The quality of components in surgical devices directly impacts patient outcomes, so it’s critical to deliver the highest levels of precision during the manufacturing process.
In an industry where even the smallest component must be made to exacting standards, photochemical etching (PCE) has emerged as the trusted manufacturing process for surgical device components, providing an unmatched level of accuracy, flexibility, and compatibility.
Boasting over 40 years of experience, E-Fab is where ingenuity meets precision. In a field where precision is paramount, E-Fab leads the way in producing intricate surgical device parts critical for medical applications. Leaders in photochemical etching, we’re the trusted team for an industry that demands meticulous attention to detail throughout the manufacturing process.
In this article, we explore the important role of precision in the medical industry, the benefits of photochemical etching, and how E-Fab supports surgical device manufacturing with expert precision.
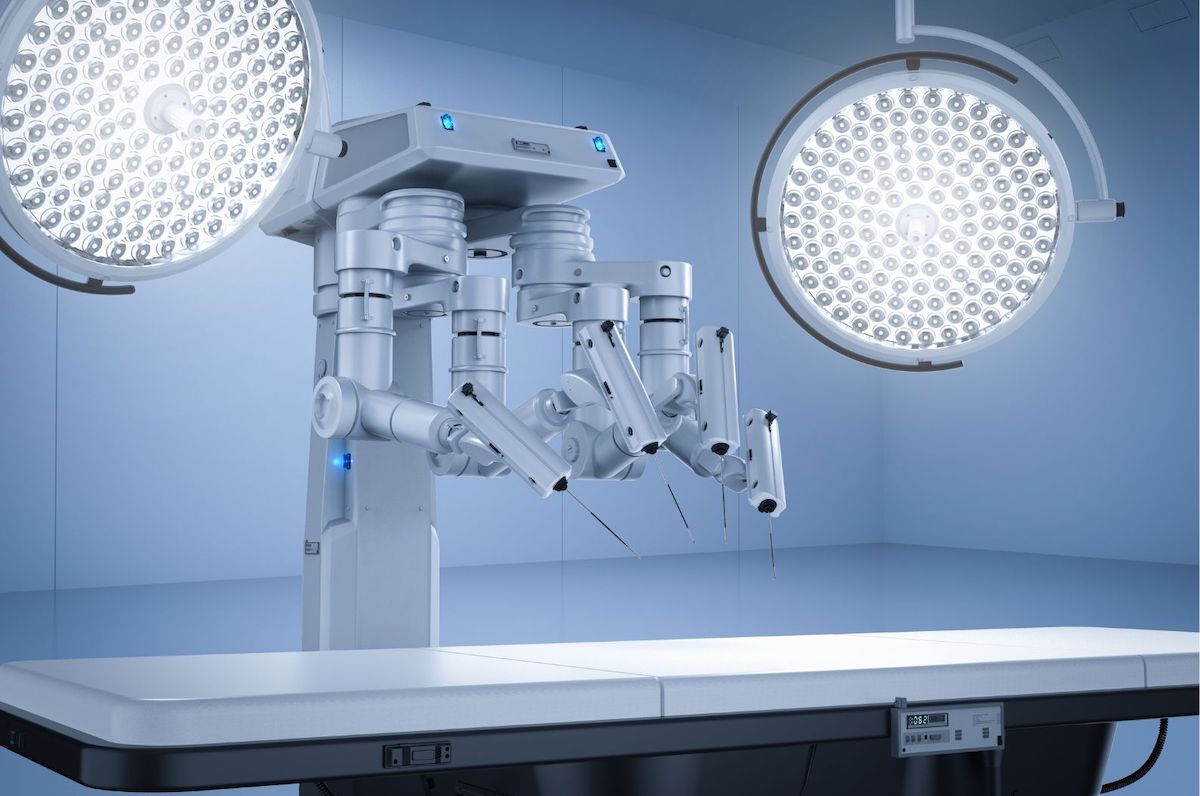
The Importance of Precision in Surgical Devices
In the fast-evolving world of modern medicine, surgical devices have remained critical tools for a wide range of medical procedures. Whether it’s a tool for minimally invasive surgery or a complex device for robotic-assisted operations, every component in these devices must meet stringent industry standards to ensure the health and safety of patients.
