In this article, we look at what makes PCE and molybdenum such a powerful combination, the key applications of chemically-etched molybdenum, and what makes E-Fab the trusted partner in molybdenum etching.
With a range of superior properties compared to other metals, molybdenum is a proven performer for a variety of industry applications. However, the true power of this transition metal is unlocked when paired with the advanced photochemical etching (PCE) process.
With the ability to produce precise, intricate designs without compromising the material’s inherent properties, PCE has become the preferred method for manufacturing advanced, precise molybdenum components that can withstand even the harshest environments.
E-Fab is a trusted leader in photochemical etching, boasting a proven track record in precision and expertise in molybdenum. Our advanced photochemical etching process enables us to deliver molybdenum components with complex or intricate geometries and tight tolerances for a range of leading industries.
In this article, we look at what makes PCE and molybdenum such a powerful combination, the key applications of chemically-etched molybdenum, and what makes E-Fab the trusted partner in molybdenum etching.

What is molybdenum?
Molybdenum is a versatile refractory metal and an essential element widely used in various industrial applications. Known for its high melting point, strength, low thermal expansion, and excellent thermal and electrical conductivity, molybdenum is often incorporated into steel alloys and stainless steels to enhance their performance and durability. Pure molybdenum is a silvery gray metal that is used in demanding environments due to its ability to withstand extreme temperatures and corrosion.
Molybdenum also exhibits multiple oxidation states, making it useful in a variety of chemical processes and applications.
Why Molybdenum is Ideal for PCE
Photochemical etching is a precise and efficient method for shaping metals, and this powerful process brings out the best in molybdenum’s unique properties.
This process is ideal for working with metals like molybdenum, offering high precision, repeatability, and the ability to produce complex geometries without inducing stress or altering the material’s properties.
From electronics and aerospace to medical devices and energy systems, photochemical etching ensures that molybdenum components meet the highest standards of performance and reliability, driving innovation and efficiency in critical applications.
Common Molybdenum Uses in Industry
With its ability to withstand extreme temperatures, photochemically etched molybdenum is relied on for high-precision applications across several industries.
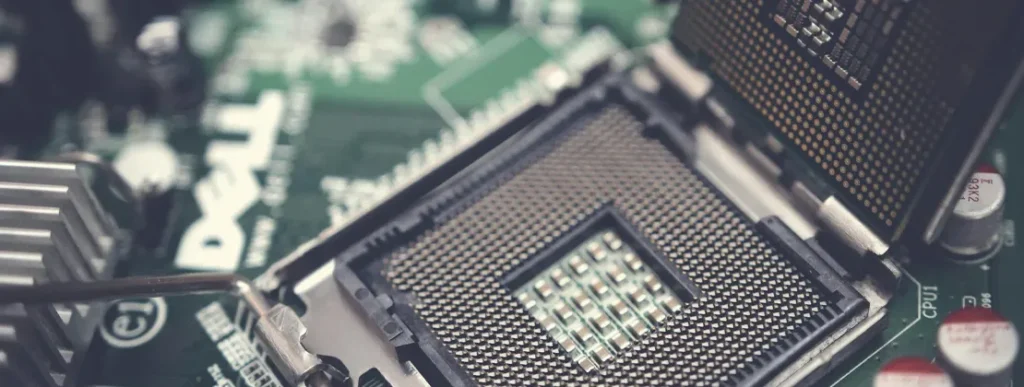
Electronics Industry
In the electronics industry, photochemical etching of molybdenum is crucial for manufacturing components such as shadow masks, contact springs, and connectors. The precision of photochemical etching ensures that these components meet the stringent specifications required for high-performance electronics.
Due to its excellent electrical conductivity and minimal thermal expansion, molybdenum is an ideal material for these applications, ensuring reliability and efficiency in electronic circuits and devices.
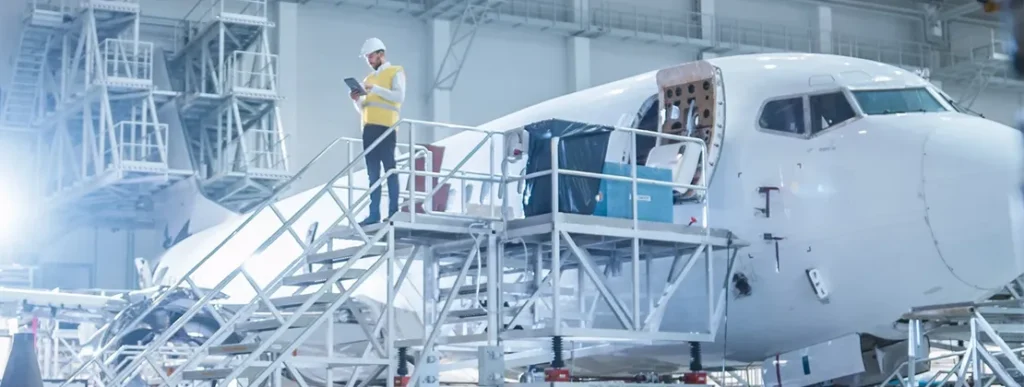
Aerospace Components
Aerospace applications demand materials that can withstand extreme conditions, and molybdenum fits the bill perfectly. Using the advanced photochemical etching process, thin, lightweight components such as control grids in TWTs, meshes, and heat shields can be produced with the precise tolerances and high strength-to-weight ratios required to perform in extreme environments.
