Implantable devices like stents and pacemakers are crucial for life-saving medical procedures, greatly improving patients’ safety and quality of life.
Despite the rapid advancements in modern medical technology, the biocompatibility of implantable devices remains a critical issue, limiting their longevity and functionality. The foreign body reaction to implantable devices also presents a significant risk for patients.
Working with non-toxic, compatible materials like medical grade titanium, the innovative photochemical etching (PCE) process is solving these challenges by producing precise, burr-free parts that perform reliably while reducing the risk of rejection.
E-Fab is a leader in photochemical etching, producing precise fabrication of custom metal components with intricate designs and tight tolerances that are perfect for use in various medical devices and equipment. ISO 9001 certified, we ensure all our components adhere to stringent quality control and compliance standards for implantable devices.
In this article, we explore the critical role of biocompatibility in implantable devices, why PCE is the superior process and E-Fab’s expertise in precision medical device manufacturing.

The Importance of Biocompatibility in Implantable Devices
Biocompatibility is the ability of a material to perform within the human body without causing harmful side effects or immune reactions.
For implantable devices like stents and pacemakers, materials must be non-toxic, non-corrosive, and able to integrate with biological tissues. Metals like titanium and stainless steel are commonly chosen because they meet these stringent requirements, offering both safety and durability for long-term use inside the body.
As the most compatible metal with the human body, medical-grade titanium is revolutionizing medical device manufacturing, with up to 80% of modern medical equipment utilizing this metal. Known for its exceptional corrosion resistance, strength, and lightweight properties, titanium is used in a variety of medical implants, from dental devices to artificial joints and MRI-safe components. This material’s ability to seamlessly integrate with human tissues reduces the risk of rejection, making it the ideal choice for critical devices that need to remain in the body for years.
Boasting more than 40 years of experience, the team at E-Fab specializes in delivering precision metal components tailored to the unique needs of our medical clients. We can tailor our photochemical etching processes to work with biocompatible materials such as titanium, stainless steel, and other medical-grade alloys, ensuring the components are safe for use within the human body.
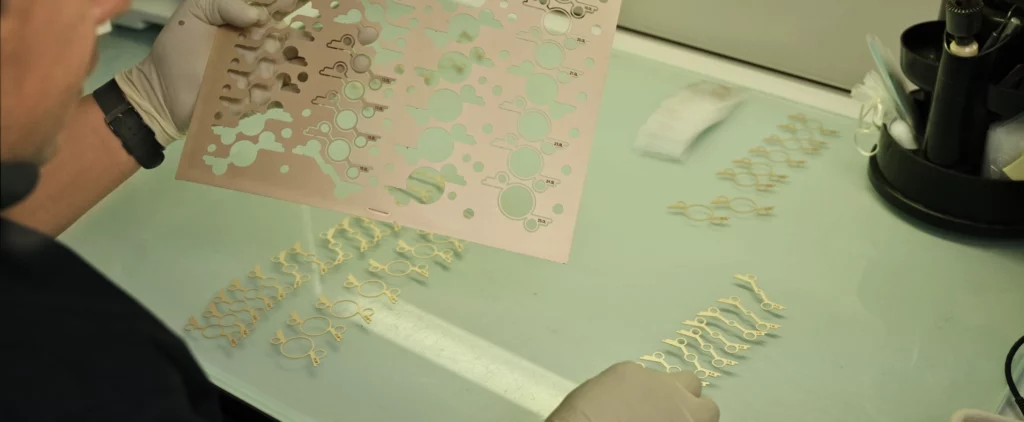
How Photochemical Etching Works for Implantable Devices
Photochemical etching (PCE) is a subtractive manufacturing process where a photoresist is applied to the surface of a metal sheet, followed by a selective etching process that removes unwanted material.
Unlike traditional machining methods like laser cutting or CNC machining, PCE is ideal for producing highly intricate and precise components without introducing stress or distortion to the material. This burr- and stress-free process ensures that implantable devices, such as stents, can be crafted to exact specifications, fitting seamlessly within the body while minimizing tissue damage.
At E-Fab, our advanced photochemical etching process delivers high-quality, burr-free, and smooth surfaces crucial for components like stents, catheters, and surgical instruments. It creates intricate and complex two-dimensional shapes, critical for components in medical equipment and implants designed to fit specific anatomical structures.