Traditional manufacturing methods, such as CNC machining or laser cutting, often struggle to meet the complex design requirements and fine tolerances necessary for advanced medical devices. Manufacturers also face the constant challenge of producing intricate and durable components without sacrificing precision – something that becomes even more challenging when working with biocompatible materials like stainless steel or titanium. That’s where photochemical etching excels.
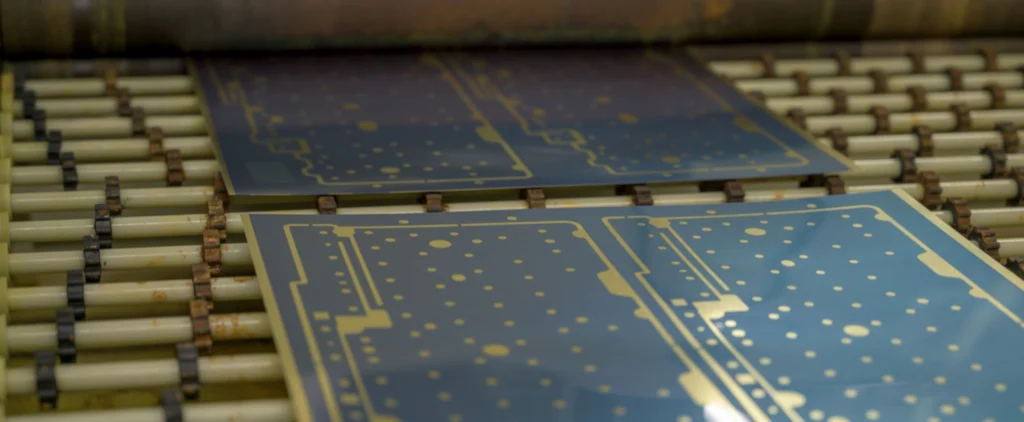
How Photochemical Etching Works
Photochemical etching is a precise, chemical-based process that produces intricate metal components used in applications across a wide range of industries. The process begins with a sheet of metal that is coated with a light-sensitive photoresist material. A mask is applied, and chemistry is used to etch away unwanted material, leaving behind a highly precise component that is stress free and burr free.
This innovative process offers several advantages over traditional manufacturing methods due to the accuracy and intricacy it provides. Photochemical etching can produce intricate designs with extremely fine details and tight tolerances, often as precise as ±0.001 in. This level of accuracy is crucial for producing small, complex components required in surgical devices. Unlike traditional machining, photochemical etching doesn’t apply mechanical force to the material, preserving the integrity of delicate metals and preventing warping, burrs, or distortion—ideal for sensitive medical applications. Additionally, unlike lasering, chemical etching does not produce any slag.
E-Fab is a leading provider of medical manufacturing services, consistently delivering photochemically- etched, high-precision components tailored to the industry’s unique requirements. Blending experience, expertise, and experimentation, our team of engineers, manufacturers, and quality assurance specialists produce a wide variety of precision metal medical parts that are durable, reliable, and accurate.
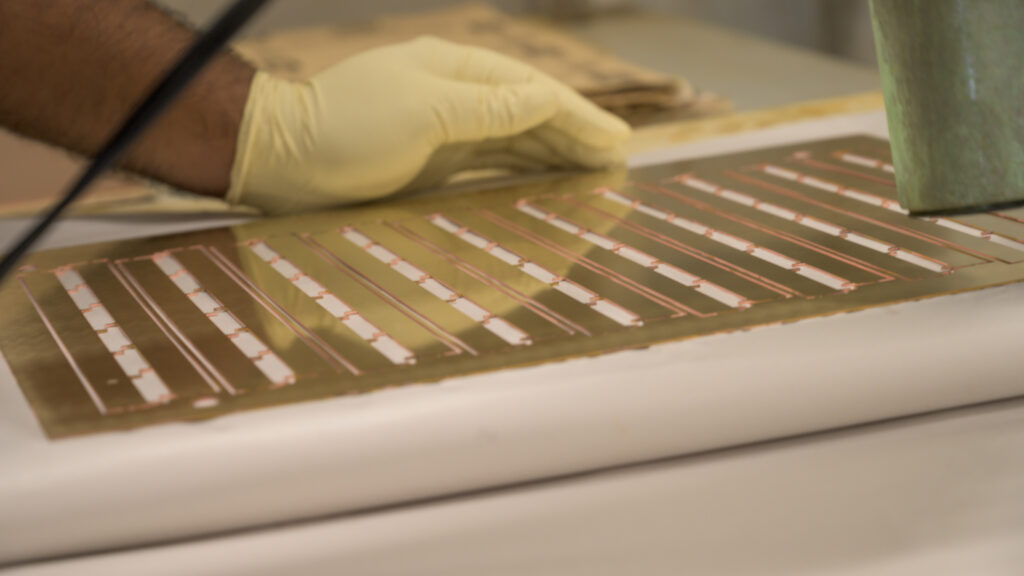
The Benefits of Photochemical Etching for Surgical Devices
Unmatched Accuracy
One of the most significant advantages of photochemical etching is its precision. The process can produce extremely fine details and tight tolerances, which are essential for creating the small, intricate components that surgical devices require. Components can be etched with tolerances as tight as ±0.001 in, making it possible to produce delicate parts that meet the exact specifications required for modern medical equipment.