The process allows for the production of intricate designs that can endure the harsh thermal and mechanical stresses encountered in aerospace environments, contributing to the overall performance and safety of aerospace systems.
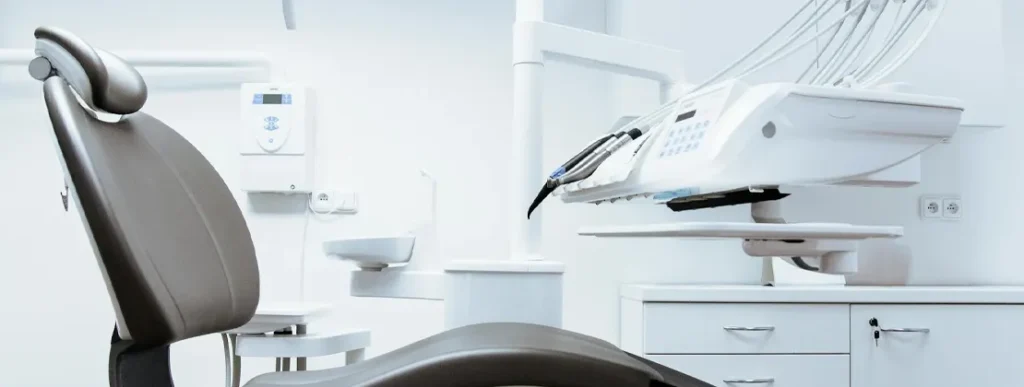
Medical Devices
The biocompatibility and durability of molybdenum make it the perfect metal for use in critical medical applications.
Photochemical etching is used to fabricate fine, detailed parts used in a variety of medical devices, including surgical instruments, radiation therapy components, and imaging equipment. The precision of this etching process ensures that the components meet the exacting standards necessary for medical applications, where even the slightest deviation can have significant consequences.
When it comes to imaging equipment where X-ray tube anodes are in operation, molybdenum is an excellent material selection because it boasts a high melting point and excellent thermal conductivity. Healthcare professionals’ ability to deliver more accurate and faster imaging helps patients and professionals alike.
Components fabricated from molybdenum and used in radiation therapy devices, like linear accelerators, can withstand high-energy radiation beams. The material helps these life-saving devices to direct radiation at target cancer cells and not surrounding healthy tissue, minimizing patient side effects and improving health outcomes.
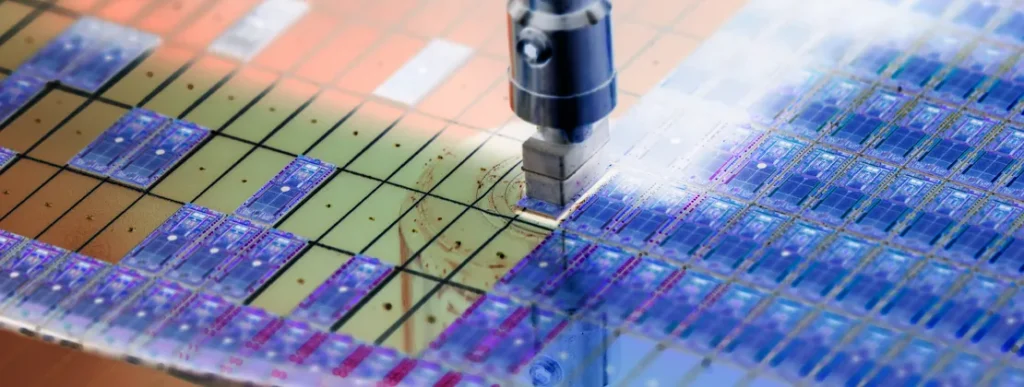
Semiconductor Manufacturing
Semiconductor manufacturing requires materials that can maintain integrity under high temperatures and corrosive environments. Due to its robust thermal and chemical properties, molybdenum is often used in semiconductor fabrication tools. Photochemical etching enables the creation of precise and intricate components, such as masks and grids, essential for the intricate processes involved in semiconductor manufacturing.