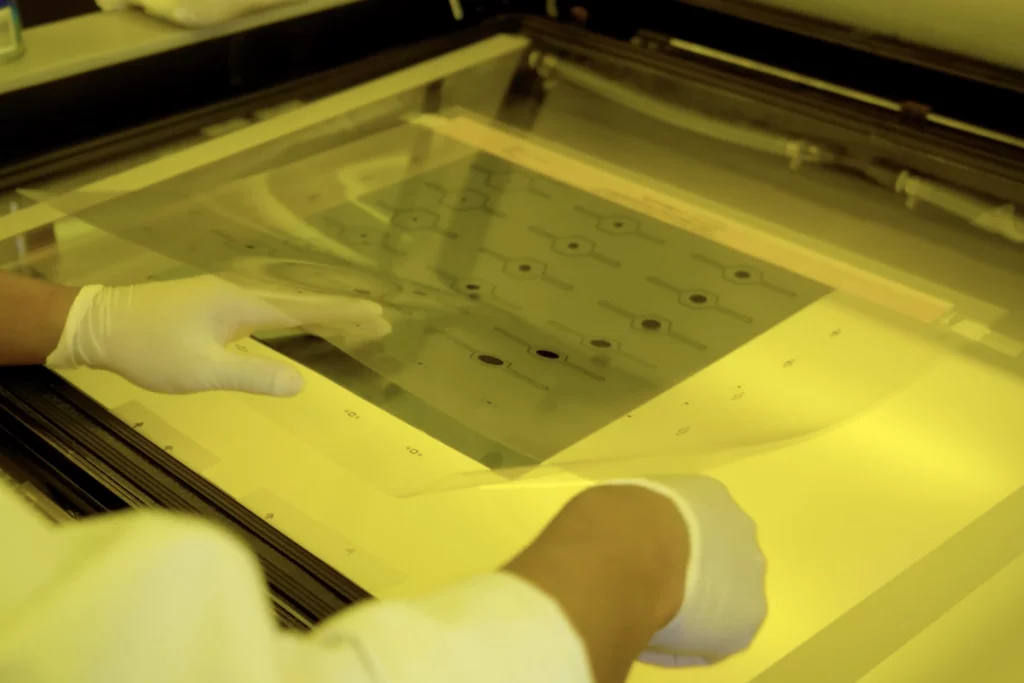
Key Benefits of Photochemical Etching for Medical Devices
When it comes to manufacturing medical devices, photochemical etching delivers a number of advantages over traditional machining methods. The main benefits include:
Precision: PCE offers unmatched precision, allowing for the production of components with tight tolerances and intricate geometries, which are crucial for devices like stents and pacemakers. The low-stress process maintains the structural integrity of materials like titanium without compromising its biocompatibility.
Customization: With PCE, manufacturers can rapidly prototype and create custom components tailored to specific medical needs. For example, custom stent sizes can be developed to suit individual patients, enhancing outcomes in minimally invasive procedures.
Biocompatibility and Material Integrity: The photochemical etching process preserves the biocompatibility of materials such as titanium and stainless steel, making it ideal for long-term implantable devices. The ability to maintain material properties while achieving precise designs ensures the devices are safe for prolonged contact with body tissues.
Working with E-Fab opens up even more benefits, like microfabrication and rapid prototyping. We can produce microscale and miniature components, which are increasingly important in minimally invasive surgical procedures, microfluidics, and lab-on-a-chip technologies. Our rapid prototyping capabilities are essential for developing and testing new medical devices and components before they enter mass production.