Let’s take devices used in minimally invasive surgeries as an example. These small devices often require components with complex geometries and small tolerances. Photochemical etching ensures these parts are produced with the high precision they require to function reliably during critical procedures.
At E-Fab, our advanced photochemical etching techniques allow for the creation of intricate and complex two-dimensional shapes, critical for components in medical equipment and implants designed to fit specific anatomical structures.
Customization and Flexibility
When it comes to photochemical etching, customization is key. Because the process is mask-based and uses digital tooling, it allows for rapid prototyping and easy design modifications without the need for expensive tooling changes. This flexibility enables manufacturers to tailor components to the unique specifications of each surgical device.
Photochemical etching is also ideal for low to high-volume production runs, making it an efficient solution for creating custom components without the lengthy lead times associated with other manufacturing methods. Whether for specialized surgical tools or devices for specific procedures, the innovative process allows manufacturers to deliver components that meet highly customized needs.Etching is a sheet-based process, meaning the cost remains the same whether you produce 10 parts or 1,000 parts, as long as they fit on a single sheet of metal.
E-Fab has built a reputation for consistently producing precise fabrication of custom metal components with intricate designs and tight tolerances, perfect for use in various medical devices and equipment. Our customized solutions are tailored to each client’s unique needs, allowing for flexibility in design and the ability to produce complex geometries and intricate patterns.
Biocompatibility
Biocompatibility is a crucial consideration in the medical field, as surgical components must be made from materials that are safe for use in the human body. Fortunately, photochemical etching works with a wide range of biocompatible materials, such as stainless steel, titanium, and other medical-grade metals.
When processed through photochemical etching, these materials maintain their integrity and meet strict biocompatibility standards, ensuring they are safe for patient use. This makes PCE an excellent choice for manufacturing surgical components that are both precise and medically compliant.
Here at E-Fab, we can tailor our photochemical etching processes to work with biocompatible materials such as titanium, stainless steel, and other medical-grade alloys, ensuring the components are safe for use within the human body.

Cost Efficiency and Speed in Production
Photochemical etching (PCE) provides precision and customization and is a cost-effective manufacturing method. While traditional machining processes can be time-consuming and expensive, particularly for intricate components, PCE allows for faster production cycles without sacrificing quality.
By eliminating the need for expensive tooling and offering quicker turnaround times, photochemical etching delivers better ROI — especially for the production of small, intricate parts.
The team at E-Fab is renowned for helping medical manufacturers achieve cost efficiencies through the cost-effective medium to high-volume production of precision components.
E-Fab’s Expertise in Surgical Device Manufacturing
When you work with E-Fab, you’re leveraging over 40 years of expertise in the precision manufacturing of surgical device components. Our commitment to delivering high-quality, biocompatible, and customized components is what makes us a trusted partner for medical device manufacturers worldwide.
We take pride in our commitment to excellence and ensuring the highest quality standards throughout our manufacturing processes. To achieve this, we hold compliance certifications (ISO 9001:2015, ITAR, CMRT, and PCMI), ensuring all our components adhere to stringent quality control and compliance standards for medical devices.
Our state-of-the-art technological capabilities, which include advanced machinery, software, and equipment, enable us to deliver the high precision and efficiency needed to stay ahead in the competitive medical manufacturing landscape.
From rapid prototyping to full-scale production, E-Fab leverages the power of photochemical etching to deliver high-precision custom medical components that medical professionals can depend on.