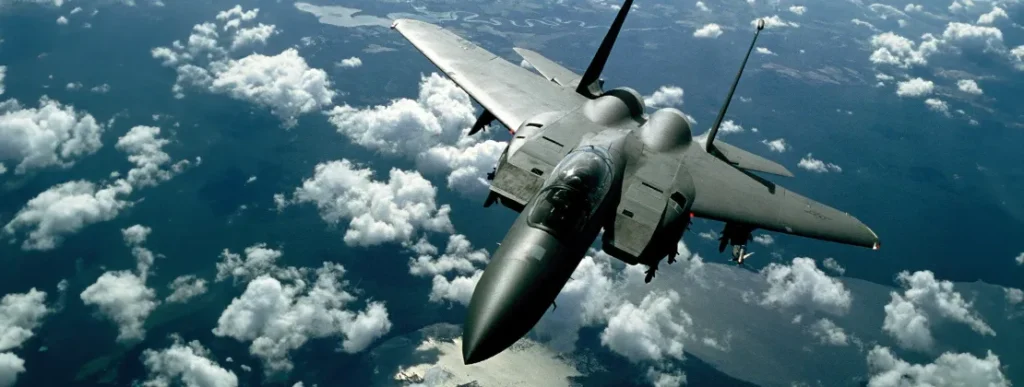
Defense Industry
Molybdenum’s high melting point and strength at elevated temperatures make it ideal for heat shields and structural components in military applications. Its superior corrosion resistance ensures longevity and reliability in the harsh environments encountered in defense industry applications.
E-Fab has built a reputation for delivering precision molybdenum parts for leading defense, aerospace, and energy companies. Some of the main components E-Fab delivers include:
Microwave Electronics
Molybdenum’s thermal and electrical conductivity make it ideal for microwave components like carriers and ribs. Its stability at high temperatures ensures consistent performance and reliability.
Electronic Beam Guns
Molybdenum’s high melting point and mechanical strength are crucial for the reliability and durability of components in electronic beam guns used in various industrial applications.
Ceramic Heaters
Molybdenum’s high-temperature tolerance makes it ideal for use in ceramic heaters and heating elements, as it maintains strength and stability in high-heat environments.
3D Grids
Molybdenum’s stability and strength, even at high temperatures, make it the perfect metal for manufacturing intricate 3D grids used for applications like traveling wave tubes. Its resistance to thermal deformation ensures accurate and reliable component performance.
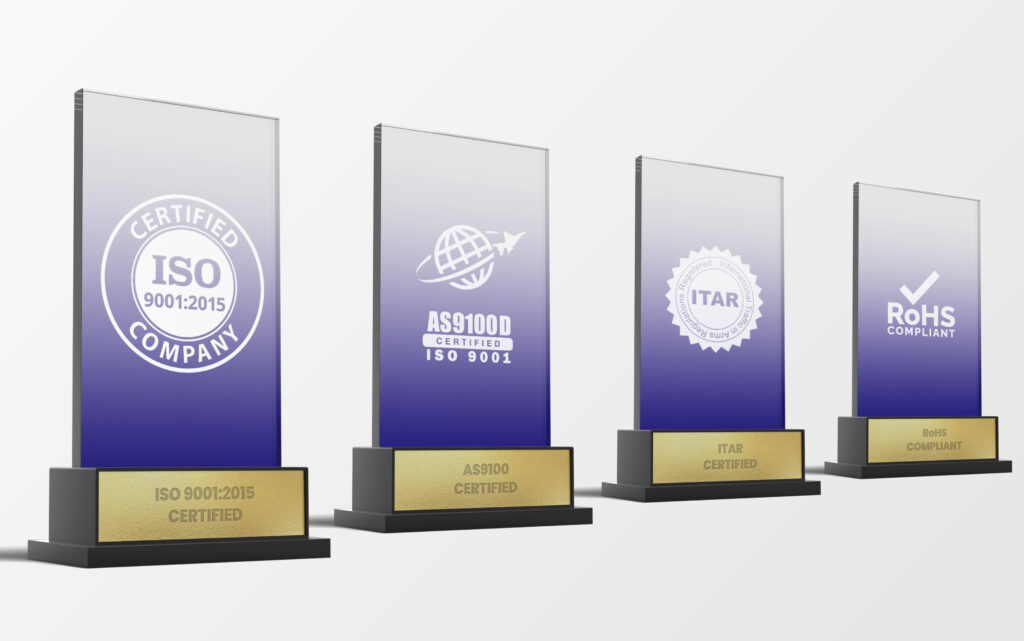
E-Fab: The Trusted Experts in Molybdenum Etching
As a trusted leader in photochemical etching, E-Fab is a leader in precision and expertise in molybdenum.