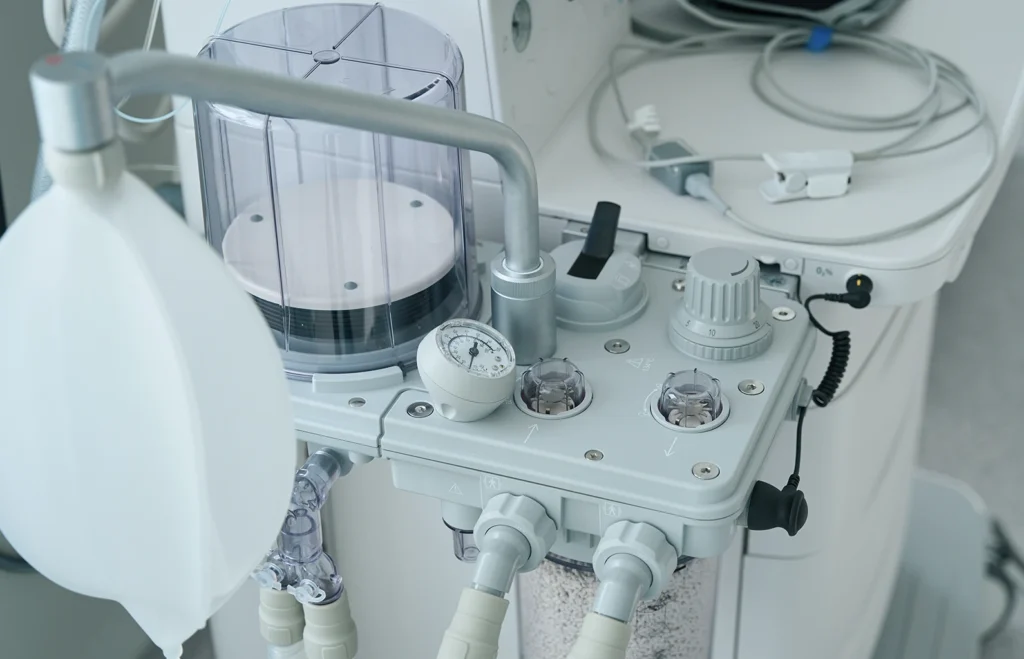
E-Fab’s Expertise in Precision Components for Medical Devices
With more than 40 years of experience, E-Fab has built a strong reputation as a trusted partner to the medical industry. It produces precision components that meet the stringent demands of implantable device manufacturing.
Our advanced photochemical etching process consistently delivers intricate, custom components with minimal material stress that optimize biocompatibility and ensure long-term functionality. ISO 9001:2015, ITAR, CMRT, and PCMI certified, we pride ourselves on quality, ensuring that every component produced adheres to the highest quality standards. Our team of Quality Assurance professionals analyzes every part we send out to ensure each meets technical specifications and precise requirements.
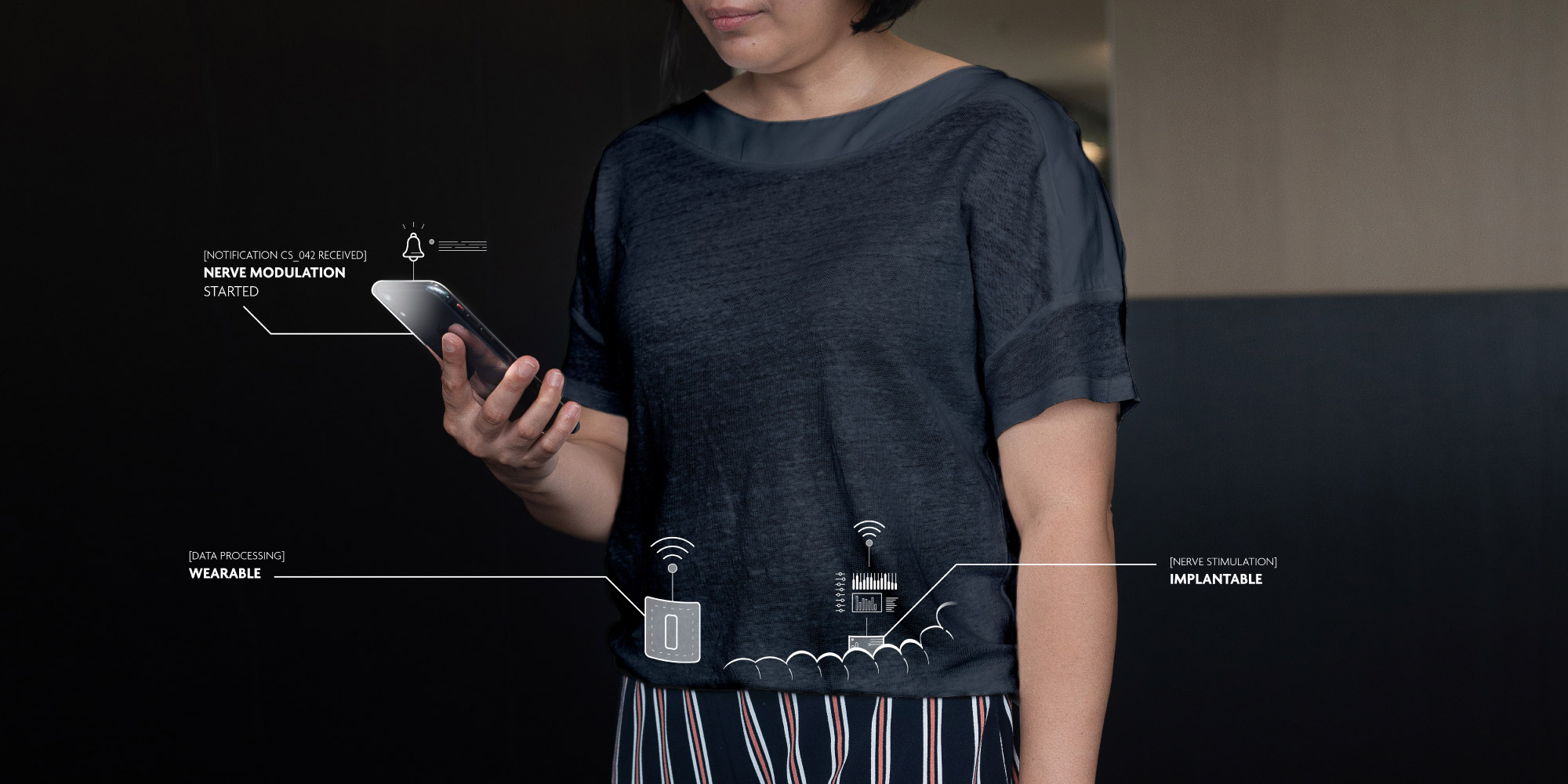
Innovations and the Future of Implantable Devices
As medical technology rapidly advances, new innovations in manufacturing processes like photochemical etching are paving the way for more precise and biocompatible implantable devices.