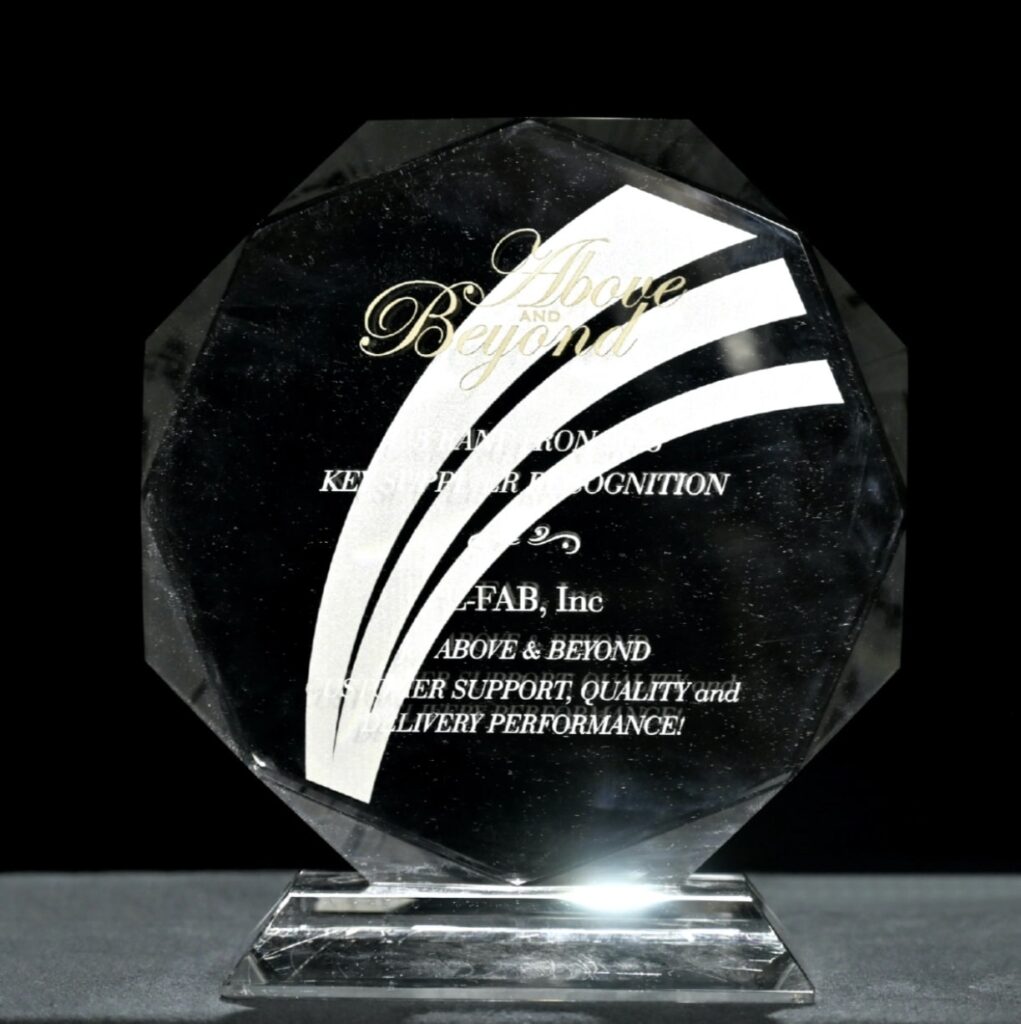
Leaders in Precision Medical Manufacturing
Offering unmatched accuracy, customization, and biocompatibility, photochemical etching is the ideal solution for producing precision components for a range of critical surgical devices.
As medical technology continues to evolve rapidly, the demand for precision is only set to grow, increasing the importance of partnering with a manufacturer that meets the highest standards of quality, precision, and compliance.
At E-Fab, we combine cutting-edge technology with decades of experience to deliver components that meet the stringent safety standards of the surgical industry. By partnering with us, you ensure that your medical components are manufactured to the highest standards, enhancing the efficacy and safety of your surgical devices.
Masters in medical device manufacturing, we work closely with clients throughout the entire project lifecycle. We continually invest in state-of-the-art technology, innovative processes, and rigorous testing to ensure accuracy and precision in every component we produce.
If you need a proven manufacturing partner for your surgical device components, discover E-Fab’s experience and expertise in producing the next generation of medical technologies.