Our advanced photochemical etching process has been developed from years of experience in creating high-precision molybdenum parts. Led by our in-house experts, we can etch and form molybdenum to precise standards and specifications and consistently produce finer geometries with greater precision than the industry standard.
With a fast turn-around time, this etching process produces parts with exceptionally high dimensional tolerances, free from burrs, sharp edges, or the need for further finishing.
We are AS9100D-certified, ISO 9001:2015-certified, ITAR-registered, and RoHS-compliant, so you can rely on us for high-quality production.
Why Choose E-Fab for PCE of Molybdenum?
E-Fab is where ingenuity meets precision to answer our customer’s call for innovation. We deliver precise parts in the highest tolerances for applications that demand accuracy. Our secret lies in our proven multi-step process.
1. Design Evaluation/Engineering for Manufacturability
Before beginning the chemical etching process, our expert engineering team works directly with the customer to ensure the smooth and successful production of their precision metal parts. This includes using software such as AutoCAD to generate a repeating pattern from a customer file, which is then printed onto mylar film.
2. Sheet Metal Lamination
A dilute acid solution is used to clean the metal sheet once the material is chosen. After that, we laminate the metal sheet with a UV-sensitive dry film photoresist that acts as a mask, preventing the chemical etchant from coming into contact with areas of the metal that need to be retained for the correct geometry.
The photoresist must be well-bonded to the metal sheet to ensure accurate reproduction of the desired shape or pattern.
3. Digital Design
By using a UV laser digital imaging tool, the design is transferred to the photoresist laminated on the metal sheet from a digital image. Photoresist film can be applied on both sides of the metal sheet, and different designs can be etched.
After the image transfers the design to the metal sheet, the photoresist is developed, removing the exposed resist. We are now ready to etch the sheet.
View our Design Guidelines here for dimension and tolerance parameters.
4. Etch Design
Our etchers spray a chemical etchant, usually ferric chloride, simultaneously on both sides of the patterned sheet. High pressure is used to spray, etching away all unprotected material.
The final etched components are revealed after removing the remaining photoresist from the sheet.
Our skilled technicians and state-of-the-art machines meticulously control the time and the amount of etchant used for this process. They consider several factors, such as the type of metal,size and thickness of the metal sheet. Perfected etch times and processes guarantee etched parts that exceed your applications’ requirements every time.
5. All-Encompassing Turnkey Solutions
Once the chemical etching process is complete, we offer a range of value-added services to meet your design specifications and deliver a ready-to-use component.
For example, many applications require two parts to be joined to create a ready-to-use metal component. Once a 2D component is photochemically etched, as described above, we can use brazing or diffusion bonding to join it to another CNC-machined part to form a 3D component.
In addition to machining any special features you may require in the metal components with our Haas CNC Milling Machine, we also offer comprehensive plating services to enhance the durability and performance of your parts. Our surface finishing capabilities include electropolishing and passivation, ensuring that your components meet the highest standards of quality and aesthetic appeal.
6. Quality Control
Following the removal of the photoresist layer (either manually or with a stripping machine), parts are rinsed before being separated. The individual parts etched on each sheet can be separated or left with tabs on the sheet.
We recommend tabbing to allow for faster inspection and safer handling during and after production. For this, a tab is connected to the individual parts so that they stay on the sheet for easy removal after manufacturing is complete.
During the chemical metal etching process, our quality inspectors review and check each part to ensure it meets the dimensional requirements and tolerances specified at the design stage.
The Future of Photochemically Etched Molybdenum
As the demand for high-precision, lightweight, and durable components continues to grow, particularly in aerospace, electronics, and medical sectors, so will the need for photochemically etched molybdenum.
With the growing emphasis on miniaturization and high-performance materials in emerging technologies, photochemically etched molybdenum’s role in future applications is set to expand. This will put greater pressure on world production and emphasize the importance of working with a manufacturer with a proven track record of experience and expertise in the photochemical etching of molybdenum.
Here at E-Fab, we’ve manufactured the highest-quality precision components and assemblies specifically designed for mission-critical applications for over 50 years. We are committed to delivering best-in-class components at quick turnaround times using our advanced chemical etching process for metal parts.
Our precision molybdenum components power leading-edge technology companies, defense contractors, and medical equipment manufacturers and innovators. With collaboration at our core, we take your product from design and concept to prototyping through full production with fast and reliable delivery.
If you’re searching for a proven photochemical etching partner for your molybdenum project, our team is here and ready to start talking, whatever your application may be.
Get in touch today to discuss a project or idea or request a quote