Continuous research and development in etching techniques, such as the non-HF etching process (known as the TiME process) for titanium alloys, further enhance the capabilities of this technology, leading to even safer and more effective medical devices.
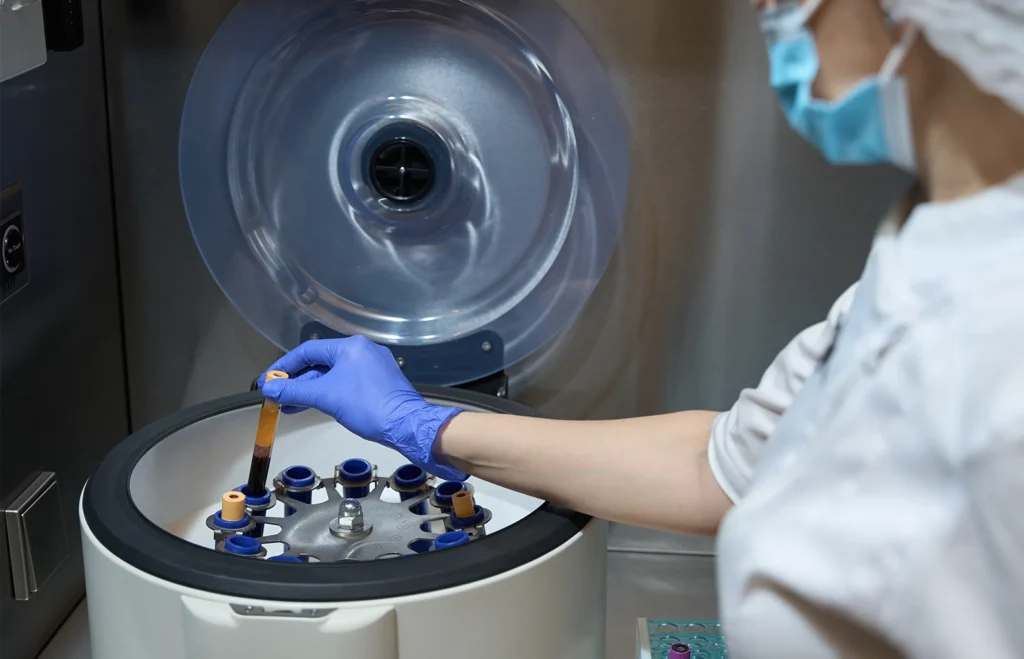
Component Manufacturing Transforming the Medical Industry
Medical technology continues to advance at a rapid rate, and biocompatibility and precision remain essential to the success of implantable devices.
With patient health and safety paramount, more and more manufacturers are turning to photochemical etching for these life-saving components, ensuring they meet the highest standards of accuracy and safety.
Blending innovation and collaboration, E-Fab is transforming the future of medical technology by providing customized, high-precision medical implant components that maximize performance and patient safety. With a commitment to quality, we ensure that your components are manufactured to the highest standards, enhancing the durability and functionality of your implantable devices.
If you need a proven manufacturing partner for etched parts in implantable devices, discover E-Fab’s experience and expertise in producing the next generation of medical technologies.