to achieve desired tolerances. Laser cutting is also often limited in its ability to produce fine details and intricate patterns, making it less suitable for applications that require intricate designs.
The Key Differences Between Chemical Etching and Laser Cutting
- Precision and Accuracy
Chemical Etching: Boasts unparalleled precision and accuracy and can achieve intricate designs with tight tolerances down to ±0.001 inches. The chemical process allows for uniform material removal across the entire surface, resulting in sharp, clean edges without inducing thermal stress or distortion.
Laser Cutting: Highly precise, but its accuracy can be affected by factors such as material thickness and laser beam divergence. While laser cutting can achieve precise cuts, the heat generated during the process may cause thermal distortion and lead to deviations from the intended dimensions.
- Material Compatibility and Versatility
Chemical Etching: Highly versatile and compatible with various metals, including stainless steel, copper, aluminum, titanium, and exotic alloys. It can also etch non-metallic materials like ceramics and polymers, making it suitable for a diverse array of applications.
Laser Cutting: Compatible with various metals and non-metals, including steel, aluminum, acrylic, and wood. However, certain materials may require specialized laser systems or additional processing steps to achieve optimal results.
- Complexity of Designs
Chemical Etching: Excels in producing complex and intricate designs, including fine features, small holes, and intricate patterns. The use of photoresist masks allows for precise control over the etching process, enabling the creation of highly detailed components.
Laser Cutting: Well-suited for cutting simple to moderately complex shapes with straight lines and curves. While it can produce intricate designs, the process may struggle with fine details and sharp corners, particularly in thicker materials.
- Cost and Scalability
Chemical Etching: Cost-effective for both prototyping and high-volume production. The absence of tooling and setup costs, coupled with the ability to etch multiple parts simultaneously on a single sheet makes chemical etching an economical choice for many applications. The digital nature of the process also allows for quick and affordable modifications to the photo tool, reducing both time and expenses.
Laser Cutting: Equipment and maintenance costs can be relatively high, especially for high-powered laser systems. The need for protective gasses and auxiliary equipment also adds to operational expenses. However, laser cutting may offer cost advantages for certain applications with low to medium production volumes.
- Burrs and Stress-Free Manufacturing
Chemical Etching: A non-contact process that eliminates the formation of burrs and stress-induced deformation, resulting in clean, burr-free parts with minimal post-processing requirements, ensuring high-quality outcomes
Laser Cutting: Can generate heat, leading to thermal distortion in the metal being cut, particularly in thin or heat-sensitive materials. This can potentially affect the dimensional accuracy and geometric integrity of the finished parts.
While both chemical etching and laser cutting have their strengths, the choice between them depends on the application’s specific requirements. For industries that demand unparalleled precision, intricate designs, and cost-effective manufacturing solutions, the advantages chemical etching delivers often make it the preferred option.
Factors to Consider When Choosing Between Chemical Etching and Laser Cutting
Several factors must be considered when determining whether chemical etching or laser cutting is best suited for your manufacturing needs, including project requirements, budget constraints, and lead times required to achieve optimal results.
Project Requirements:
When choosing between the two processes, consider factors such as precision, complexity, and material compatibility. If the project involves intricate designs with tight tolerances, chemical etching may be preferred due to its ability to achieve precise results without inducing thermal stress or distortion. Laser cutting may be more suitable if the project requires rapid cutting of simple to moderately complex shapes.
Budget Constraints:
Chemical etching offers cost-effective prototyping and high-volume production solutions, as it eliminates the need for expensive tooling and setup costs associated with traditional machining methods. Thanks to the ability to etch multiple parts simultaneously on a single sheet, material waste and production costs are also reduced. Initial setup costs for laser cutting can be higher, primarily due to the investment in laser equipment and programming. It may offer cost advantages for smaller production runs or projects with frequent design changes, as it does not require custom tooling.
Lead Times:
Chemical etching typically has shorter lead times than laser cutting, as it does not require the fabrication of custom tooling or setup of laser parameters. Chemical etching’s batch processing capabilities also allow for rapid production of multiple parts simultaneously, further reducing lead times. Laser cutting may offer faster cutting speeds for certain materials and thicknesses, which can be advantageous for projects with tight deadlines.
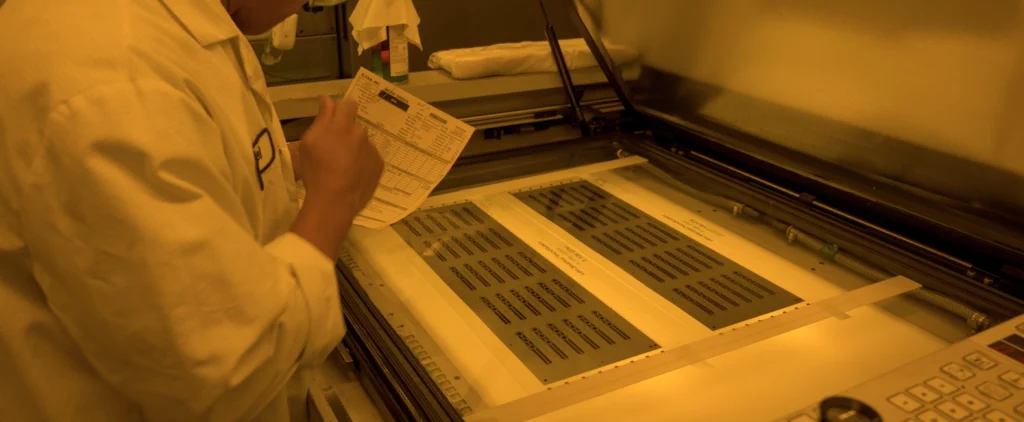
Making the Right Manufacturing Choice
While both chemical etching and laser cutting have their merits, chemical etching emerges as the clear winner in terms of precision, customization, and cost-effectiveness. With its ability to produce intricate designs with unparalleled accuracy and repeatability, chemical etching is preferred for industries where precision is non-negotiable.
Chemical etching’s flexibility and cost-effectiveness also make it a versatile solution for a wide range of applications, from electronics and medical devices to automotive and aerospace components.
E-Fab is a leading manufacturer specializing in photochemical etching services. With years of experience in the industry, E-Fab has developed expertise in delivering high-quality precision components for various applications. We use industry-leading photochemical machining equipment to turn a variety of metal alloys and composite materials into parts for a wide range of industries using chemical etching and various wet machining technologies.
Our innovative processes and expert staff ensure that every component we fabricate is of the highest quality.
Our Photo Etching areas of expertise include:
- Design/engineering assistance
- Material selection/metrology
- CNC machining (including micromachining)
- Lamination
- Heat treating
- Electro and electroless plating
- Joining (including welding, wire bonding, soldering, and braising)
At E-Fab, we’re not just specialists in photochemical etching, forming, and bonding—we’re your partners in turning complex ideas into precise parts for any industry, anytime. Discover our diverse capabilities and commitment to quality by viewing our gallery today.